Interroll and Teknokom Install Automated Material Flow System in Turkey
28th May 2020
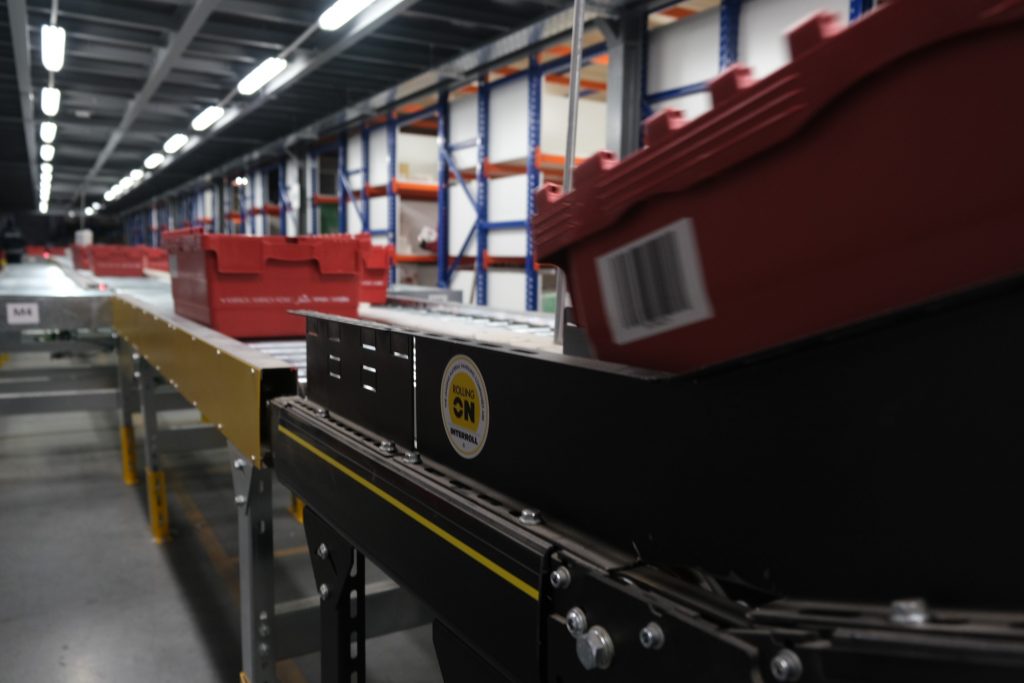
Interroll and Teknokom, an innovative system integrator for complete warehouse automation solutions, have installed an automated order picking system for Cookplus in Istanbul, Turkey. Essential elements of the new material handling solution are the RollerDrive EC 5000, MultiControl, and the Modular Conveyor Platform (MCP) from Interroll. The system combines advanced features such as travel control, automatic invoice printing, dynamic volume measurement, with cargo label applications and real-time monitoring.
The order picking automation system which was delivered and installed by Teknokom is a key part of Cookplus’s modern, 6,000-square-metre distribution centre of Cookplus in Hadimköy near Istanbul which serves customers all over the country. Cookplus is the e-commerce brand of Karaca Group, a leader in the tableware, kitchen and home textile market, operating with 2,700 dealers and shops in 27 countries. The zero-pressure-accumulation conveyors used for this material flow solution have a length of more than 220 metres interconnecting a variety of picking stations with the packaging and shipping areas on two floors of the facility. The efficient and extremely energy-saving conveying of totes and parcels uses about 190 RollerDrive EC 5000 units being controlled by 60 Interroll MultiControls cards connected to a programmable logic controller (PLC) and a warehouse management system.
“With our new solution we dramatically increased the performance and capacity of our distribution and fulfilment centre by avoiding a variety of complex manual internal processes. Just as important to us as increasing our efficiency was further improving customer satisfaction through very fast and reliable deliveries,” says Ertugrul Celebi, Chief Operating Officer, Logistics & Supply Chain, at Karaca A.S.
The advanced conveyor system is entirely managed by software developed by Teknokom, a long-standing member of the Rolling On Interroll program, Interroll’s international partner network. The software applications use the data gathered by Interroll’s MultiControl cards for controlling and monitoring purposes. One example is an intelligent travel control feature which allows bypassing picking stations or a complete floor if no action from operators is needed. Moreover, at the end of the picking operation, before packaging, a printer automatically equips every order with the respective invoice. Upon entering the shipping area, a label applicator automatically pastes to each order a barcode label for the forwarding agent; this label contains all of the necessary information, including the order destination, volume information and a list of content.
“To fulfill the demanding needs of our customer, we used our long-standing cooperation with Interroll and smoothly integrated different state-of-the-art technologies in this automated material flow system. The complete project was very carefully and holistically executed, from planning and installation up to maintenance and support. For example, our customer is now able to monitor the operation of his system in real time via an online application—whenever and wherever he wants,” declares Mustafa Hisim, Deputy General Manager at Teknokom A.S.
Teknokom’s software application allows for monitoring the whole material flow process for maintenance and support purposes via a user-friendly interface which offers controlling as well as reporting features. For example, the locations of the totes, the actual status of the orders, and the picked items in a single tote can be seen for both floors. Moreover, operation managers can receive live as well as time-frame-based reports about order fulfillment capacity, bottlenecks in the picking stations, error reports, and detailed performance information.