High Throughput; Tried & Tested
25th November 2024
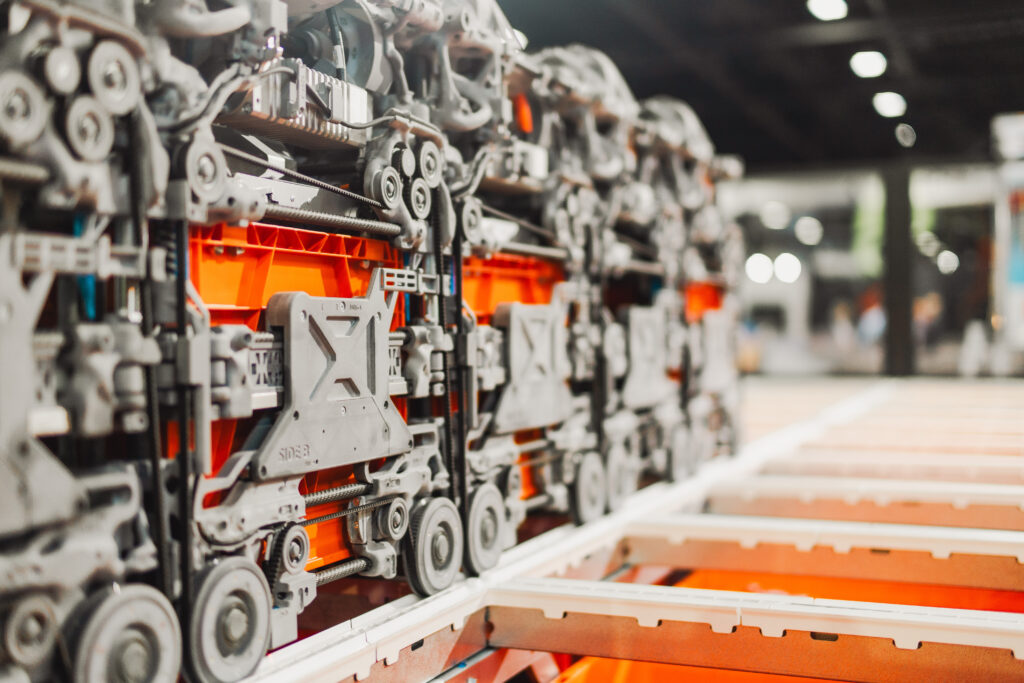
David Priestman visited Ocado’s Luton customer fulfilment centre (CFC) in Bedfordshire, England, to experience one of the most sophisticated hive storage and retrieval systems in global logistics.
CEO of Ocado Intelligent Automation (OIA) is Mark Richardson, who spoke to us for our May issue (p 30-31) about the company’s OSRS system and ambitions to become a major force in non-grocery warehouse automation systems. He provided an extensive tour of the Luton CFC, which opened last year. The CFC has rapidly scaled its operations to approximately 55,000 orders per week since its go-live in September 2023, relative to a planned design capacity of approximately 65,000 orders per week. With its more than 500 restless bots this facility ships 250 units per labour hour, with a target of increasing that to over 300 per hour when all the automated picking robots have been installed.
OIA’s bots are deliberately unclad and without skirting. This makes them lighter, shows the inner workings, makes maintenance easier and perhaps feeds greater acceptance by users – the warehouse engineer staff programming and monitoring them. They have luminous green lights visible to the engineers, which turn red should a bot be in error mode, which happens very rarely, Richardson assures me. The new 600 series bot is now being manufactured, featuring more plastic components and smaller motors to make it lighter and even faster, whilst using less power.
Action all induct stations
Most of the products in the OSRS grid are newly arrived items. They are brought on pallets to the induct station, adjacent to the metal grid, where items are manually unloaded and unpacked before being fed into the 200,000 white, injection-moulded plastic storage bins that are used inside the grid. In the future OIA may switch to auto-depalletization technology for this. The company is also now introducing metal bins, with a similar weight, that are fire-resistant to protect assets. Customers can choose between all plastic bins with firewalls in the grid, a combination of materials, or all metal for very cautious environments.
