Rapid Order Processing at Very’s Automated DC
22nd November 2021
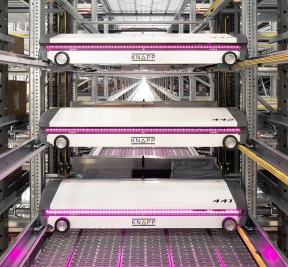
Advanced automation technology from Knapp is helping The Very Group to fulfil customer orders in just 30 minutes at Skygate, its new distribution centre in the East Midlands (UK).
Launched on the day that the UK’s first lockdown was announced in March 2020, the 850,000 sq ft facility has secured a number of benefits for the online retailer and its customers, including greater product availability, faster refunds and enhanced ability to handle peak trading periods.
“A fast, seamless fulfilment operation is vital for great customer experience, and that’s what we focused on when developing Skygate’s highly automated technology,” commented Phil Hackney, Chief Operating Officer at The Very Group. “Throughout the pandemic, that technology has helped us to manage huge volumes of orders. It also enabled us to bring all of our clothing and footwear returns under one roof for the first time and means we’re well positioned for future growth.”
Despite a surge in orders during its first year as the pandemic fuelled demand for e-commerce, Skygate managed to deliver the performance required by Very. The automated picking, sortation and packaging technology from KNAPP means that orders can be ready for dispatch within 30 minutes, compared to around four hours at Very’s previous fulfilment centres. The fastest order to date, processed in July 2021, was ready for dispatch in just 17 minutes.
Operating 24/7, Skygate has processed over 40 million items since its launch and has significant potential for future expansion. The efficiency of processes at the facility, combined with the consolidation of three sites into one fulfilment and returns centre, will contribute up to £25m in efficiency savings per year for The Very Group. Skygate’s central location – close to the M1 motorway and adjacent to East Midlands Airport – combined with the on-site rail freight terminal will save Very an estimated one million road miles a year.
Designed for peaks
With Skygate responsible for the fulfilment of 95% of the Group’s customer orders, KNAPP worked closely with Very to ensure that the automation would be able to handle peak volumes with the required speed and accuracy. The logistics technology enables the pre-picking of orders on high-traffic days, which helped Very to cope with record-breaking Christmas and Black Friday trading in 2020. Sales for Very.co.uk increased by over 25% year-on-year in the seven weeks to Christmas 2020, with Skygate processing an impressive 3.9 million orders during this period, peaking at 265 orders per minute.
Key to both rapid order fulfilment and efficient returns processing at Skygate is KNAPP’s EcoPocket system. This pocket sorter technology uses a matrix sortation algorithm to arrange products in RFID-enabled pockets into the correct sequence to fulfil customer orders at the packing stations.
Items are placed in the pockets at a series of workstations, where totes of product arrive automatically from KNAPP’s OSR Shuttle Evo storage system. Taking an item from a tote, the operator scans it and drops it into a pocket with a single swipe action.
One of the largest shuttle systems in Europe, the automatic store features over 400 shuttles and provides almost 640,000 storage locations. Combined with 120,000 pockets in the EcoPocket system and 26,000 pallet locations in the manual store, Skygate houses an
One-touch returns handling
The automated handling solution at Skygate also enables one-touch processing of returns, with products available for resale within 30 minutes and customer refunds provided faster than ever before. Returns are prioritized, with two-thirds leaving the site within 24 hours and the overwhelming majority within three days.
A vast dynamic buffer of EcoPockets on the third mezzanine level of the warehouse makes returns processing a breeze and gives Skygate the capacity to handle 80,000 returned items per day.
Also featuring a dispatch sorter with 96 destination chutes, the automated logistics solution is controlled by KNAPP’s KiSoft suite of software, comprising Warehouse Management System (WMS), Warehouse Control System (WCS) and machine control systems for seamless integration.
“We are extremely proud to have developed this brand-new distribution centre from concept to reality in just three years,” commented Anton Tschurwald, Vice President Retail Solutions for KNAPP AG. “A strong spirit of partnership with the customer meant that Skygate was delivered within budget and on time, despite going live during the COVID-19 lockdown.”
To keep the complex project on schedule despite the lockdown restrictions, KNAPP worked with Very to develop – within just a week – the infrastructure and processes to continue start-up of the system by the British team with support from technicians working remotely from Austria. “The significant challenges were overcome through a potent combination of teamwork and technology,” said Tschurwald.
To ensure maximum system uptime, a 33-strong team of KNAPP Customer Service technicians is based permanently at Skygate, carrying out comprehensive preventive maintenance and dealing quickly with any issues that arise.