Sustainable Sheds
8th September 2024
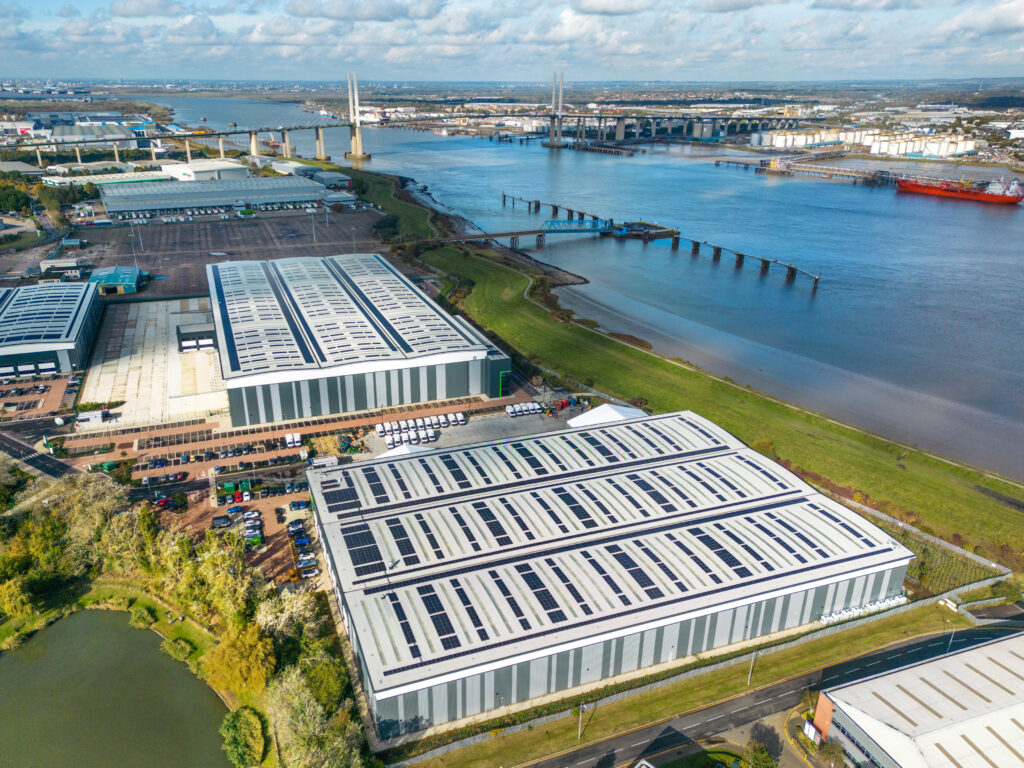
Warehouses are often assumed to be dark, drafty and dreary. Perhaps that impression needs to change. David Priestman visited a new logistics park by the River Thames in London to learn why.
Crossways Commercial Park, near Dartford, Kent, is being completed by Goodman with a focus on high build quality, sustainability, innovation and the wellbeing of staff. The market for warehousing is very competitive and Goodman wishes to position itself at the forefront of these trends and new customer needs. The company is committed to reducing energy use and maximising the sustainable use of resources, including renewable energy.
Demand for distribution centres (DCs) continues to be influenced by the need to maximise productivity and efficiency, while building greater supply chain resilience. Goodman adopts an own + develop + manage model that sees the company retains ownership of the buildings and land, leasing it for the long term (minimum of 10 years).
At the 37-acre Crossways site Goodman has three completed DCs, two of which are occupied, and three new units to follow by the end of next year. Unit 1, known as Crossways 241, is the largest, at 240,000 sq.ft and currently available. “Kent is relatively affordable and has short routes to Dover and Eurotunnel,” George Glennie, Development Director for southeast England told me. “We have lots of customers in the food sector, some of whom we do retrofit work for, such as adding solar panels.”
Let there be a Harvest for the Warehouse
A ’fabric first’ design ethos by Goodman means minimising energy consumption via highly insulated, airtight warehouses built at the best orientation and benefitting from natural light. Unit 1 has a full, curved rooftop of solar photovoltaics (generating 905,900 kWh), carbon neutral external cladding, rainwater harvesting, SolarWall ‘Transpired Solar Collector’ heating and cooling system (installed on the southern elevation), automated LED lighting, EV charging, cycle shelters and landscaping. Unsurprisingly, Crossways has achieved BREEAM Excellent and EPC A+ ratings. The greenest, swankiest shed I have ever set foot in. And I’ve seen a few!
Glennie gleams at the quality of the new builds. “We can put in as much power as is necessary to future-proof the site. The cladding is adaptable for temperature-controlled requirements, and the solar power can save our customers money as they have the opportunity to purchase the energy generated. This is offered at a discounted rate to the cost of grid power.” He says that many customers use a DC as the company’s headquarters too and appreciate the high-spec office space included. “I like this business park because it’s a campus environment with nice walks to go on, rest areas, several small lakes and a train station for commuting (Stone Crossing). This aids staff retention. There are other logistics businesses here, such as Davies Turner and Amazon. We’ve built a really good product here. We can control the outcome, which means happy tenants,” he concludes.
Catering Supply Chain
Goodman has seen increased interest recently from companies in the food production sector, compared to traditional third party logistics providers. One such tenant is Albion Fine Foods (part of Vestey Foods), a food ingredients supplier that chose Crossways’ Unit 2 in the summer of 2022 because it is adjacent to the M25 and within the huge Greater London catchment. The transport links enabled Albion to reduce transit times and delivery miles to its restaurant, pub and other catering customer sites.
Harry Jennings, Albion’s Finance Director, proudly provided a tour of the facility, which the company moved into in July 2023. With a £70m turnover, 100 vans and 310 employees, including drivers, it is a fast-growing firm. 4500 sku items are stored in the DC, ranging from literally every ingredient imaginable to sundry kitchen supplies. These are picked overnight and supplied next day to any caterer in the southeast, or further afield if a big customer. “We were in Tonbridge, Kent,” says Jennings, “but we couldn’t hire more drivers and warehouse staff there. We looked at lots of units. Crossways has lots of yard space. With our own fleet we need space for vehicles and we have 11 loading docks so our delivery vans can constantly rotate at the bays.”
There is ample scope here for Albion to continue growing. The DC has a 24/7 operation, only closing for Christmas, and uses Koerber’s WMS. As well as the ambient, chilled and frozen storage zones of the warehouse there is a commercial kitchen that makes and prepares value-added things like salads, sauces and marinades, as well as developing menus for chefs. By having food pre-prepared restaurants save considerable time and money. Albion also operates a canteen for its staff and drivers here.
I asked Jennings about Albion’s inbound supply chain. “We have thousands of suppliers, especially from the EU,” he says, pointing out that a French subsidiary has been opened to alleviate the foolish disasters of Brexit. “We can import a container of food with our own driver and truck,” he explains. “We’ve now got the stock space and ample racking. With the mezzanine we’ve gained lots more, thanks to the building height (14m),” which permits high-bay aisles and 12000 pallet spaces. “There’s a pool of logistics workers here,” he informs me, “so we now get more applications than we need for vacancies.”
Strategically located developments are, of course, crucial, which is why Goodman, listed on the Australian stock market (ASX), invests in sites that place customers closer to consumers. Across 14 countries the company has £44bn of assets under management, 435 properties and 1700 customers. It aims to offer facilities in all the ‘global gateway’ cities. If the others resemble Crossways then logistics has a very green future.
Similar news…