Save the planet by looking into space
17th January 2022
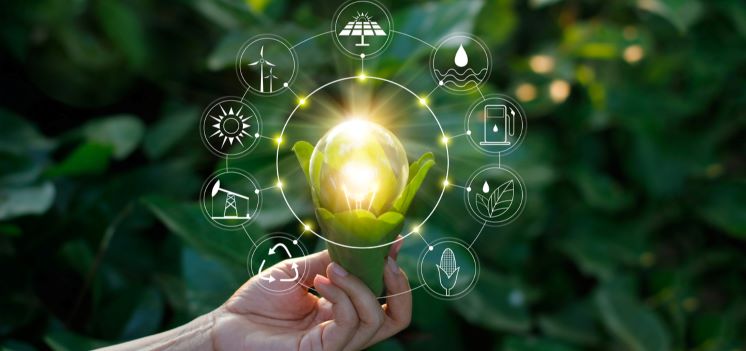
The recent COP26 summit has, despite some disappointments, highlighted the need for radical change in every area of the modern economy, supply chains not least, writes Matt Whittaker, Commercial Director at Bis Henderson Space. This need is widely accepted and being acted on in transport – electric or perhaps hydrogen powered vehicles, modal shift to rail, even low carbon deep sea shipping – but the carbon impact, and potential for improvement, of essentially static and inert warehousing and storage is less considered.
That poses a problem, especially in the UK. It’s well recognised that the country is ‘under-warehoused’, especially given the rapid and permanent rise in eCommerce with its demands for increasingly sophisticated distribution facilities. But continuing to build ever more ‘big sheds’ is in no way sustainable, let alone carbon-neutral, on several levels.
Firstly, the UK’s construction and building industries rate really poorly in international terms for their use of concrete, steel and other energy-intensive materials – and ‘net zero carbon’ steel or cement are still largely aspirations, rather than achievable realities. New build is intrinsically bad for any carbon footprint.
There are less obvious climate change considerations. Firstly, while the local effects of climate change on agriculture are as yet unknown, they are unlikely to be positive – should we really be concreting over more farmland, in a country that hasn’t been able to feed itself for two hundred years or more? And secondly, is it wise to build ever more distribution centres, vital nodes in the economy of the nation, on increasingly vulnerable, if attractively flat, flood plains?
The need for more warehousing and storage capacity is undeniable – ironically, increased capacity may be essential to achieving other carbon and wider environmental goals, for example by enabling more energy-efficient transport and distribution networks. But need this all be new build?
We know that there is a considerable estate of unused, or under-utilised, warehousing that is potentially available, at least on a short-term or temporary basis. We also know that there are many businesses desperate to take advantage of those opportunities. How can we bring these parties together, to improve the carbon performance of supply chains without adding to the burden of new build?
Many companies are sitting on vacant or under-utilised storage space, for many reasons. They may have off-shored some of their manufacturing meaning they have a lower requirement for goods-inward storage. They may have outsourced some of their distribution to a 3PL’s network. They may have ‘legacy’ facilities from mergers or acquisitions, or they may have moved to a strategy of national or regional DCs, leaving local stock-holding points behind. Their requirements may have shrunk – leaner supply chains, or sometimes the actual product is now radically smaller. Their business model, perhaps a shift to B2C eCommerce rather than bulk sales to wholesalers or retailers, may have made space redundant.
This ‘sort of vacant’ space is in no way carbon neutral. It isn’t too easy to heat, or refrigerate, or otherwise service as just part of a warehouse.
On the other hand, there are many firms that desperately need more warehousing storage or operational space. There are temporary, one-off, requirements – perhaps a relocation while the existing warehouse is refitted. There may be unplanned events such as, a fire in the warehouse or perhaps a major product recall.
Then there are planned peak requirements. Many businesses have to build stock in anticipation of seasonal or predictable events, for example: New season fashion, Christmas, Easter, sporting tournaments, big rock tours and so on. These events may be one-off or annual and some companies scale their warehousing to accommodate those peaks. However, this inevitably means they are paying top dollar for space that, a lot of the time, isn’t really being used but for which they are still paying. This approach is wasteful, both from a financial as well as an environmental perspective.
And then there are needs that arise directly from the climate agenda. In many (not all) business model, the overall carbon footprint can be mitigated by holding more stock close to market – that implies many more storage/warehouse areas, but on a scale that doesn’t equate to a whole shed.
Many businesses may be trialling new ranges or new markets and need the facilities to support a ‘toe in the water’. And many companies are experimenting with different strategies, and balances between strategies, where they are not necessarily in a good position to commit to a long-term lease on a new build shed, even if that were desirable.
Fortunately, Bis Henderson Space exists largely to marry up these potential partners – the companies that are sitting on unrealised space assets, and the businesses that need, temporary, short-term, seasonal or experimental storage or fulfilment facilities.
Often, our ‘suppliers’ of excess space can offer a fully-serviced site where clients can tap into the existing trained staff, IT systems and so on, and we always try to spot the synergies. For our space providers, the deals we broker, which might range from a single six-month contract to a regular seasonal arrangement, can provide an unexpected source of income and volume-related operational efficiencies. For our space-hungry clients, we can source operational space that can help grow the business without climate change guilt.
It’s not realistic to suppose that our economy can be sustained without some degree of new build warehousing, but it surely makes sound environmental thinking to make the best possible use of the assets we have before we commit to ever more carbon-intensive projects.
At Bis Henderson Space we offer unique, low risk, high flexibility solutions that can continually adapt to changing business needs, including a transition to a more eco and sustainable solution.
Matt Whittaker is an experienced 3PL commercial director and logistics real estate specialist, and currently straddles two roles for Bis Henderson Group; heading up it’s the Property Services function for Bis Henderson Consulting whilst also fulfilling the role of Commercial Director for Bis Henderson Space – harnessing his intimate knowledge of the Industrial and Logistics Real Estate market to service the practical, operational and commercial strategic requirements of its customers.
Adept at translating customer needs and business trends into innovative property solutions to deliver real value, he has the creativity, market intel and experience to lower cost, maximise value and enable growth and change plans.