New Smart Pallet Mover promises performance boost
3rd March 2022
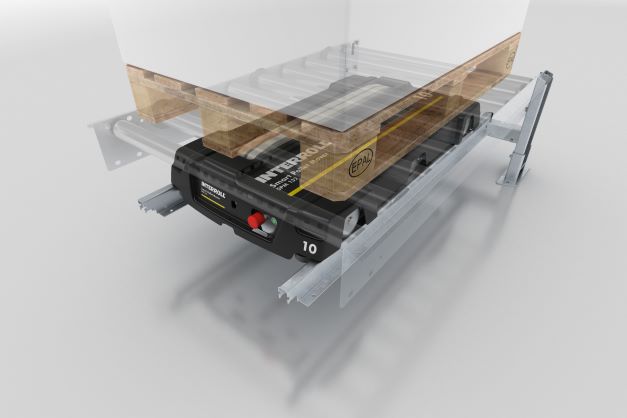
It is not the performance of modern production machines but their material supply that promises the greatest potential for further productivity increases in industrial companies today. With the new Smart Pallet Mover (SPM), Interroll has launched an awarded solution that can be adapted as a flexible and modular pallet management system to meet a wide range of application requirements in industrial manufacturing.
The customer and user benefits of the Smart Pallet Mover are impressive: Those who use it can now finally automate work processes in front of the machine production to avoid manual activities in safety-critical areas and manage the pallet work flow by buffering, sorting, sequencing and carrying at the right time to deliver significant improvement of the machine down time optimising the return on investment (ROI) of the machine production cells.
This not only eliminates costly production interruptions for material supply to machines, but also the risk of accidents during operation. In this way, productivity increases of up to 30% are possible compared to manual operation.
The Smart Pallet Mover is a pallet management solution for automating pallet transport in the vicinity of manufacturing machines and for production-related picking and sequencing processes, which can also be used in Industry 4.0 environments. The SPM is designed to transport, sort and buffer boxes or pallets weighing up to 1,000kg.
It represents a mobile and autonomously acting material flow system that can be used, for example, as a cost-efficient supplement or substitute for forklifts or automated guided vehicles (AGVs).
The Smart Pallet Mover solution consists of various modules. The centre of the solution is a mobile unit (SM1000 Mover) that runs underneath non-driven conveyor sections and moves pallets lying on them. A transfer car (SM2000 Transfer Car) which moves on a rail can transport pallets between parallel conveyor sections.
“With this platform solution, which is unparalleled on the world market, we are tapping into the great productivity potential offered by production-related pallet management automation for our customers and users,” explains Jens Strüwing, Executive Vice President Products & Technology at Interroll. “A user-friendly 3D online tool, the SPM Layout Configurator & Pallet Flow Simulator, makes it possible to configure a system quickly and easily as well as simulate planned operation on the computer.”
The flexibility of this innovative solution, the use of proven technologies and a very short payback period ensure that users can significantly strengthen their competitiveness. As with all Interroll products, the Smart Pallet Mover is extremely easy to install, operate and maintain. The modular plug-and-play solution can therefore be put into operation without lengthy interruptions to production, even during modernisation projects.
Networking capabilities based on global data standards such as REST API and JSON ensure maximum compatibility and ease of use. The conveyor modules can be reconfigured very easily if required, and height-adjustable supports allow the system to be installed even on uneven floors.
Before the official market launch, the new solution had already won two internationally renowned awards. For example, the Smart Pallet Mover won the Red Dot Award, Product Design 2021, for its exceptional design quality and degree of innovation. At the same time, the solution was chosen by the independent experts of the International Intralogistics and Forklift Truck of the Year Award (IFOY AWARD) in March 2021 as a finalist of this globally renowned intralogistics award.
With this new offering, Interroll is taking into account the fact that production managers are increasingly focusing on material handling, as shown, for example, by the survey “Production Logistics in Medium-Sized Businesses,” which Interroll published last year: The average degree of automation of internal material transport at the companies surveyed was only 53%. Almost every tenth company (9%) had a degree of automation of less than 25%.
CLICK HERE to view a video of the new solution.