Navigating the Supply Chain Maze
28th February 2025
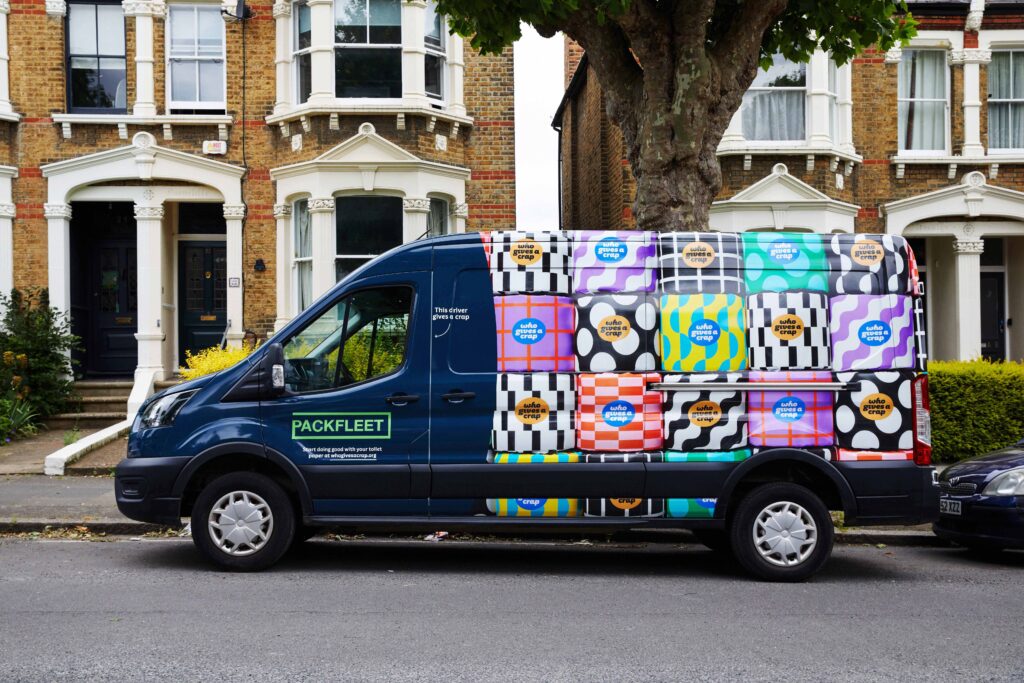
Aaron Geiger, Managing Director of Manufacturing and CPG/Retail for ORTEC, looks at Strategies businesses can deploy to optimize Last-Mile Deliveries.
Supply chain optimization has become a critical factor in maintaining a competitive edge. However, many companies still struggle to effectively implement AI-powered solutions for their supply chain. The disconnect often stems from a misalignment between C-level decision-makers and operational teams, leading to suboptimal results and missed opportunities for true optimization.
These are important decisions because a growing number of logistics professionals admit they aren’t optimized enough in their operations. Over half of respondents (52%) in a recent survey rated their organization’s current last-mile delivery planning effectiveness as below ‘excellent’ or ‘good.’ Additionally, the survey found that nearly 40% of respondents need to adjust delivery routes multiple times per day due to unexpected delays, emphasizing the pressing need for innovative solutions in logistics.
Understanding The Role of Software Optimization
One of the primary challenges in implementing AI and software solutions is the lack of a holistic view of the supply chain. Many companies focus solely on individual components, such as warehouse management or transportation logistics, without considering how these elements interact within the broader ecosystem. This siloed approach often leads to inefficiencies and missed opportunities for optimization across the entire supply chain.
Data quality and integration pose additional challenges. AI and machine learning algorithms rely heavily on accurate, comprehensive data to generate meaningful insights and recommendations. However, many companies struggle with data silos, inconsistent data formats, and outdated information, which undermine the effectiveness of even the most sophisticated software solutions.
Smarter Load Optimization
Moving beyond these implementation challenges, let’s examine the critical area of load optimization in warehouses and distribution centers. Many companies today are utilizing optimization software that focuses solely on downstream processes at the warehouse level. Even though the approach yields some benefits, it significantly limits flexibility and responsiveness to changing market conditions.
Forward-thinking companies are recognizing the need for more sophisticated software solutions that allow for upstream optimization. This strategy enables companies to make last-minute changes to orders, responding dynamically to shifts in demand or supply chain disruptions. By optimizing loading upstream, companies can better align their operations with real-time market conditions, improving efficiency and customer satisfaction while minimizing food waste.
A key component is the ability to perform dynamic builds, reconfiguring truck loads with proper ‘stackability’ to ensure each axle is weight-optimized while also considering the unique temperature control requirements of different products. These capabilities allow companies to maximize the number of pallets loaded onto trucks without risking fines during road checks or compromising product quality.
Many industries, including grocery as an example, face unique challenges in load optimization due to the various temperature control sections required in a truck. Traditional loading strategies based on the order of customer drops often result in inefficiencies, requiring the removal of several pallets at each stop to reach the varying temperature sections of the truck. These strategies not only increase delivery times but also risk compromising the temperature integrity of perishable goods.
Today’s more advanced load optimization software strategically orchestrates the loading of the trailer to address these challenges. These solutions consider product compatibility, determining which items should be safely stacked on top of each other in a pallet and within the truck. They also optimize the placement of goods in different temperature-controlled sections of the truck, minimizing the need to remove non-customer-specific pallets at each stop.
By implementing these advanced optimization techniques, companies reduce the number of pallets that need to be moved at each delivery point. Industry observers believe this not only improves efficiency but also reduces the risk of temperature fluctuations for sensitive products. The result is a more streamlined delivery process that maintains product quality and freshness while reducing operational costs.
Is Your Routing Truly Dynamic?
The final piece of the puzzle in supply chain optimization is dynamic routing. Many companies still rely on static routing methods, which lack the flexibility and agility required in today’s fast-paced business environment. The limitations of static routing become particularly apparent in the face of unexpected events, such as traffic disruptions, weather conditions, or last-minute order changes, all of which significantly impact the delivery of goods.
Dynamic routing offers a solution to these challenges by continuously optimizing delivery routes based on real-time data and changing conditions. This is particularly crucial in industries, where factors such as traffic, weather, and product freshness impact delivery schedules. Dynamic route optimization leverages advanced algorithms and real-time data to create the most efficient delivery routes, considering factors such as traffic patterns, delivery time windows, vehicle capacities, road conditions, and the specific temperature requirements of different product categories.
However, simply investing in dynamic routing software is not enough for companies. They need to build the right strategy to adopt and implement the technology effectively, which is where the disconnect between C-level executives and operational teams often becomes most apparent. While C-suite leaders may be eager to invest in cutting-edge routing software, operational teams need support in refining their processes before the software is truly effective.
By combining AI-driven insights with human expertise, companies will be positioned to make more informed decisions about customer service levels. Sometimes, this might mean adjusting delivery frequencies based on a comprehensive analysis of costs and benefits. For example, a company might decide to reduce deliveries to certain customers from four or five times a week to three, based on factors such as order volume, product mix, and delivery costs. The strategic approach to routing optimization leads to greater cost savings and improved overall efficiency without compromising product quality or customer satisfaction.
The logistics industry faces unique challenges in supply chain optimization, particularly in areas such as temperature-controlled logistics and product freshness. However, by leveraging advanced technologies and strategic thinking, companies can overcome these challenges and achieve significant improvements in their operations.
As the logistics industry continues to evolve, companies that successfully implement these advanced optimization strategies will be best positioned to thrive in an increasingly competitive and complex marketplace.
similar news