Transparency for the customer who is king
6th September 2021
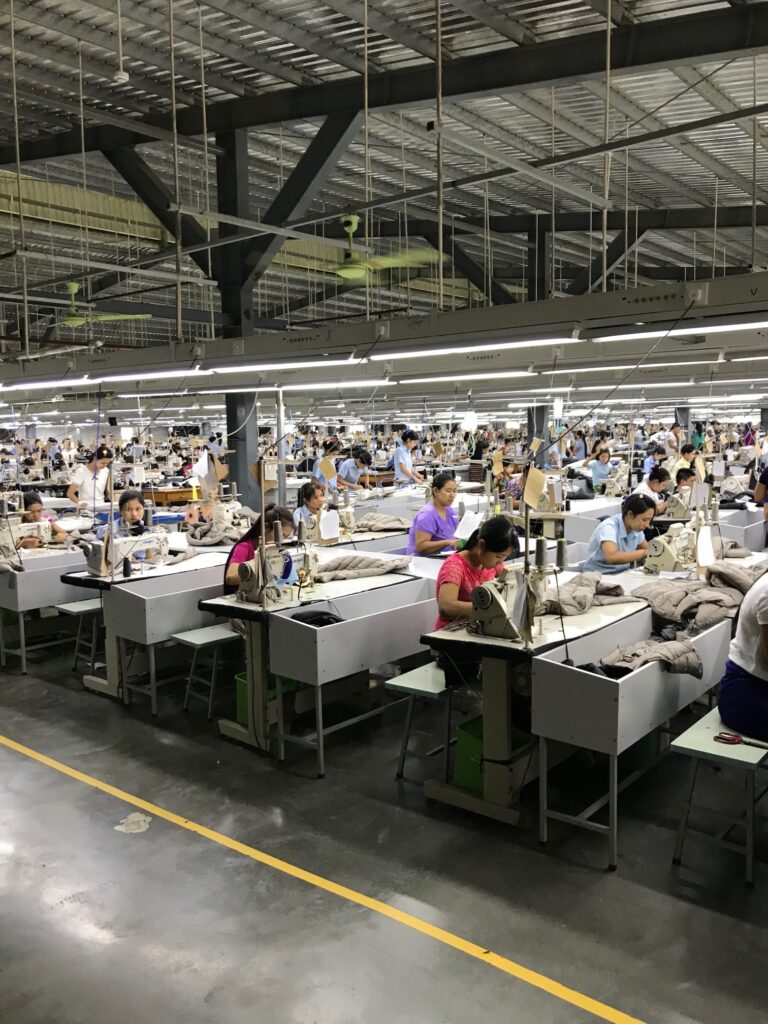
The new Supply Chain Act will take effect in Germany in 2023. The textile discounter KiK, already concerned with ensuring that suppliers comply with labour and environmental standards, took steps several years ago, which now puts it ahead in preparing for the new law. In 2015, the company said goodbye to Excel lists and e-mails in order to manage its supply chain with the CSR module of Setlog‘s OSCA software. So the most important homework for 2023 has been tackled.
11th June, 2021 will go down in German economic history books. On that day, the German government passed the Supply Chain Act after lengthy discussions. The goal is to ensure that environmental and human rights standards, especially in developing countries, are met and that millions of families have a better standard of work and life. The new regulations will initially apply to companies with more than 3,000 employees from 2023, and to companies with more than 1,000 employees from 2024.
What looks like a long lead time at first glance will seem to happen quickly – especially for companies that have not yet dealt with the issue. Anyone who manages a company that employs fewer than 1,000 people cannot easily cross the topic off the agenda. Supply Chain Management (SCM) and Corporate Social Responsibility (CSR) experts are preaching at the top of their voices that even mid-sized companies that supply large corporations should be concerned with the new supply chain law.
“Corporations will secure in new contracts that not only large, but all suppliers comply with the legal CSR regulations and that their supply chains are transparent,” emphasises Ralf Duester, co-founder of the software provider Setlog. The Bochum-based company has numerous customers – from medium-sized companies to corporate groups – who have been managing the issue of CSR with suppliers, purchasing agencies, auditing institutes and other supply chain partners via the Setlog software OSCA for years, thus bringing transparency to the supply chain.
KiK meets high standards
One of the long-time OSCA users is KiK Textilien und Non-Food GmbH in Boenen. Germany’s largest textile discounter has 70% textiles in its assortment. The rest are non-food items such as toys, accessories, gifts and stationery. The target group of the company, which is active throughout Europe, primarily includes families with children, young mothers and people on a budget who want to dress fashionably. Like most suppliers in this industry, KiK – the acronym stands for “Kunde ist König” (customer is king) – has almost all of its items produced by suppliers in Asia. The majority of the goods come from China and Bangladesh, the rest mainly from Pakistan, India and Turkey.
Anyone who works with KiK must meet high standards. Lower prices than the competition and good delivery reliability are not the only reasons for the company to relist a supplier. “Anyone who wants to cooperate with us is not only checked at the beginning, but has to undergo regular audits,” emphasises Ansgar Lohmann, who heads the CSR department at KiK.
