KNAPP Picking Robot Named Best Product at LogiMAT 2017
31st March 2017
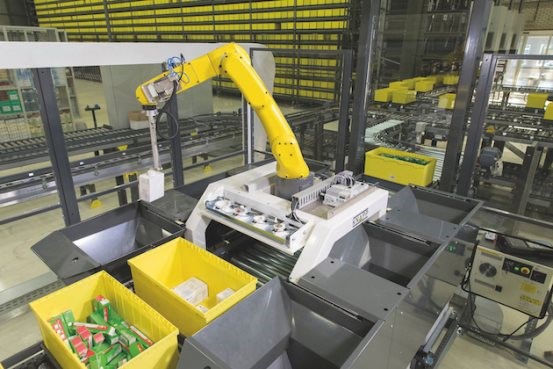
With warehouse staff reaching their performance limits in processes that demand high performance and quality for long periods of time, one solution is the use of industrial robots. Achieving reliable robotic picking had been considered an insurmountable task but KNAPP’s Pick-it-Easy Robot has made this a reality – and the solution has just scooped the Best Product award at the LogiMAT 2017 exhibition in Stuttgart.
Designed to handle a wide range of articles in applications where consistently high throughput is required, KNAPP’s Pick-it-Easy Robot is a goods-to person picking system that is suitable for various business sectors and sales channels. Robotic and manual workstations can be easily combined to make best possible use of their individual assets. The robot cell offers particular advantages to companies with multi-shift operation that are striving to reduce errors and the associated costs.
Sophisticated image recognition and processing software detects the target article in the source container and calculates the optimal grip point on the article’s surface. The six-axis articulated arm robot positions the gripper precisely over the grip point, with the flexible gripper able to pick articles lying in any position in the source container. Constantly monitored by sensors, the system picks up the article and transfers it safely into the target container. The Pick-it-Easy Robot complies with all safety standards and guidelines.
In continuous use, the Pick-it-Easy Robot attains a significant increase in productivity, while maintaining consistently high quality in comparison to manual picking. An ideally designed goods-to-person workstation can process 1000 lines per hour; over a longer period, however, such performance is not possible for the human workforce. The Pick-it-Easy Robot is a sensible alternative to humans in warehouse areas that demand continuous high throughput; depending on order structure, article range and capacity peaks, a robot cell can replace one or more manual workstations. If, for example, a manual workstation with two-shift operation is replaced, the payback period for the Pick-it-Easy Robot is very short.
KNAPP’s zero defect warehouse philosophy, based on modern image processing and recognition technologies, has been incorporated in the development of the Pick-it-Easy Robot. The work process is monitored by several sensor systems, with any errors being detected and corrected automatically or, if necessary, forwarded to a manual workstation. The cost of errors is considerably reduced and delivery quality is enhanced. The safety devices and sensor systems guarantee the safety of personnel and prevent material damage. The Pick-it-Easy Robot offers a high level of flexibility and simple integration into existing systems, with the ability to process various types of container. The arrangement of the articles in the container is flexible – both chaotic and stacked articles can be handled smoothly, as the Pick-it-Easy Robot always finds the ideal gripping point for each item.
With its Pick-it-Easy Robot, KNAPP is taking an important step into the Industry 4.0 era. The robot has become the co-worker, or ‘cobot’; with the Pick-it-Easy Robot, better distribution of the workload and up to a fourfold increase in productivity are achievable. Retrofitting and integration of the robot into existing intralogistics systems is also possible. With the Pick-it-Easy Robot, KNAPP has added a valuable solution component for the zero defect warehouse, its concept of an intelligent and networked site.