The manned pick stations, situated in a ‘tunnel’ underneath the centre of the grid to keep products closest to the pickers, are designed by Ocado and manufactured by a contractor. Pickers use a visual system featuring a large screen that shows images of each product to be taken from a storage bin and placed into a delivery tote. The screen shows the picker exactly where items are to be placed as there are 3 plastic carrier bags inside each delivery tote. “No voice picking is used,” Richardson explains, “as we’re visually presenting the exact product to be picked.” It’s intended to provide a ‘gamification’ experience for staff.
The ambient part of the Luton OSRS grid is 21 totes high, with the chilled zone being just 8 high (well above ground level). The delivery bins sit inside the storage totes that always remain in the grid. Between two and four hours’ worth of delivery items are kept inside the grid at any time, waiting for their delivery departure slot. This means the OSRS acts as a despatch buffer, which is very effective as, whilst customer delivery times are from morning to late evening, picking inside the grid should be a 24/7 operation. For reference, the average Ocado grocery order consists of 46 items.
Typically, there are around 20 customer deliveries per individual van route. Items for each van are fetched quickly from the grid to be loading manually in roll cages, as well as via some automatic loading systems.
Choreographed picking robots
The Luton OSRS currently has 45 on-grid robotic picking arms fixed in position on top of the grid, above the picking tunnel. They are spread all over the top of the grid; 22 are in the ambient zones, 23 in chilled. Each one can reach to and pick from the 8 storage bins surrounding it. The system brings bins into any of these 8 locations, some are storage bins, some are delivery totes. The robots then do the necessary picking and placing, quickly but precisely. They will be added instead of installing more manual pick stations, which there is space for in the tunnel. The robotic pick solution at Luton is currently picking around one-third of the volumes at the CFC. At target, OIA expect approximately 70% of the range will be picked robotically, with a high proportion of the chilled goods, so as to keep temperature-controlled products inside the grid.
“We tried ground-level robotic picking,” Richardson informs me, “but we decided that on-top was better. We’re slowly teaching the robots and driving productivity up. This will be our most productive warehouse. We can use any robotic arm on it as the magic is in the software. The robot mustn’t just drop an item but place it in the best spot in the delivery bin.” The picking robots are being rapidly deployed for large-scale use across other Ocado and grocery customer sites internationally, and they can be used for non-grocery items too, of course.
The Luton CFC is the most advanced Ocado site in the world and it represents a complete step change in the productivity that can be achieved. Not only does it use Ocado Group’s bot and grid technology (as opposed to the 10 miles of conveyor at the company’s first-generation CFC in Hatfield, Hertfordshire), but it also houses OIA’s latest automation.
Large scale use
The use case for installing an OSRS is based on leading-edge efficiency and the proven expertise that Ocado has gained over 20 years using it as sites like Luton for up to 50,000 sku items. “If you have a demanding use case then we can really help,” says Richardson. “We’re not new to materials handling, it’s tried and tested. We’re more interested in the productivity of the whole site than the speed of individual machines. General merchandise warehouses are ideal, as is pharma, apparel and fashion, plus small consumer electronics.”
OIA can also configure the set-up to include picking some items outside the grid for warehouse staff to do value-add things like packaging and personalised messages before despatch. With the picking robots in operation the company is now gaining more large-scale use-case experience. “Whether our system is superior to competitors or not,” Richardson tells me, “the expertise we’ve gained is the key. We’re fully ready to deploy OSRS with picking robots. We’re not bolting it on, it comes with the grid and is well thought-out.”
Simply the densest
OSRS is scalable, with no limit or maximum breadth. Richardson claims that OSRS is the densest ASRS system available, thereby maximising footprint and ideal for new greenfield site distribution centres, as well as retrofitting an existing DC. It can be used for ambient goods and with a cold store. Above all, it is seriously fast, due to the advanced communications with all the bots. McKesson, the large Canadian pharmaceutical distributor, is going live next summer with an OSRS for retail store replenishment.
Next year’s LogiMAT (where Ocado are in the same hall as us, Hall 8), ProMAT and IMHX shows should see a good deal of interest in OIA’s booths, from both customers and competitors.
similar news