Eisenwerk Martinlamitz (EWM) relies on tough materials handling equipment from Hyster
31st August 2015
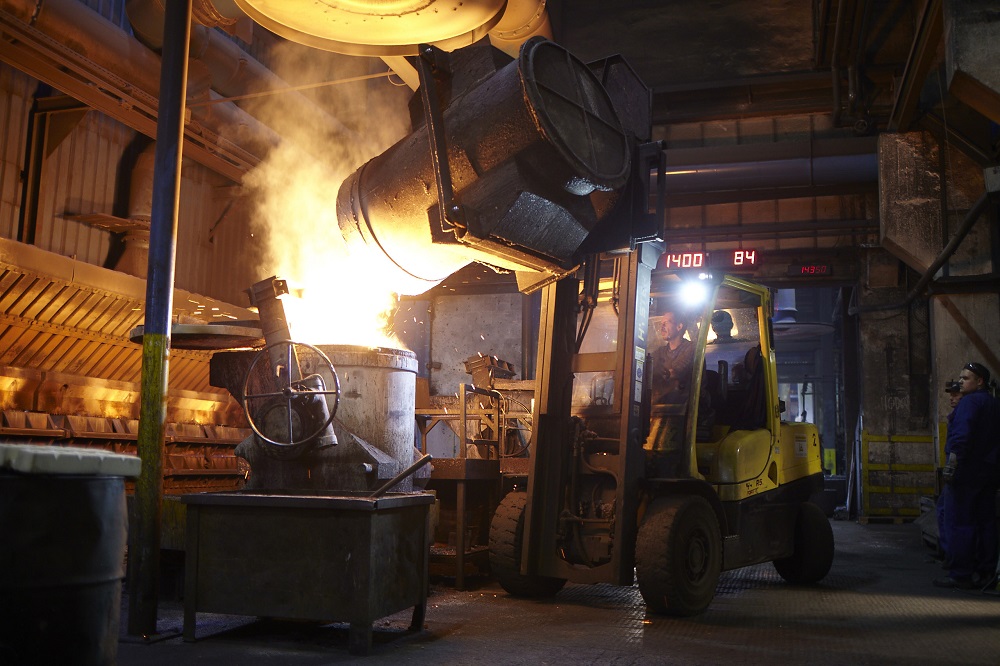
After several years of testing, Eisenwerk Martinlamitz now exclusively relies on the robust materials handling equipment from Hyster, which is designed specifically for use in iron and steel works. The specially-equipped forklift trucks can withstand the heat of the furnace in the plant and can be used where space is limited.
Located outside Schwarzenbach, on the Saale River near the Czech border, ironworks operation Martinlamitz (EWM) sells more than 50,000 tonnes of cast metal annually. This metal is used for axles on agricultural and construction equipment, commercial vehicles and railways, transmission housings and parts for wind turbines, crane and maritime engineering on to feet, arms and joints for robots. The foundry delivered the axles used for the high-speed trains deployed for the Winter Olympics in Sochi, Russia.
Historical documents reveal that one of Europe’s oldest hammer forges existed in Martinlamitz in 1200AD, and today’s foundry derives from this. Today, EWM supplies grey cast iron and modular cast iron parts to more than 21 countries around the world, including Korea, India and China.
Hyster forklift trucks receive special equipment
The EWM company site is steeped in tradition and places special demands on logistics. In particular, the company requires powerful and manoeuvrable forklift trucks that are capable of transporting cargo containing hot molten mass, with temperatures of up to 1,400 degrees in the 1.8 tonne ladles around its narrow factory halls.
Today, EWM uses Hyster Fortens H4.0-5.5FT series forklift trucks with a 5.5 tonne lifting capacity and a 600 millimetre load centre of gravity.
“The Hyster forklift trucks are especially manoeuvrable and robust, so they can also withstand the tough operating conditions“, EWM Managing Director, Barry Thomas Irvin, explains.
The forklift trucks’ DuraMatchTM transmission prevents sudden braking, for example, and controls the direction of travel to ease the load placed on the brakes and tyres. The forklift trucks drive with super-elastic tyres, which are robust enough to also compensate for uneven ground and floor surfaces. Hyster also improved the stability mechanism (HSM) for lateral stability, without compromising the ride on uneven surfaces.
Additional oil cooler and temperature-resistant hydraulics
In order to withstand the high temperatures of the melting furnace, the forklift trucks required to operate in that area are equipped with an additional oil cooler and temperature-resistant hydraulic hoses. Additional filter systems reduce dust accumulation, prolonging the service life. Reduced maintenance and oil-immersed multi-disc brakes also increase the reliability of the Hyster material handling equipment. Special attachments, such as a rotating fork clamp that can handle loads of up to four tonnes, ensure reliable operation. With these special adaptions to the forklift trucks, the hot, molten mass can be transported directly from the oven to the mould casting facility where it is processed. EWM has two ovens, each with a capacity of 16 tonnes that alternately produce 280 tonnes of cast metal daily. This production requires 50 million kilowatt hours of electricity, which is the equivalent of a small town.
EWM: punctuality and quality count
“In recent years we have invested several million euros in the expansion of our foundry”, says Barry Thomas Irvin.
Today, EWM has a fully-automated HWS Seiatsu mould casting facility for mould dimensions of 1200 mm x 800 mm x 320/320 mm. This enables a casting output of 120 mould castings per hour at peak time. Additionally, an investment was made in a new paint shop that works with water-soluble paints.
“Our strengths are our punctuality and especially our quality. That is why we also focus on reliable logistics solutions”, says Barry Thomas Irvin.
EWM has a fleet of 52 Hyster material handling vehicles. The entire logistics chain from the delivery of goods and materials to the transport of the molten mass and castings within the plant, on to the loading of the finished parts is all handled by Hyster forklift trucks. The fleet includes high-lift trucks with and without a platform, Hyster J1.5 -2.0XNT energy-efficient 3 wheel electric counterbalanced trucks with 1.5 to 1.6 tonnes of lifting capacity, Hyster J2.2 -3.5XN compact 4 wheel counterbalanced trucks with 3 to 3.5 tonnes of lifting capacity, and Hyster ICE forklift trucks with 1.6 to 5.5 tonnes of lifting capacity. All the forklift trucks feature a robust and compact chassis design, especially durable and reliable components, as well as low operating costs.
Reliable solutions for outdoor use
The Martinlamitz ironworks now primarily deploys Hyster electric forklift trucks for outside use.
“This is rather atypical,” says Hyster dealer Jochen Kotschenreuther, who has supported the foundry for many years. “Usually electric forklift trucks are used for emission-free operation indoors.”
EWM took a different approach and first tested the use of the electric forklift trucks outdoors. The results showed that the Hyster electric forklift trucks are robust and meet EWM’s tough demands even when used in outdoor areas for loading and unloading. In addition to this, the use of electric forklift trucks is financially viable despite the higher purchase costs. This is due to the electric forklift trucks having significantly lower operating costs and requiring less maintenance.
“Electric forklift trucks perform just as well as trucks equipped with internal combustion engines. That is why it makes sense to use them in many areas today that formerly were the domain of diesel trucks,” explains Jochen Kotschenreuther.
The robust Hyster forklift trucks are in service for approximately 18,000 operating hours in their ‘first life’ at EWM. Afterwards, they are refurbished and deployed in less demanding operating areas. To ensure that they are always ready for use during this period, Jochen Kotschenreuther has a technician permanently on-site to maintain the machines. For the Martinlamitz ironworks, reliability and punctuality have highest priority in the entire process chain.
Visit www.hyster.eu.