OSCA brings visibility to jeans supply chain
2nd March 2022
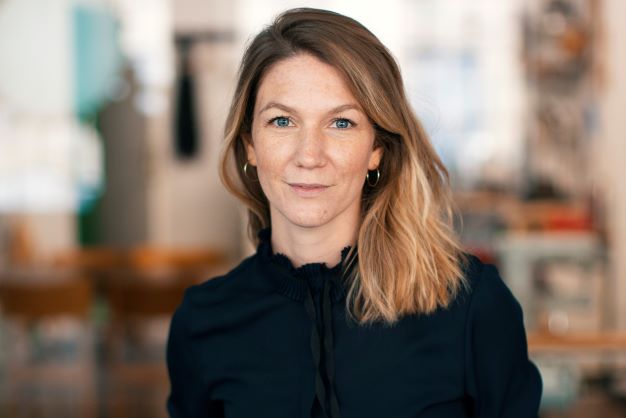
When it comes to jeans, the name MUSTANG immediately comes to mind in the fashion industry. To bring transparency and structure into the supply chain, the company has been relying on the SCM software OSCA since 2021. In doing this, the Schwaebisch Hall-based company was able to achieve end-to-end visibility in the supply chain.
When the name “MUSTANG” is mentioned in the fashion industry, insiders like to tell this story: MUSTANG was founded in 1932 in Kuenzelsau by Luise Hermann as “L. Hermann Kleiderfabrik” as a reaction to the stagnating timber trade business of her husband Heinrich Hermann. The company initially manufactured workwear. When a certain Albert Sefranek married the founders’ daughter, Erika Hermann, in 1945, it was him who had the idea to manufacture jeans instead.
The story is legendary: In a bar frequented by many American soldiers in 1948 in Frankfurt’s Bahnhofsviertel, Sefranek traded six bottles of Hohenlohe schnapps for six of the modern pants from the US. Albert´s mother-in-law, the original founder, initially refused to sew the “tight American pants”. But the very first order swayed her fast: “300 jeans, please!” The mother-in-law agreed, and the business took off.
The only constant in life is change – this motto also reflects the company’s further history. In 1989, for example, the company obtained the license for JOOP! jeans, ending in 2003 with the sale of the JOOP! brand. At the end of the 90s, the jeans market was in crisis as overall demand was declining. MUSTANG closed the production facility in Kuenzelsau, where 15% of the total volume was still manufactured at that time. The restructuring measures continued until the early 2000s.
Today, the company produces abroad. Suppliers in Tunisia and Turkey manufacture about half of the volume, the rest comes from the Far East – Pakistan, India and China. Between 25 and 30 suppliers work for the company, which has been based in Schwaebisch Hall since 2020. Around 95% of the goods are transported by large container ships; only in exceptional cases do jeans start their journey to Europe by plane. MUSTANG works with five different logistics carriers. The pants specialist consolidates all imported goods in a warehouse of fashion logistics company Meyer & Meyer in Wittenberge (Brandenburg). Around six million MUSTANG units pass through the facility every year.
All sales channels are fulfilled from Wittenberge. The retail sector with 90 stores, 45 outlets and online sales accounts for about 50% of the total volume. The production setup with up to 30 suppliers and an agency in Hong Kong works – but has become increasingly complex in times of volatile supply chains. Whether short notice volume changes or unplanned delays: Until August 2021, such data had to be entered manually into the ERP system for the total of 2,500 shipments per year. There were tracking lists in Excel for purchase orders and forwarders received change notifications by e-mail.
“It was a huge manual effort and we suffered from information silos. The system was also error-prone,” reports Signe Oepen (pictured). She has been COO of the company since 2020 and leads the operations team with 35 employees. In the 21st century, ordering processes are becoming faster and production more complex. Therefore, at the end of 2020, MUSTANG started looking for modern software to get more visibility into the supply chain and speed up processes.
Within a short period of time and after a selection process, MUSTANG chose Setlog’s cloud-based software OSCA. “With OSCA, we get more transparency into our supply chain and can track purchase orders digitally. This is an important pillar for our growth strategy,” announced MUSTANG CEO Andreas Baur in January 2021. According to COO Oepen, the crucial factor for the decision to use OSCA was its simple implementation process, which enables rapid and comprehensive handling of all supply chain processes.
Simple implementation? What might apply to normal times turns out to be quite the challenge in times of a global pandemic. After all, working short-time does not necessarily support shorter processes. “But thanks to frequent catch-ups and feedback loops between MUSTANG and Setlog, which entailed a meeting every two weeks, Setlog implemented the software very professionally,” reports Oepen. Today, dozens of employees access OSCA.
The fashion company uses OSCA SCM for scheduling, production reports, transportation, warehousing and reporting. What that means is that MUSTANG reports its purchase orders from the ERP system via OSCA to the suppliers or the agency in Hong Kong. The SCM software serves as centralised communication tool – from order confirmation and delivery planning to the booking of shipments.
In addition to costs, the employees can also monitor volumes, lead times, transport times and delivery dates. Suppliers and agencies enter transport notifications and tracking data into the system. Dashboards allow users to view the respective status of orders and shipments. “We have become much faster with OSCA and can easily enter all changes into the software,” says Oepen.
If delivery dates change, all partners in the supply chain are informed simultaneously and in real time. “Now it’s not a problem if an employee is on vacation. In the past, we sometimes had to sift through a lot of emails to find relevant information,” says the operations lead. She also points out one special feature: Information on packing lists is transmitted to the logistics centre in Wittenberge via an interface once shipments are finalised. This allows the logistics specialists to plan labour even before the goods arrive.
In addition to the topic of digitisation, MUSTANG is also committed to sustainability. When it comes to environmental protection, OSCA also helps significantly in further bringing transparency into the value chain. MUSTANG can enter so-called sustainability features for purchase orders into the software. For example: “Sustainable cotton” is marked in a field when an order is placed. The agency or suppliers can then see that this specification has been linked to the order.
Even through the waves of the pandemic, it was still smooth sailing for MUSTANG – thanks to the operations team and OSCA. Because container ships did not leave ports or were delayed due to lockdowns in production countries, goods were in danger of arriving too late. MUSTANG changed transport modes a few times – from sea to air – to gain more speed. Before the pandemic, MUSTANG airfreighted only 5% of their parts, during the Covid-19 pandemic they involuntarily shipped 20 percent by air. “These very last-minute re-bookings are more controllable thanks to OSCA,” Oepen says.
Whether it’s disruptions in global transportation, pandemics, environmental disasters, or political crises: “Without a modern IT landscape, including not only SCM solutions but also ERP systems, production planning, customs brokerage solutions, data warehouses and payment systems, consumer goods manufacturers are ill-prepared for the challenges of the future,” says Ralf Duester, member of Setlog’s board of directors. According to him, the most important trends include the
increasing complexity in procurement and distribution, the shift from push to pull markets, an acceleration of ordering process, and the growing need for additional services and all-in-one solutions. “MUSTANG has impressively shown how – thanks to a dedicated IT team, a strong IT infrastructure and collaborative supply chain partners – a fashion company made it through a difficult period and has positioned itself well for the future,” Duester said.