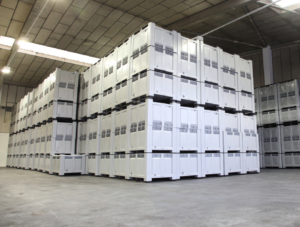
In December 2023 alone, £45 billion worth of goods were imported to the UK… Read more »
In December 2023 alone, £45 billion worth of goods were imported to the UK… Read more »
UK food-on-the-go retailer, Greggs, have announced it’s entering into a lease agreement for a… Read more »
Robert O’Donoghue from Hyster Europe reveals the key trends and challenges affecting industrial manufacturing… Read more »
Rite-Hite, one of the leading manufacturers of loading bay and health and safety equipment,… Read more »
Manufacturing and reuse of wooden pallets increased significantly according to the most recent survey… Read more »
Oceaneering’s Mobile Robotics group has added an extra production campus in Orlando, Florida. The… Read more »
New research has revealed the emergence of major shifts in globalisation, as companies rush… Read more »
Returnable plastic transport packaging maker bekuplast has received at its manufacturing facility a new… Read more »
To ensure that Witron remains a strong partner for its customers and employees in… Read more »
Interroll has laid the groundwork for a significant expansion of its product portfolio at… Read more »
A new semi-rugged laptop has been launched by technology company Getac. The next-generation S410… Read more »
With its AFR Systems (Alternative Fuels and Raw Materials) business unit, BEUMER Group supports… Read more »
SupplyOn, a global collaboration platform for the manufacturing industry, is celebrating its 20th anniversary.… Read more »
Microlise has joined manufacturers’ organisation MAKE UK, becoming a member alongside the UK’s leading… Read more »
Rite-Hite, the loading bay safety business, has signalled a major investment in its European… Read more »
Linde Material Handling’s Remanufacturing Centre in Velké Bílovice near Brno (Czech Republic), which was… Read more »
Following recent news that insolvency in the manufacturing sector is at a five-year high,… Read more »
Don-Bur is investing £4 million in new plant, software and training to mass-produce a… Read more »
On-demand manufacturing platform Xometry has decided to implement Infor CloudSuite Industrial. Built on highly… Read more »
Softbox Systems, a provider of cold chain packaging for the pharmaceutical industry, is to… Read more »
Peli BioThermal, a global name in temperature controlled packaging, is to expand its European… Read more »
Synchrono, a leader in modern demand-driven manufacturing software and synchronization technology, has released a… Read more »
The Galway, Ireland manufacturing facility of Thermo King®, a manufacturer of transport temperature control… Read more »
Vanderlande has launched its new Manufacturing and Distribution Centre in Georgia (GA), USA. The… Read more »
With revenue growth remaining challenging, almost half (48 per cent) of manufacturers are racing… Read more »
TCMs UK dealers visited the companys Pamplona, Spain production facilities recently to see first… Read more »
Combilift Ltd, the specialist manufacturer of 4-way forklifts and other innovative materials handling equipment… Read more »
Combilift Ltd. is to invest 40 million over the next two years in a… Read more »
Ivanti, a tech company that breaks down barriers between IT and security so that… Read more »
Chelmer Foods, a leading supplier of dried fruits, nuts, seeds, and pulses for industries… Read more »
Looking ahead to 2025, Supplyframe shares its predictions on the electronics supply chain industry,… Read more »
An acceleration in strategic reshoring moves by businesses worldwide to shift operations and supply… Read more »
Fly By Nite, renowned specialists in trucking, logistics and warehousing for the entertainment industry… Read more »
Delta, a global supplier of power management and a provider of IoT-based smart green… Read more »
Logistics Business has published a new eBook on warehouse automation and robotics, in association… Read more »
Linde Material Handling (MH) is replacing its existing range of electric forklifts with a… Read more »
Rolls-Royce is struggling with persistent supply chain issues that are impacting its engine production… Read more »