Zero Waste to Landfill for Thermo King Galway Manufacturing Facility
17th August 2017
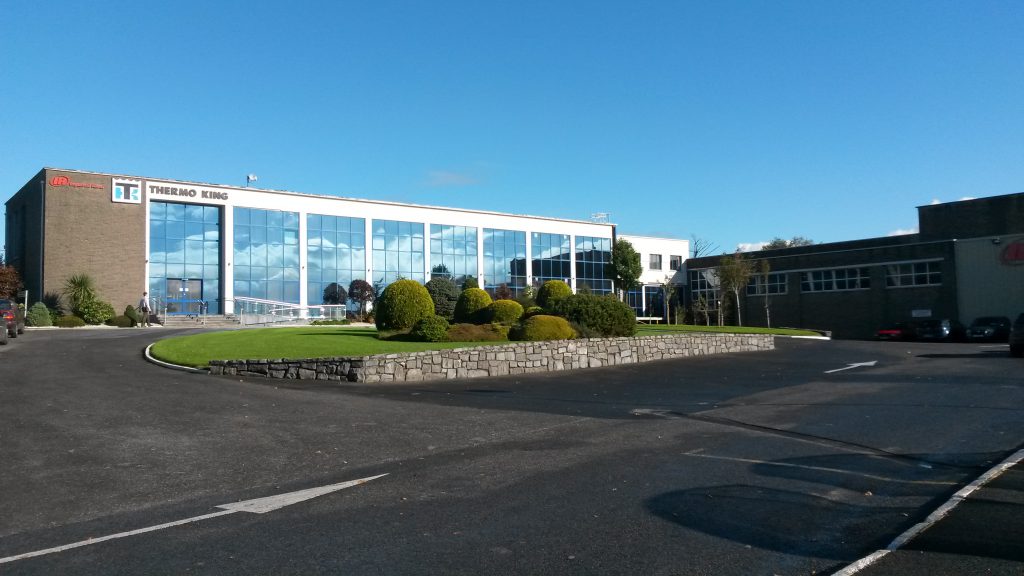
The Galway, Ireland manufacturing facility of Thermo King®, a manufacturer of transport temperature control solutions for a variety of mobile applications and a brand of Ingersoll Rand, became one of the first Ingersoll Rand sites to manage zero waste to landfill.
The sustainability push in the Thermo King Galway factory builds on the Ingersoll Rand Climate Commitment made in September 2014 to, among others, reduce greenhouse gas emissions (GHG) related to its operations by approximately 35 percent reduce by 2020.
Thermo King Galway is one of the brand’s most important manufacturing facilities. It currently employs more than 500 people, who build a wide range of Thermo King truck and trailer refrigeration units. Before achieving the zero waste milestone, the facility sent 230 tonnes of waste to landfill every year. Today, everything at the Galway site is recyclable, and recycling waste generated at the production stations like metal, plastic, cardboard or wood is part of standard work at the facility.
“Measures implemented at Galway have been effective and show that environmental sustainability is the right call for everyone, including our bottom line,” said Cormac Mac Donncha, operations director at Thermo King. “For example, we switched from using wooden pallets to reusable steel pallets for shipping finished product. This keeps pallets out of landfills, avoids the cost of recycling them and saves the facility over one million Euros each year.”
Notwithstanding, the Thermo King Galway facility continues their efforts to further improve the sustainability of their operations.
Most recent improvement is the installation of a rainwater harvesting facility to collect rainwater from the building’s 200,000-square-foot roof. The rainwater is used for toilet flushing and reduces the facility’s water usage by 50,000 litres (13,200 gallons) per month.
“The work doesn’t stop just because we’ve reached our zero waste to landfill goal. This is an ongoing process. We continue to look for alternative recycling methods and opportunities to further reduce our impact on the environment,” said Mac Donncha.