US Car Parts Supplier Optimises with New WMS
11th November 2019
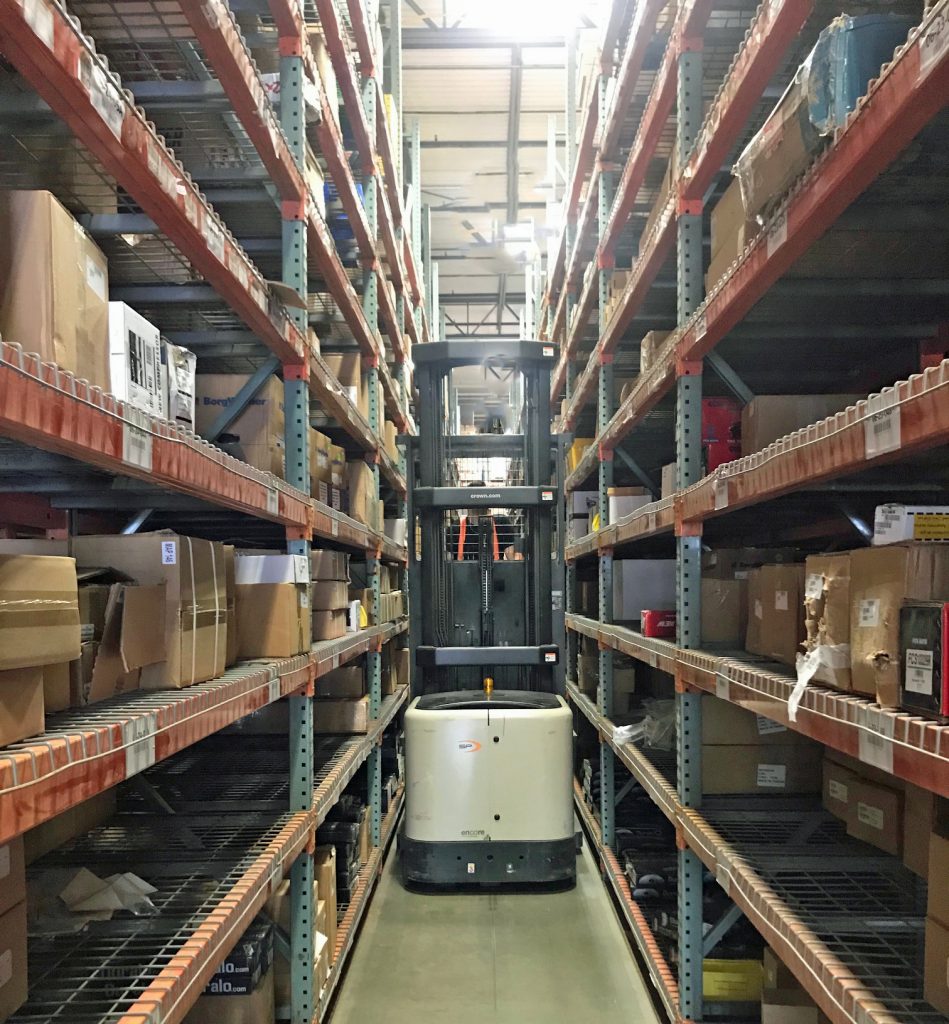
A leading US online auto parts supplier and distributor is optimising inventory, space and resources within its fulfilment center, via a WMS supplied by SnapFulfil.
San Diego-based Buy Auto Parts operates in a highly competitive and aggressive market place where shipping the right part quickly, first time and on time is critical – and straight away the ROI from its new SnapFulfil Tier 1 WMS has seen efficiency-driving picks per hour increase by more than 50% since implementation.
“One of the biggest areas it’s helped improve is our pick, pack and ship operational efficiencies and the ability to wave orders,” says John Salvatore, vice president of Buy Auto Parts operations. “Being able to wave an order by its due-out date is a huge advantage if, for example, I want to wave my next-day air, international, urgent orders or Amazon orders. I can now prioritise them as I want.”
With a cloud-based WMS, Buy Auto Parts can also better manage their non-traditional summer peak season by maintaining deeper visibility into inventory levels and process efficiencies. This is especially helpful for bulkier inventory such as radiators, air conditioning compressors and wheel hub assemblies, plus other parts where they don’t carry large amounts of stock.
Mr Salvatore adds: “When the same item is housed in different areas of the warehouse, SnapFulfil picks from the lowest inventory level to the highest, so managers can better monitor supply levels. It intuitively knows, for example, to pick a carburetor from a stock of one rather than a carburetor from a stock of 10, thus maximising available space.”
Future plans include improving reverse logistics operations using the WMS, because some of the company’s products have several components – and it wants to be able to shorten the time items are re-stocked so customer refunds can be issued in a timely manner.
Additionally, Buy Auto Parts is working with SnapFulfil to create an enhanced inventory cycle count program, so it can enhance inventory accuracy to better serve its growing customer base and their ever-increasing delivery demands.
SnapFulfil MD, Tony Dobson, explains: “Managing a strong reverse logistics operation requires a healthy set of technology-driven automated procedures and systems, because they capture and evaluate increasingly important data sets from every step in the process. Being cloud-based, SnapFulfil offers immense flexibility to handle dynamic return operations as well as easy integration with other company systems to facilitate a much more holistic return operation.
“Another of SnapFulfil’s major benefits is the immediate productivity improvements made possible by the system’s automated task management functionality. In addition to accurately recording and verifying inbound goods at both receiving and put-away, it also drives a rolling inventory count allowing any discrepancies to be identified in a timely manner and records adjusted accordingly to maintain the highest levels of stock accuracy and integrity.”