AI and AR: powering Logistics 4.0
27th July 2021
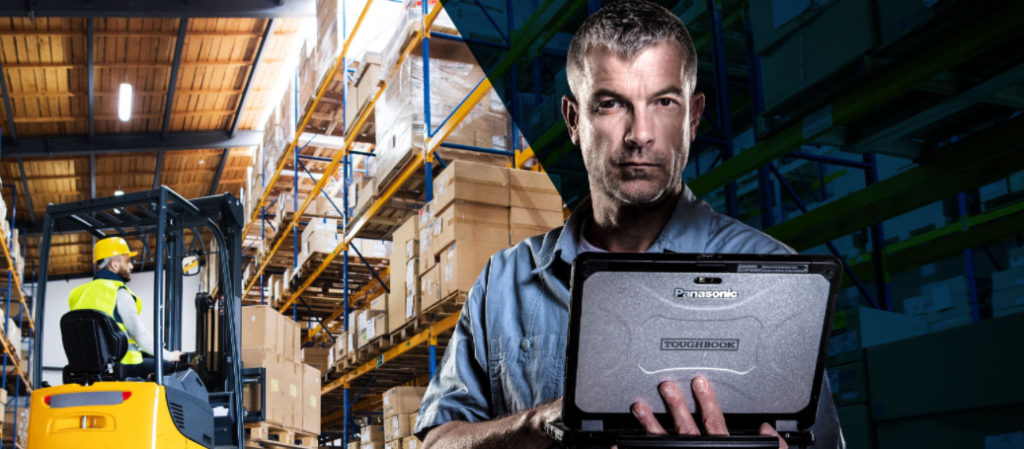
When it comes to Artificial Intelligence (AI) and Augmented Reality (AR), what benefits do they really offer for businesses in the logistics sector? In this article – written by Luca Legnani, Panasonic’s European Marketing Manager – we look at how logistics businesses are applying AI and AR to their operations today, and how easily the technology can be integrated into existing business processes.
Switch on the news in any given week, and you’ll no doubt see a story about a ground-breaking new technology which will change the face of the planet. The truth is, for the majority of the world’s businesses, newly emerging technologies are too expensive and too high risk before they’ve become adopted – and tested – by the masses.
But waiting for a technology to become best practice can leave you trailing behind your competition. So what are the practical applications for technologies like AI and AR? And can they really deliver tangible benefits – through efficiency, operational costs and return on investment?
AI: The catalyst of Logistics 4.0
AI has been around for many years, and its use is widespread. In fact, most of us use it in some form every day: unlocking your phone with facial recognition technology, the algorithms which dictate your social media feeds, even using a search engine is powered by AI.
When it comes to logistics, AI’s applications range from simple tasks like optimised freight route-mapping, to the more experimental, such as Google’s Tossing Bot1: a robot arm powered by machine learning technology, and designed for use in pick and pack warehouses.
But warehouses don’t necessarily need a robot which can throw to successfully integrate AI. The rise of the automated warehouse has been taking place for a few years, and although still in its infancy, is viewed as highly efficient. In the UK logistics market, grocery giant Ocado built an automated warehouse in Andover. Its ‘hive’ of 1,100 robots successfully processed 3.2 million items per week, picking, lifting and sorting online shopping orders.
Even this pales in comparison to JD, whose warehouse on the outskirts of Shanghai processes 200,000 orders each day – a feat which would normally take hundreds of employees to achieve. Using image scanners, the robots ‘check’ packages in just microseconds, before identifying where each one should be placed. The facility even has driverless forklifts to deliver the processed orders to its corresponding delivery truck.
In fact, automated vehicles are also exploding in the world of logistics. In last-mile logistics, there are a number of autonomous ‘delivery bots’ already operating across the world. From depot to door, each one can intelligently plan a delivery route and avoid obstacles to fulfil an order.
But completely automated warehouses and delivery bots are fairly big investments – and so, can result in unfortunate losses. In the case of Ocado, for example, an electrical failure caused a fire to break out at the Andover facility, putting it out of action. Not only did the fire cost the online supermarket £100m, it also resulted in the business cutting 400 jobs as a result.
It’s much more likely then, that for the foreseeable future of the logistics industry, it will be simpler uses of AI-initiated automation and optimisation that will gain the largest traction. Warehouse Management Systems (WMS) would be boosted with the integration of AI software, predicting peaks and troughs in demands, and allowing supply chain managers to make informed decisions about planning resources. And cognitive automation within back office logistics means contract management can also start to be automated – with some studies suggesting there would be more accuracy as a result.
These are examples of smaller-scale, less expensive, realistic investments which offer a much quicker return. And, it’s a very safe bet that transportation companies are starting to implement these changes into their operations in order to augment their business processes.
AR: Offering a new perspective in smart logistics
Augmented Reality might not be used as frequently in our day-to-day as AI might be, but its popularity is growing. AR works by adding a layer of computer-generated virtual reality over a view of the real world, most commonly recognised from social media filters.
In the logistics world, the difficulty arises when ensuring wherever AR is integrated into a working process, it’s done so in a way which is useful, seamless and user friendly. For example, although Smart Lense technology is being tested – contact lenses with Augmented Reality capabilities – it’s highly unlikely that a significantly large workforce could all be encouraged to use them where there are alternatives. Smart Glasses, however, are a different ballgame.
Often predicted to be the next game-changing technology, Smart Glasses could offer a visual overlay via their lenses. For practical applications, this could mean 3D illustrations are provided for employees loading cargo into a shipment, ensuring the best use of space, and minimising the risk of incorrect sorting. There are also high hopes for the technology’s ability to enable remote expertise sharing.
And the benefits aren’t just for inside the warehouse: last mile logistics can also benefit from Augmented Reality implementation. If the technology is integrated into a device with a camera, such as a tablet or smartphone, it can remove the need for barcode scanning and data input, using the camera to automatically process and sort data.
Panasonic’s Visual Sort Assist (VSA) solution has already begun revolutionising the way large-scale logistics companies manage their warehousing processes.
A practical, business-friendly solution
For the most part, the best integration of new technologies seems to be where it naturally matches up with current processes. Upgrading current technology to newer versions which offer enhanced capability could be the best way forward.
At Panasonic, the TOUGHBOOK M1 RealSense is one option. A 7” tablet designed perfectly for use in the supply chain. Its AI-powered RealSense camera with 3D mapping technology allows the user to take accurate measurements from a safe distance; optimising warehouse storage, organising shipments and calculating load dimensions becomes a much easier task.
It also offers all the benefits of rugged technology; resistance to drops of up to 1.8 metres, built-in water and dust resistance, a sunlight viewable screen, and a glove-compatible touchscreen – all features which make it ideal for use in a warehouse environment, last-mile delivery or supply chain management roles.
And then there’s the TOUGHBOOK M1 Thermal Imaging solution, which allows users to record, analyse and document temperature surfaces from a distance. Plus, all data can be intelligently processed, meaning less administration time and fewer human errors.
Not only could the use of devices such as this one lead to greater efficiency, process optimisation and reduced human error, it could also lead to a huge saving in TCO.