EPG automates Al Maya’s central DC
11th October 2021
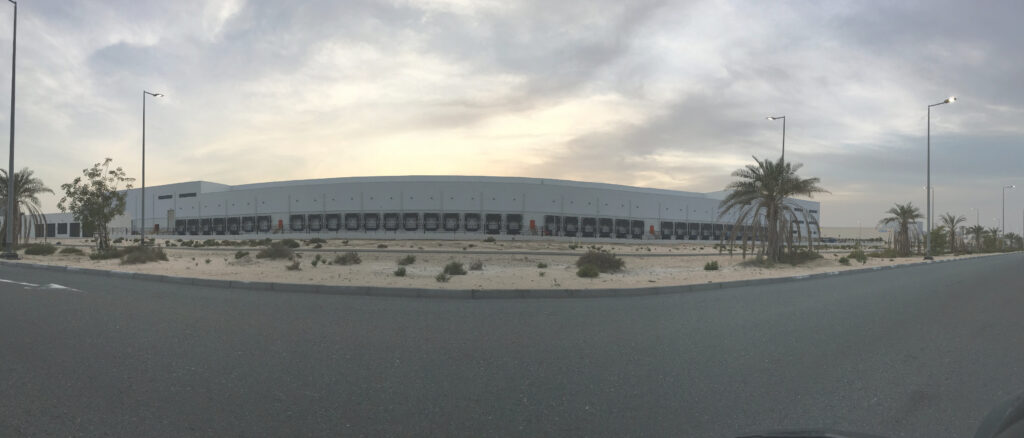
Al Maya Group is a Dubai-based conglomerate with multiple business verticals: food and non-food products and over 90 retail stores in the Middle East including supermarkets, international bookstores, franchises, and many other lifestyle retail stores. In the food sector, the company serves the major supermarket chains in the region.
Handling sensitive and temperature-controlled goods is a challenge, especially since Al Maya has to offer a wide range of products to all the major retailers in the region through its distribution operations. All of this requires a well-functioning logistics operation.
In order to manage its existing processes and also ensure that it is well-equipped for the future, the company took the decision to automate the processes at its central distribution centre for all sectors with the EPG ONE Warehouse Management System (LFS). Al Maya also requested EPG’s consulting services to help design the different storage solutions and the overall structure of the warehouse. The company achieved its goal of having a state-of-the-art distribution centre with a WMS within a very short time – and without any disruption to ongoing operations.
“We are very satisfied with the development of the project as well as with the support of the EPG team on site and with the overall planning”, says Bharat Korwani, IT Manager at Al Maya Group. “The efficiency and level of detail with which the entire project was carried out really impressed us.”
As one of the largest FMCG distributors in the UAE, Al Maya supplies all the major retail stores in the region. The product range in the company’s distribution division is focused on fresh products purchased directly from the countries of origin. Premium customers of its distribution division include Carrefour, Lulu Hypermarket and other retail stores as well as its own supermarket chain Al Maya Supermarkets.
All the business areas in which Al Maya operates follow very different and unique logistical rules. In addition, the variety of products being stored is vast and requires the utmost sensitivity in handling, especially in the food segment. Up to 2,500 different items have to be managed. The main objective is to handle the goods based on best-before dates and in compliance with the FIFO (first in, first out) principle.
Al Maya predicted the development of this requirement way in advance and was correct to assume so. Due to the increasing order volume, operations can no longer be managed on the basis of old platforms.
EPG’s logistics experts developed a warehouse matrix to meet Al Maya’s requirements based on the key indicators that needed to be met in terms of warehouse structure and business requirements. As a result, EPG designed various storage areas and temperature-controlled zones, while also considering the specific requirements of the individual business units.
The introduction of customer classes A, B and C divides the distribution centre into reasonable units. Before this classification, the handling of the goods and the stock overview were mainly dependent on the experience of individual employees. FIFO handling and the secure administration of best-before dates were not possible without errors. Due to the different storage zones – rack storage, pallet floor, filling stations and floor storage – product groups can now be clearly assigned.
LFS ensures automatic control of the storage areas and offers maximum transparency with respect to the current stock. If required, replenishment is requested automatically. EPG’s warehouse management system LFS also controls the sorting of goods according to BBD (best-before date), product group and customer. The orders are assigned a storage location upon receipt.
Order processing is highly reliable with LFS, as the warehouse management system controls picking in sequences and – depending on the products ordered – according to priority and shelf life. The goods are assembled on pallets and then loaded onto trucks according to the sequencing, ensuring that the goods of the customer being supplied first are loaded last. More than 700 orders are processed in Al Maya’s distribution centre every day.
EPG organised the processes in the new 22,000 sq m distribution centre and planned the transfer of goods to this new warehouse facility without any disruption to day-to-day operations.
“LFS has helped us to manage our inventory and overall logistics operations for our FMCG distribution division in the most effective way,” says Korwani. “This has given us strict control over the operation. It has also provided us with complete visibility of our stock and helped us with BBD maintenance.”
“As a result of the implementation of LFS, we now have an effective supply chain operation and Al Maya is consistently able to deliver goods to our customers on time,” Korwani adds: “We were always able to count on EPG during the entire changeover process and the move. We are therefore confident that we will rely on the logistics experts at EPG for future projects.” Within a short space of time, Al Maya decided to introduce EPG’s LFS in two additional divisions.