The audit is extensive. Ten sub-areas along the core labour standards of the International Labor Organization ILO are audited in a matrix developed by the company. The auditors commissioned by KiK primarily examine working hours, minimum wages, social benefits and environmental protection requirements on site. However, they also check whether fire extinguishers, fire doors and smoke detectors are in place and look at the statics of the building.
The inspectors, who are liable to KiK for their findings, also keep an eye on official approvals such as fire protection, environmental or business licenses. The following applies to all suppliers: Those who show no willingness to develop further are not even listed. KiK carries out a total of 800 audits per year in its supplier pool.
Ansgar Lohmann’s 13-member team makes this effort because binding compliance with environmental and social standards has long been important to the company. In industry initiatives, for example, KiK also promotes company accident insurance in Bangladesh, building safety, fire protection and compliance with human rights.
Audit management made easy
Managing 800 audits is a challenge. KiK realised years ago that a flood of e-mails and Excel spreadsheets are unsuitable for managing such a Herculean task and bringing transparency to the supply chain. In 2014, the company decided to look for software support. “It was important for us to have a holistic approach with factory checks in an automated system that delivers data in real time,” Lohmann reports.
After analysing various providers, KiK chose OSCA, the software from Setlog. Back in 2013, the SCM expert integrated the Vendor & Compliance Management tool VCM, now known by the abbreviation CSR, into the cloud-based SCM software. The solution can be used as a stand-alone or in combination with OSCA’s SCM module. It covers the entire supplier relationship from onboarding through quality management, audits including rework, document management, reporting and ratings.
“We were convinced not only by the good price-performance ratio, but also by the fact that the software is compatible with other systems and is so easy to understand that even less experienced suppliers can use it,” explains Lohmann.
After the decision was made, everything happened quickly. In May 2015, the discounter gave the green light for the IT project. Less than three months later, it went live with OSCA. Then the company integrated the purchasing agencies, the testing institutes, and the training and qualification partners. Just one year later, all suppliers had been trained. Since then, all players have been communicating in real time via the software. E-mails and Excel lists have been history for the CSR department ever since.
Predefined pattern
The daily routine follows a predefined pattern: If an audit is to be carried out, the CSR team commissions an auditing institute via OSCA, which confirms the agreed date and the order. The audit report, including photo documentation, is uploaded to OSCA. The audit criteria are weighted differently to produce an overall score. If improvements are necessary, they are discussed with the responsible persons on site.
Deficiencies must be rectified within a specified period. An early warning system displays all audits on a dashboard of the CSR team and automatically informs employees about the progress of rectifications according to a traffic light system.
Whenever a KiK employee wants to find out about a supplier, all they have to do is press a button to see how good the factory is. Other analyses can also be visualised on the dashboard – such as the performance of all procurement agencies or the CSR performance of an entire procurement country. The monthly evaluations are not only well received by management, they also serve as a basis for strategic decisions, the company’s regular sustainability reports, and can potentially be incorporated into the risk assessment of binding due diligence requirements.
Since 2015, KiK has been working to continuously improve the area of CSR. Currently, the company is doing its utmost to integrate the so-called Tier 2 suppliers into OSCA. This involves the weaving and dyeing production stages.
But Lohmann knows that KiK alone can only do so much. For him, it would be important for the industry giants to pull together – so that standards for complaint management are introduced, for example. “Today, it is the case that some factories have 20 hotline numbers for complaints to their major customers,” Lohmann reports. KiK is therefore involved in the Alliance for Sustainable Textiles and hopes that standards will prevail.
Now that OSCA has been in use at KiK for more than six years, the flow of information has sped up considerably. “Things are up to three weeks faster today than before the software was introduced,” Lohmann sums up. Thanks to the software, resources could be used elsewhere. “But the most important thing is the time saved. If a defect has been reported in a factory, we can react immediately,” reports Lohmann.
Another advantage of OSCA is its easy connection to other systems. At KiK, the results of the audits are imported directly into the SAP system via an interface from OSCA – in which things such as a supplier evaluation is possible at the push of a button. “A buyer can, for example, call up the performance of a supplier in real time over the entire year,” explains Lohmann.
If Lohmann had to choose software now, he would choose OSCA again. “It meets our requirements,” he says. Among the five most important secrets of success in this context, he counts:
- Understandability of the software: it is easy to learn and is available in multiple languages
- Fast IT implementation: The software goes live within one quarter
- Easy IT compatibility with other systems: Interfaces can be easily set up to other IT systems
- Clear management cockpit: Users can see at a glance how a supplier is performing at the touch of a button
- Reliable audit templates: The software automatically creates resubmissions and displays a to-do list for employees
With CSR, KiK is on everyone’s lips. Politicians, journalists or members of non-governmental organisations regularly contact KiK to find out more about the topic. Competitors openly ask KiK how the company has tackled the issue. Presumably, Lohmann’s phone will ring even more often by 1st January, 2023.