Hyster Reduces Handling Costs for Paper Recyclers
29th August 2017
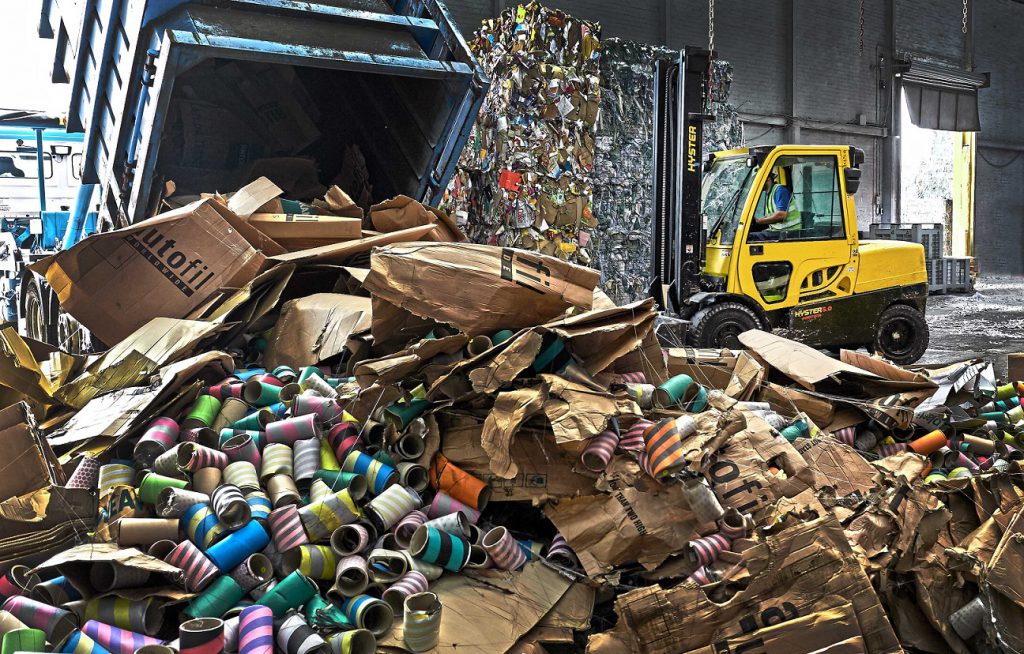
In 2015, collection and recycling in Europe increased by almost one million tonnes of paper* in just 5 years. As the industry continues to grow, Hyster Europe claims that it can help even the most intensive paper recycling operations reduce cost and maximise efficiency.
“Paper recycling applications present many particular materials handling challenges,” says David Reeve, Industry Manager for Hyster Europe. “Operations need high quality trucks that are tough enough to avoid downtime and unplanned maintenance costs.”
Materials handling equipment used in the paper recycling industry is often required to operate on uneven ground, for long hours and in dirty and dusty environments indoors and outdoors, all at optimal efficiency. Furthermore, specialised attachments are often required to handle the paper bales which can absorb rain water resulting in additional weight.
“Recycling businesses are no longer restricted to only using tough ICE trucks,” says David. “Hyster® electric trucks are tough enough for most recycling operations, but as with any application, the choice depends on how the trucks will be used.”
Choose Tough Electric Trucks
Switching to electric trucks can ensure zero-emissions and reduce energy costs, something that interests many recycling firms with a focus on sustainability. With fewer required maintenance intervals and less wear, it may also reduce maintenance costs.
“While electric trucks can have an acquisition price of up to 20% more than ICE trucks, the reduced operating costs delivered means that the investment can be recovered over a contract period,” adds David.
Hyster is well known for producing tough trucks and the electric forklift range is no exception. Built for both indoor and outdoor use, a weatherproof all-steel cab provides operator comfort even in the dirty, dusty environment of a paper recycling application.
“Operators frequently have to chisel loads out from tightly packed bales on a vehicle,” says David. “These trucks are built for such operations which can cause massive shock loadings to the attachment, mast rollers and carriage. We can even add built in load weight indicators to give the operator reassurance when lifting uncertain load weights.
“In some cases, however, lead-acid or lithium-ion battery options may be quickly discounted as there simply may not be enough power to provide the necessary operating hours each day,” David continues. “Therefore, diesel or LPG options may achieve a lower total cost of ownership compared to electric trucks.”
Choose ICE Cool Trucks
Some of main problems of using a standard ICE truck in a recycling application include engines overheating and radiators getting clogged up due to dust, dirt and debris in the environment. Indoor waste paper stores also tend to have poor air circulation and are often confined spaces. The heavy-duty banding wire is another common issue if not carefully disposed of. It can be picked up and transferred to the transmission and axle of the fork lift truck during travel risking damage to exposed truck components. This costs businesses money in downtime and regular maintenance.
The Hyster® ‘Cool Truck’ is a lift truck option specially designed to overcome these challenges, enhancing efficiency and reducing costs. Oil immersed brakes also help keep brakes and tyres cool in short shuttle or long run applications whilst preventing the ingress of paper debris into the braking system.
“The Cool Truck is designed to enhance efficiency and reduce unnecessary expenditure specifically in the difficult environments of paper and recycling plants,” explains David.
Options include a fully enclosed frame and vented hoods, side panels and radiator covers to reduce the vacuuming of dirt and debris from the floor into the engine. The ‘Cool Truck’, which is available as a modification both on Hyster® Fortens® lift trucks and heavy duty forklifts, has also been developed for use with a wide range of attachments, so can be tailored to suit specific applications.
The Hyster® Duramatch transmission assists bulldozing applications. Its integrated Auto Deceleration System can reduce brake and tyre wear by up to 50% and Controlled Power Reversal reduces shocks through the transmission and helps prolong tyre life. The Hyster® DuraMatch transmission electronically controls braking, direction changes and ensures the truck operates smoothly.
Hyster® electric counterbalance trucks from 1.3 – 3.5 tonne capacity, and ICE counterbalance lift trucks from 1.6 – 5.5 tonne capacity are built by Hyster in its factory in Craigavon, Northern Ireland to the highest quality standards. Strict quality measures and testing help to ensure durability in the most demanding paper recycling operations, with, for instance, more durable paintwork, highly tested components and robust tyres.
Extensive research and testing with paper recycling industry customers also helps to feed the design objectives of Hyster® trucks, ensuring the focus is on what owners and operators want and need. Quality service and maintenance support from the global network of local distribution partners is also key to a low cost of ownership.
“Intelligently designed Hyster® forklift trucks are tough enough to support operational demands while delivering a low cost of operation,” adds David. “However, for maximum efficiency, we can help businesses identify which truck is the right choice to meet their specific application needs.”