Case Study: From Manual to Industry 4.0 in One Year
7th May 2020
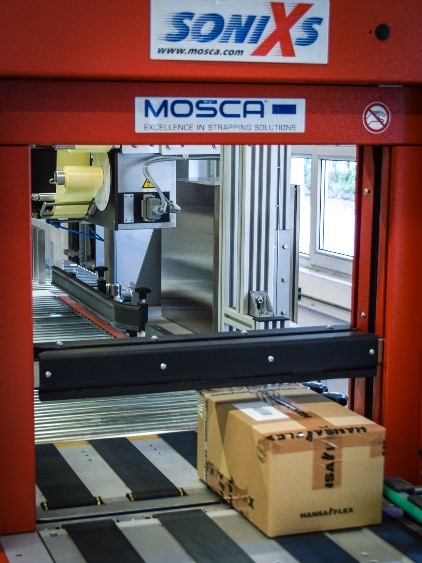
HANSA-FLEX, a leading hydraulic systems supplier based in Bremen, Germany, has prepared its packaging line for the future. In cooperation with the strapping specialists from Mosca, a networked, end-of-line, full-scale solution that is capable of much more than securing goods for transport was completed within a year. The project entailed intelligent strapping machinery with a fully automated parcel distribution system that combines state-of-the-art conveyor and strapping technology with automated data processing and Industry 4.0. This system practically eliminates errors over the last few metres of the packaging process, before the goods are reliably sent off to the customer.
It all started with a blank sheet of paper. The mission was to re-engineer a packaging line to make it 100% reliable, error-free and process-optimised. The products to be strapped included a variety of hydraulic systems ranging from hoses to seals and complex hydraulic components. Each day, around 1,000 parcels are processed and prepared for delivery at HANSA-FLEX headquarters in Bremen. Most of these packages come in different sizes and weights. They are delivered to end customers and to HANSA-FLEX branch operations by three different CEP service providers.
In the past, the last few metres of the HANSA-FLEX packaging process required a lot of manual labour. Employees picked up each package from one of the picking stations and carried it to the shipping department where – step-by-step – it was weighed, labelled and strapped for secure transport. Afterwards, the workers placed each finished package on a stack for collection by one of the three delivery service providers.
“All of these different steps made the end of our packaging line inefficient and prone to errors”, explained Frank Oetting, Central Warehouse Manager at HANSA-FLEX in Bremen. “It was time for us to find a new solution. One that was not only up-to-date, but also an investment in the future.” In search of a suitable partner, HANSA-FLEX contacted Mosca, a technology leader for strapping systems based in Waldbrunn, Germany. The hydraulics supplier was already using standardised strapping solutions supplied by Mosca. Now a customised application was needed to meet all of the customer’s specifications.
From initial design drawings to system launch in one year’s time
The Mosca team with their end-of-line expertise and the HANSA-FLEX team with their wishes and requirements sat down with the blank sheet of paper. Frank Oetting: “We knew exactly what we needed and worked with Mosca to develop the initial drawings.” A year later, he found himself standing in front of a fully automated strapping and package distribution system that reliably and precisely handles all of the end-of-line packaging operations that once required manual labour.
The heart of the new system is the EVOLUTION SoniXs TR-6 Pro, a high-end Industry 4.0 model manufactured by Mosca. This fully automated strapping machine with network interface was integrated into a conveyor system developed exclusively for HANSA-FLEX. Now the packages are simply placed on the conveyor with an order label – the system does the rest. An inclined roller conveyor aligns the packages and transports them to the EVOLUTION SoniXs TR-6 Pro. The machine automatically recognises the size of the boxes and secures them with double strapping. Mosca also supplies the white strapping material customised with the HANSA-FLEX logo. The strap ends are welded using Mosca SoniXs ultrasonic technology – which does not require a warm-up phase and saves energy.
End-of-line packaging runs like clockwork
Downstream processing is also carried out without human intervention. A scanner reads the order label, a calibrated scale weighs the package, and a printer creates the shipping label with all the information for the package delivery service. The system also attaches the label to the package. All data related to the shipment is forwarded to the HANSA-FLEX ERP system so that the order can be automatically invoiced by the respective CEP service provider. Three different conveyors assign the packages to the corresponding service providers. If a label is incorrect or illegible, the package is sorted out on a fourth conveyor and checked by an employee.
Mosca Area Sales Manager Wolfgang Dürkoop is responsible for HANSA-FLEX support: “Since the current workload does not require continuous operation of the system, we integrated an automatic start-stop system to help our customer lower energy costs.”
Close cooperation and open communication
The fact that this large-scale project was implemented so quickly is a direct result of the close cooperation between HANSA-FLEX and Mosca. Frank Oetting: “We have a lot in common in the way we work. We roll up our sleeves, tackle the problems and openly share information.” This hands-on approach made it possible to master the toughest project challenges without major difficulties. “A key factor was the interface to the SAP system that processes the shipping data and automatic invoicing”, Oetting explained. It was important to ensure that this functioned reliably and was designed in such a way that it could also be integrated into other applications with similar requirements. Wolfgang Dürkoop: “We worked with our system experts to develop a viable solution.”
Similar application for strapping pallets
It wasn’t long before HANSA-FLEX required a similar application for its Geisenfeld plant, where goods needed to be automatically strapped on pallets and assigned to the company’s shipping department or warehouse. “Once again we worked with HANSA-FLEX to create and implement a concept consisting of the strapping machine, conveyor system and data processing,” explained Michael Zimmermann, Head of Mosca System Sales for Germany, Austria and Switzerland. In this case, the conveyor system was built in an H-shaped layout so that goods can be placed on it from two sides. The system independently aligns the pallets, identifies the required strapping program based on the order label, and conveys the packages to a Mosca EVOLUTION SoniXs KZV-111-20 machine that vertically straps the packages to the pallets. Weighing, labelling and assignment to shipping service providers or warehouses are carried out on the fully automated conveyor system.
Concept, production and maintenance from a single source
The promising solution clearly meets the needs of the staff at the HANSA-FLEX sites in Geisenfeld and Bremen. “It was important for us to procure the entire system from a single source. And Mosca offered us exactly what we needed”, said Frank Oetting. Except for a few components, the system solutions at both plants were produced exclusively by Mosca. “We provide complete maintenance along with support for conversion and expansion work”, explained Wolfgang Dürkoop.
Thanks to its modular design, the system can be expanded at any time. “Flexibility is what makes this model ideal for our application,” says Frank Oetting. The company is already planning steps for the future, when conveyor technology will be used to connect the individual picking stations to the system. This will eliminate the need to manually place the packages on the system.
The system workload can be significantly increased in its current state. Wolfgang Dürkoop: “The EVOLUTION SoniXs TR-6 Pro can strap up to 900 packages per hour. With our solution, HANSA-FLEX is well-equipped to handle major production increases in the future.”