AGVs in Operation: Meat and Drink for Multi-Destination Bot
12th March 2018
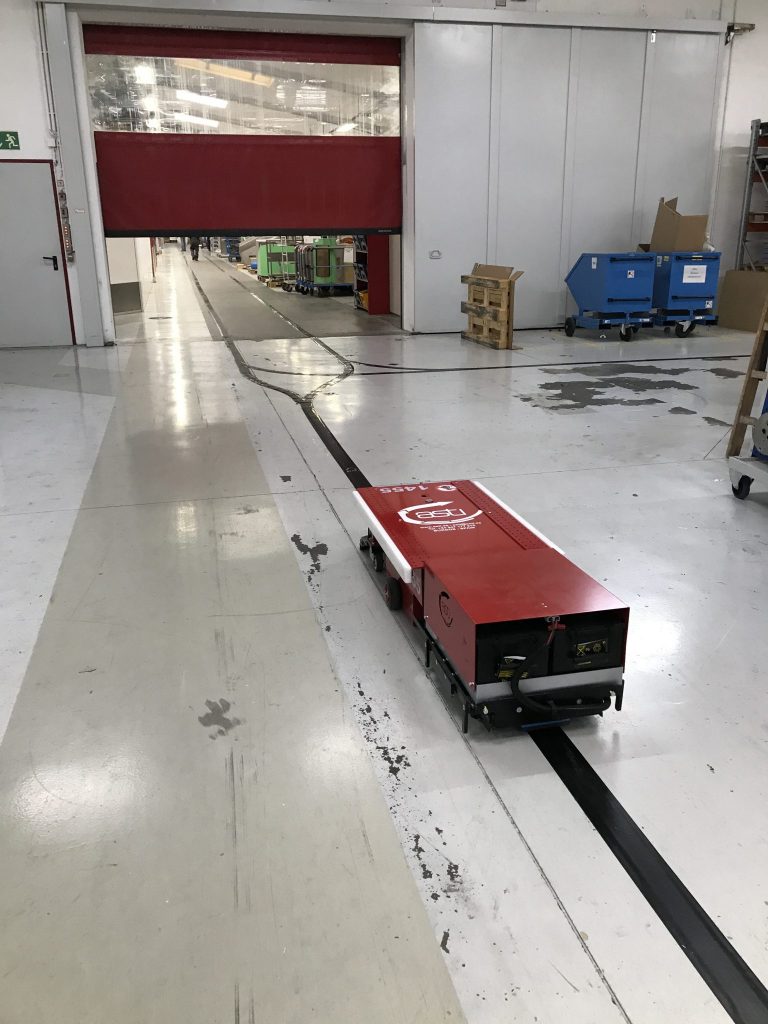
As soon as an operator at TREIF, a German manufacturer of bread- and meat-processing equipment, gives an order, the automated guided vehicles (AGVS) built by ASTI Mobile Robotics go into operation on the 500-metre circuit set up in the Maschinenbau GmbH plant in Oberlahr (Germany). On leaving their station, the first thing the autonomous robots encounter is a fork in the track, with one route leading left and the other right. They automatically choose the one that, depending on their destination, optimises their trip to the cart pick-up station. Now comes the second choice — to pick up a cart or not? It all depends on the order received. The vehicles then encounter another fork in the track: left or right? One side leads to three cart stations, the other is longer and leads to the opposite end of the factory where the system’s seven other stations are located. Once the task has been completed, the AGV returns to the queue and waits to receive the next order.
ASTI Mobile Robotics’ autonomous robots repeat the cycle 80-150 times a day on average at TREIF. The German firm’s employees monitor the production processes and let the AGVs do the routine physical work — collecting the loaded or empty carts — leaving the operators free to focus on their core task: making machinery.
The German company, founded in 1948 and a leader in its sector, was keen to fine-tune its manufacturing operations, closely monitor repetitive tasks and processes and maximise staff safety. With these goals in mind, it contacted ASTI Mobile Robotics, the European market’s leading mobile robotics developer, to manage and prioritise its various work orders.
In response, ASTI Mobile Robotics developed two lightweight EasyBot AGVs able to do just that. The solution’s main new feature is its multi-destination system, which can be configured to meet each client’s specific needs. The smart software calculates which route the AGV should take to reach its destination. The vehicle follows a different circuit and stops at different stations for each order and performs different actions at each point on the route. It not only provides autonomous materials handling; it also offers connectivity, integration, predictive maintenance and performance analysis.
To deliver this, the AGV is fitted with a mobile device via which it interacts with the system. Operators communicate with the AGVs and the rest of the system via an Android app — designed and developed by ASTI Mobile Robotics — installed on a tablet. They can change priorities, select destinations and obtain information on the vehicles. With this highly functional tool, TREIF operators can manage AGV orders on the move, without having to access a PC. The AGV’s route in the warehouse comprises 6 stations. Operators position the carts they want to send to the various stations and, via the app, select where the automated vehicles need to pick them up and which station they need to take them to.
Cart pick-up orders can also be generated by button at each station. To do so, operators briefly hold down a button, which lights up to indicate that the system has received the order to pick up a cart from that position. As soon as an AGV is free to perform the task, the system routes it to that station and the button starts flashing, indicating that the AGV is on its way. The vehicle departs from position P1 and passes under the carts waiting there ready for other uses. When the AGV reaches its destination, it hitches up the cart indicated by the user and takes it back to the queue at the home position.
The system is designed to handle simultaneous orders sent from both sources —tablet and button — with the same destination. It gives priority to the order from the tablet, picking up the cart from the starting position and taking it to its destination. Once that order is completed, the AGV immediately accepts the order given via the button, collecting the cart indicated and taking it to the home position. By using a single trip to carry out two separate orders, this smart system optimises AGV routes and journey times to maximise operating efficiency.