Discount Retailer Awards Contract for new DC
27th March 2025
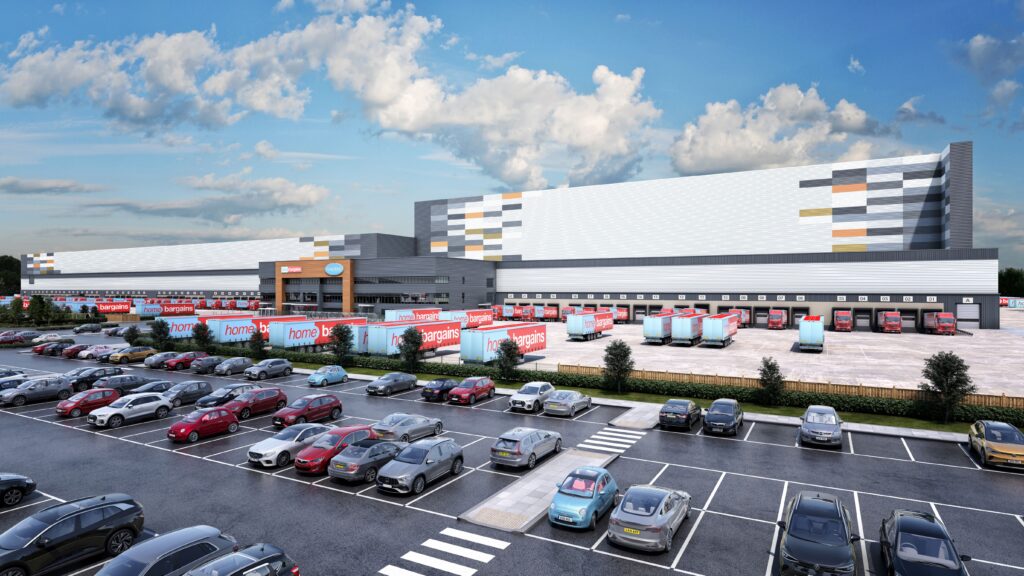
The British family-owned enterprise TJ Morris awarded WITRON a contract to design and implement a circa 1 million sq.ft distribution centre (DC) for food and non-food products. The highly automated facility in Doncaster is designed for a daily picking capacity of 646,000 cases and will supply over 300 stores from a range of 10,000 different dry goods from mid-2028. The signing of the contract is a particular vote of confidence, as a TJ Morris distribution centre of similar size will be put into operation by WITRON in St Helens in May 2025, and WITRON have already received the contract for the Doncaster Distribution Centre.
TJ Morris is one of the largest privately-owned companies in the UK and one of the fastest growing retailers in Europe. The innovative WITRON technology with its many benefits in terms of cost-efficiency, flexibility, ergonomics, and sustainability enables TJ Morris to keep this service level high throughout the expansion plans.
Logical Consequence
The distribution centre in Doncaster has the same design as the one in St Helens, with all product groups and logistics areas – from receiving to truck loading – integrated end-to-end into the highly automated overall process. All processes are controlled by an intelligent warehouse management system from WITRON. The material flow includes 470,000 pallet, tray, and tote storage locations, 104 stacker cranes, as well as more than 15 kilometers of conveyor technology – all designed and manufactured at WITRON’s headquarters in Parkstein.
Daily Picking Capacity
The automated system is designed for a daily picking capacity of 646,000 cases, which are picked with WITRON’s Order Picking Machinery (OPM) including 32 COM machines, the Dynamic Picking System (DPS), and the semi-automated Car Picking System (CPS). The dispatch of the picked load carriers is optimized by a fully automated shipping buffer – “just-in-time”, sorted by routes and stores, in the optimal truck loading sequence, considering the storage space utilization on the truck.
“In addition to the benefits for consumers in the stores, a decisive criterion for TJ Morris was also the focus on the employees who will work with WITRON technology in the distribution centre in the future. They will benefit from state-of-the-art, ergonomic workstations, which is an enormous competitive advantage in times of labor shortages”, explains Duncan Pointon, WITRON’s UK Sales Manager. „In addition, the issue of sustainability, is addressed in many different ways – for example through significant CO2 savings due to densely packed load carriers, optimal truck utilization, and fewer trucks on the roads. Furthermore, through space savings in construction and by significantly reducing excess goods, breakage, and waste.”
similar news