Lampenwelt Brings Light into the Supply Chain
2nd August 2024
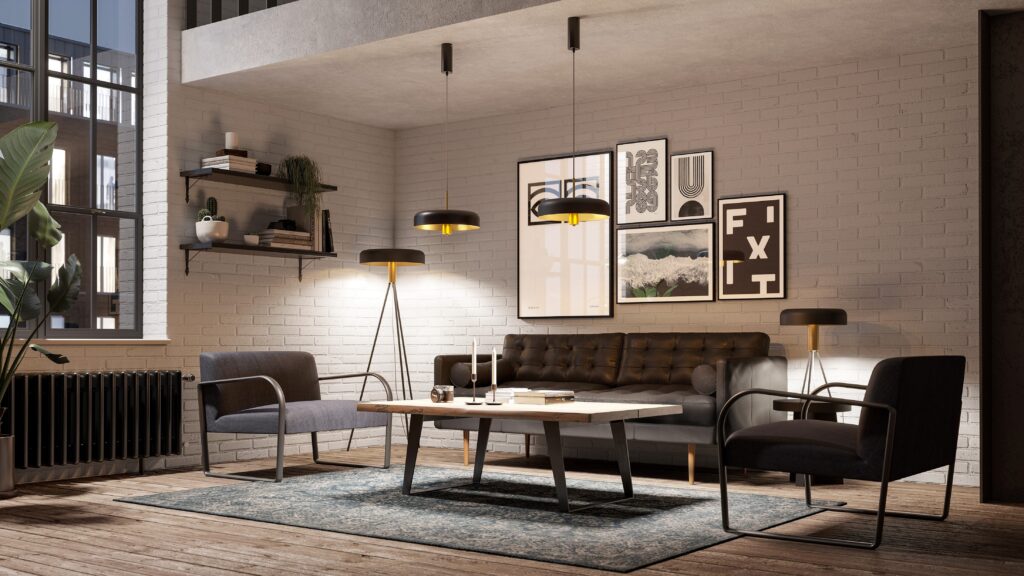
When it comes to ordering lights online, many consumers make the final click at Lampenwelt. The e-commerce specialist, which is part of the LUQOM Group, recently started using the SCM software OSCA to bring transparency to the supply chain. As a result lead times and the workload for orders have been significantly.
“In addition to simple user guidance, Setlog convinces with its fast implementation,” says Patrick Keyser, Director Demand & Order Management, Global Forwarding, Lampenwelt GmbH. Anyone moving into a new home has a lot to do. Packing, moving, unpacking, assembling furniture and then lots of paperwork. Often there are only temporary light bulbs hanging from the ceiling in the new apartment. Replacing these is also on the to-do list. In the past, people would rush to large furniture stores and often spend half a Saturday in the lamp department to find a new lamp and the right light bulb for each room. But in the age of the Internet, many consumers do away with such time-consuming activities: Instead, they shop for their desired lamps online from the comfort of their new sofa.
For more than two decades, Lampenwelt from the Sauerland region of Germany has been one of the largest and most successful platforms for the sale of lamps of all price ranges. The company sells its products in 27 countries via various domains, including lights.co.uk in the UK and luminaire.fr in France. The online pure player, which is part of the Berlin-based LUQOM Group founded in 2017, offers a range of around 450 brands and more than 60,000 products. Lampenwelt is the nucleus of LUQOM. The LUQOM Group was extended by the strategic acquisition of Lampemesteren from Denmark in 2021 and the acquisition of the QLF Group in 2019, the online market leader in Benelux.
The associated sales growth also brought challenges – in all three of LUQOM’s business divisions: Services, brands including own brands and the e-commerce business. “Without a cutting-edge IT landscape, companies in the consumer goods sector can no longer be successful today,” emphasizes Patrick Keyser, Director Demand & Order Management, Global Forwarding at Lampenwelt. The retail expert has years of experience in digitalization in the fashion sector. Since 2022, he has been transferring his knowledge to the lighting and smart home products sector with the help of his team. His goal: to bring light into the darkness of the supply chain.
Darkness is an exaggeration, of course. Until now, the ordering process had been handled via email to the group’s branch in Asia, LUQOM Asia. The employees took care of purchasing from the Asian suppliers. “On one hand, the effort involved via Excel and email is huge. On the other hand, changes in production or delivery times pose challenges because the supply chain is not transparent,” reports Keyser.
He therefore tackled the project ‘introduction of SCM software’ quickly. From his previous position, he had fond memories of the cloud-based tool OSCA from the Bochum-based software company Setlog: “In addition to simple user guidance, the provider convinces with its quick implementation,” emphasizes Keyser. After consultations with Setlog Managing Director Ralf Duester and an analysis of other providers, the contract was signed in August 2022 and the project launched immediately. The first project milestone by December was to connect and train LUQOM Asia (30 employees) and all Chinese manufacturers of Lampenwelt’s own brands to OSCA SCM. The same applied for the two existing logistics partners. In a second step, the remaining suppliers from Europe and other countries – such as Turkey – will be integrated into the system so that OSCA SCM is used by more than 200 suppliers.
• OSCA SCM contains four service areas for LUQOM Group:
• Delivery Planning & Dialogues: This is where the purchase orders are confirmed by the suppliers.
• Booking & Shipment: This involves the suppliers’ transport booking process with the freight forwarders, the storage of shipment data (manually or via TMS connection) by the logistics service providers and the upload of mandatory documents.
• Delivery to DC: This is where the delivery process at the warehouse is controlled. The forwarder and warehouse employees coordinate the time of goods delivery.
• Reporting: Here, the system offers comprehensive reporting and analysis functions.
According to Keyser, the software was implemented quickly – just as planned. Training in German, English and Chinese also took just two weeks. Some employees and partners initially found it a little difficult to get used to the new workflows. “But anyone who recognizes the advantages also understands the change. OSCA brings transparency to the supply chain. There is now only one central system for communication and document exchange for everyone involved,” says Keyser. For him, there is no alternative to a ‘digital twin of the supply chain’.
Whether ‘Lindby’ ceiling lights or ‘Arcchio’ wall lights: Five employees in Keyser´s team can already manage 2.5 million orders per year via OSCA in the first stage of expansion. The products from Lampenwelt’s own brand are delivered via two logistics service providers to a multi-user warehouse with a total area of 45,000 square meters near Fulda, which is managed by a contract logistics provider, as well as to the company’s own distribution center, which is also located in Hesse.
Although OSCA has only been in operation since December 2022 and the connection of the remaining suppliers is yet to follow, SCM expert Keyser is already excited by two results: Lead times have been reduced by around 15 percent. The company has achieved even better results when it comes to reducing the amount of work involved in ordering lamps and the like: Keyser was able to measure around 20 percent. He anticipates a reduction of up to 50 percent – after the end of the second expansion phase. “The solution has also been well received by the retail specialists in Asia. Our Asian colleagues also benefit from the centralized solution in terms of data exchange and communication. A large number of emails are now a thing of the past,” says Ludger Tillmann, General Manager of LUQOM Asia.
Although the current project is not yet finished, Keyser is already working on others – the connection of other subsidiaries such as QLF and Lampemesteren to OSCA. The interfaces will be implemented shortly. Light should therefore soon be shed on the other supply chains.
Similar News: