Furniture company gains inventory visibility
13th October 2022
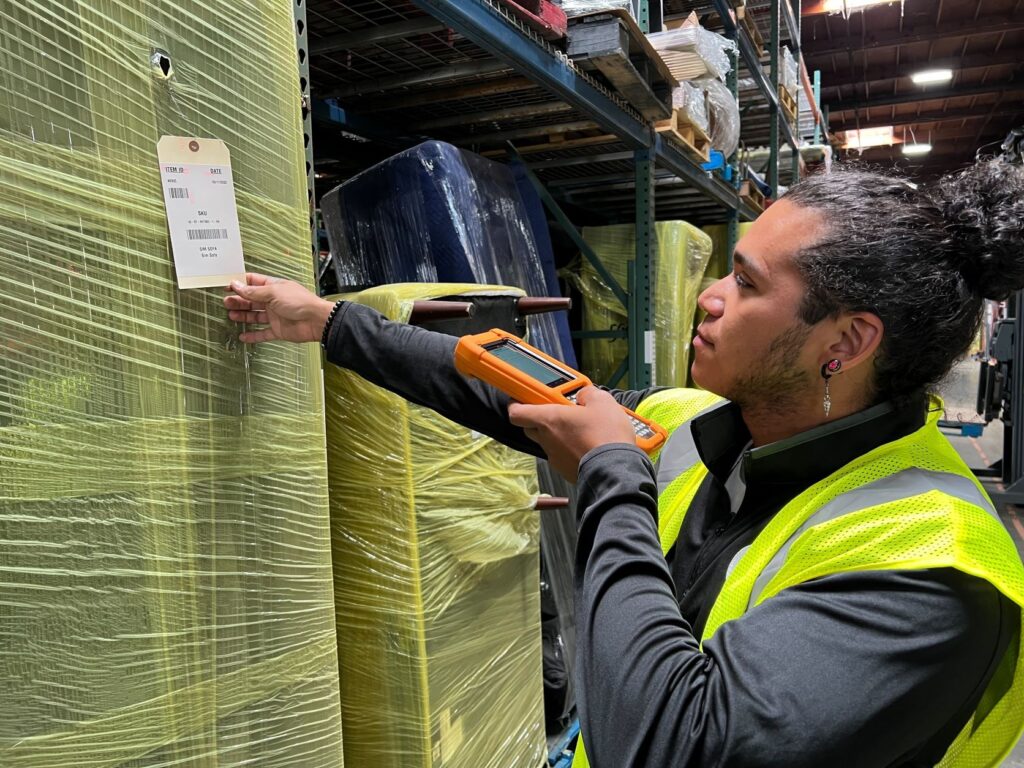
Rapidly expanding furniture company Oliver Space, which offers a fully circular home furnishing experience, is enjoying complete inventory visibility for the first time since implementing Synergy’s SnapFulfil WMS suite.
The San Francisco-based business – which not only delivers and assembles its premium quality furniture for customers, but also picks up and refurbishes used Oliver items to be made available at discounted prices – had struggled with inventory, picking and staging accuracy as the refurbishment returns side of the business ramped up.
However, the flexible and highly configurable SnapFulfil WMS has given Oliver Space the multiple tiers of stock and storage categories they require for precise inventory reconciliation. For customers, this means an even better experience as fulfilment is seamless, faster and more accurate.
David Guckian, Product Manager at Oliver Space, says: “We can now separate out, both in the system and the warehouse itself, all the different levels of stock and returns, which immediately optimised our inventory management capacity. We’d outgrown our initial 18,000 sq ft warehouse, but on moving to the new 30,000 sq ft DC realised a more consistent and reliable set of processes was required – and SnapFulfil ticks all the boxes.
“We looked at the full range of WMS solutions available, but around our key requirement of customisation, the so-called top tier systems were too labour intensive and costly to justify implementing. We treated it as a proof of concept and SnapFulfil quickly became the provider of choice because of their ability to work with us and facilitate all the process quirks and anomalies we required for a niche and complex business operation.”
The Oliver Space implementation was handled remotely, which is just as effective as on-site delivery as Synergy is a domain leader in digital onboarding. This saves customers time, money and resources, as well as aligning with their sustainability credentials.
Oliver Space was up and running in just under two months – even allowing for its more cautious approach to go live and use the test system to run live operations concurrently with its existing ERP until it had completed all necessary development internally.
Guckian explains: “The SnapFulfil team is highly responsive and together we worked through the various challenges that our operations model brings quickly and efficiently. They helped our engineering team implement API and other software so they would integrate fully, plus all the go-live training, UAT and testing was done in the staging environment – so that we were able to fine tune and dovetail everything in advance without interrupting our day-to-day operations.
“Consequently, when we were ready to go live it all went to plan and was like flicking a switch because of all the joint preparatory work we’d put in.”
Oliver Space is building the circular economy of furniture for a more sustainable future. With refurbished pieces becoming increasingly popular among an environmentally and fiscally conscious consumer base, SnapFulfil’s renowned reverse logistics capabilities are more necessary than ever. It also has the ability to scale up on user licence costs effectively during busier periods.
Guckian says: “As an exclusively online business we’re tech-centric, so Synergy and SnapFulfil are a natural fit and they understand where we’re coming from. Demand continues to grow, so we’re considering a second DC in Los Angeles early 2023, again powered by SnapFulfil, but I think we could be using their self implementation program that allows customers to onboard the system themselves.
“All we’ll need is their detailed rules engine training and we’re good to go. That’s how configurable their software is, and it will give us the control, independence and system expertise to manage our own roll out.”