Delivering WMS Advantages
21st November 2023
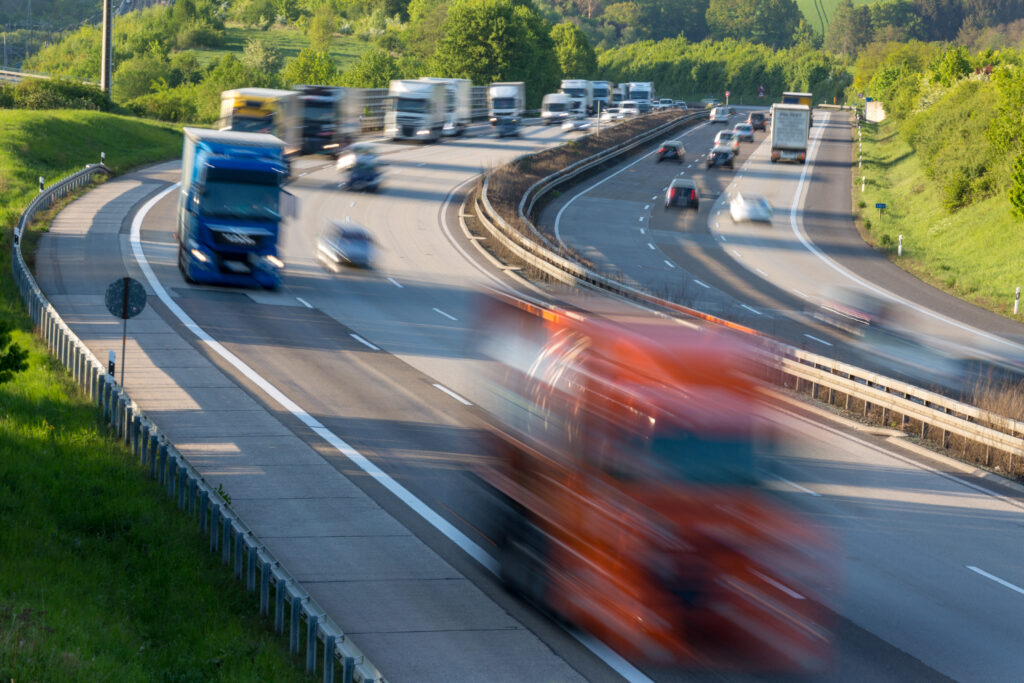
Sainsbury’s wanted to select and install a new WMS, then self-manage it. Learn how the retail giant achieved that goal.
Changing core processes, technology or operations can be disruptive to supply chains but is often a necessary evil. J Sainsbury’s plc, the UK’s number two food supermarket chain with a 15% market share, owns the formerly catalogue-based general merchandise brand Argos, as well as Habitat homewares and the Tu clothing range. With 1400 stores and over 150,000 staff it has grown exponentially from its Victorian foundations.
Simon Frodsham, Sainsbury’s Head of Engineering, and Chris Gaunt, Head of Product, gave an enlightening use-case presentation of the project at Körber’s recent Elevate conference in Prague. Together they explained the rationale for change. Previously the group had several WMS products in use and ageing warehouses. The company wanted to have in-house capability for the new WMS, to have something that was easy to upgrade and that could handle any product anywhere in the supply chain, food or non-food. It had to be brand-agnostic, flexible and help improve the availability of in-store stock.
Selection Process
A broad selection of WMS vendors were invited to tender. Sainsbury’s demanded a new WMS to be functional, to align with other technology in use (e.g. ERP), be able to handle the vast volume of products, provide the best service and support, cloud-based and integrate with the existing supply chain ‘ecosystem’. The business relationship was key, Gaunt and Frodsham explained, as well as the total cost of ownership. Ultimately the company chose Körber’s ‘Warehouse Advantage’ (WA) product for Argos’ Local Fulfilment Centres and depots (LFC) in March 2021.
Sainsbury’s supply chain sees 13,000 deliveries made per week across 200 countrywide postcode locations. In addition, consumer shoppers are able to collect parcels or drop-off returns at supermarkets and Sainsbury’s Local stores. Having bought WA from Körber the retail giant decided to run it themselves. But this required hiring new employees and training large teams, which took time. The decision was taken to partner with a niche integrator, iWMS, for the first implementation.
The project was delivered on time, with new pick, label and sorting features. Processes that were improved included order status, integration to tracking, stock management and the real-time allocation of order fulfilment. Having used Körber’s (formerly Voiteq) voice-directed systems for 20 years it made sense to continue using the ‘One Voice’ platform as a core technology in all the LFCs. “It’s a really successful collaboration,” said Gaunt. “Warehouse Advantage is flexible. It was a complex integration and is an evolving operation. We are iterating ways of working with it.”
The Sainsbury’s team are now predominantly independently running the WMS, with some outside support. Next year will see new and existing LFC sites adopt WA as it rolls out across the logistical network, including at a national depot which is able to deliver nationwide within 5 hours. This national depot handles general merchandise (non-food) for any of the group’s retail outlets. “We wouldn’t have decided to do that if we weren’t satisfied,” Frodsham stated.