‘World-class’ automated facility for pet food maker
19th August 2022
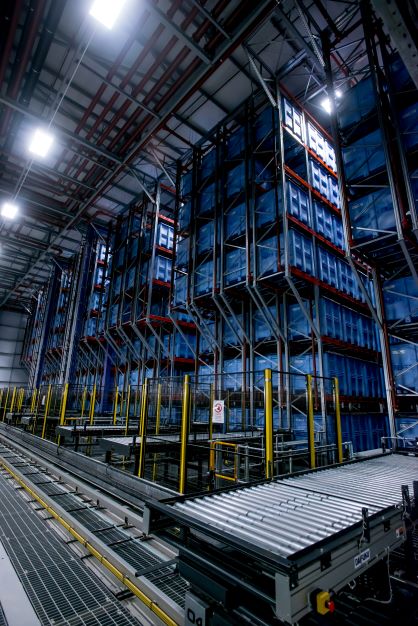
Japanese factory automation specialist Daifuku has been instrumental in creating Europe’s most advanced production plant dedicated to the manufacture of high-quality ‘own label’ pet food.
Serving more than 2,500 customers globally, Lancashire-based GA Pet Food Partners produces over 80,000 tonnes of complete dog and cat food to strict human-grade standards. Its innovative use of intelligent automation underpins the business’ operational efficiencies, while enabling it to manufactures 930 different products for its global customer base of pet food brands.
Being able to manage such complexity, while maintaining the highest food standards, is largely down to the company’s adoption of best-in-class technology, which includes four fully automated fork lift trucks (called ‘Henrys’), high bay storage and retrieval systems, sorting transfer vehicles (STVs), conveyors and three huge automated guided vehicles (camels) called Snap, Crackle and Pop.
Daifuku has been specifically responsible for the design and installation of the storage and retrieval systems in the Pantry and Larder Store within the Ingredients Kitchen area of the GA Pet Foods’ facility. This solution comprises 12 automated cranes (six in each chamber), with associated racking, which creates 21,000 unique storage locations. These are used to store raw ingredients and finished products in the Pantry / Larder Store respectively, prior to transportation (via the automated camels) to the extrusion facility, where the finished, dry pet food is formed. All of the warehouse systems are controlled by Daifuku’s WCS partner Invar.
Collaboration is key
Five years in the planning and four years in development, the GA Pet Food Partners’ operation at Chorley, Lancashire represents the very best in automation and genuine partnership. Chairman of GA Pet Food Partners, Roger Bracewell, was determined to find the best automation providers to work on the project, as long as they were able to work together as a single team. He said: “From the outset of our automation journey, we made it clear to potential technology partners that we wanted to create a collaborative team, where genuine dialogue could take place among all of our automation partners.
“Right from the start, we made this intention clear, paying each technology provider for their time during the pre-engineering phase – so that they could provide us with the best, most detailed designs and proposals. We didn’t just ask firms for their ‘best price’. We wanted this to be a quality-driven process and not one that focused solely on the lowest cost.
“Having now opened our fully-automated Ingredients Kitchen, the results speak for themselves. This operation, we believe, sets new global standards for not just pet food production, but also human food processing – especially in the areas of traceability and operational efficiency.”
Extruder efficiency
Interestingly, GA Pet Food Partners’ automation investment strategy has been underpinned by the business’ adoption of sales and operational planning (S&OP) principles.
Russell Hutchinson, business development manager at Daifuku, explains: “While so many businesses nowadays adopt a lean manufacturing strategy, the team at GA have taken time to really understand their operation and realised that ‘lean’ is not the right approach for them. For the plant here in Lancashire, it’s all about keeping the main extruder working to maximum capacity.
“As they say here, ‘If it ain’t turning, it ain’t earning’. That was a real lightbulb moment for Roger and his team who have subsequently invested in the upstream element of their supply chain, with the ultimate objective of improving the extruder’s efficiency.”
For GA Pet Food Partners, automation has not been about labour saving or cost cutting. Moreover, technology has enabled the business to increase output by 30%, improve overall plant efficiency (achieving an improvement of 15% in extrusion up time) and maintain world-class quality standards. The use of leading-edge automation has also enabled the company to remain flexible – one of its key areas of competitive advantage within the global pet food production sector. This as all be done without any increase in headcount at the facility.
Having opened the fully automated production facility this summer, the next project on GA’s agenda is its finished packaging line, which will further improve its service levels to global customers.
similar news