Inventory management with drones
23rd May 2022
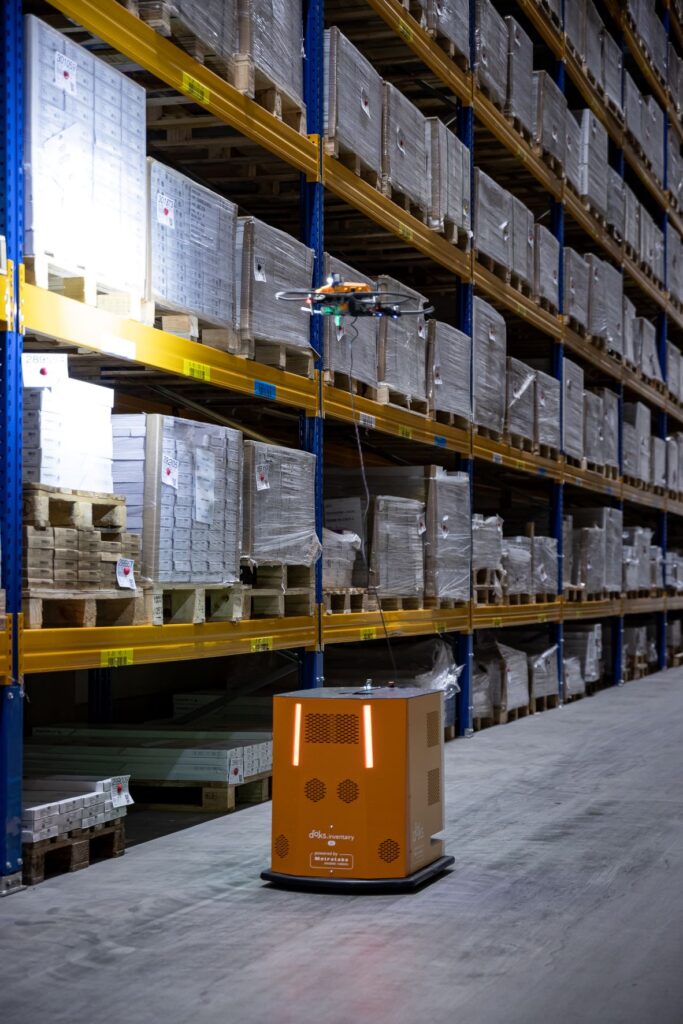
Inventory management may have just got a lot easier, writes Paul Hamblin, editor of Logistics Business Magazine.
You will probably need to travel far and wide in the world of warehousing to find someone who doesn’t find inventory management a thankless task. It’s essential, of course, but it sucks time out of the day-to-day process, not to mention valuable people hours. Picture the likely scene as it looks today: one forklift, two people in a basket, the driver joined by one other individual scanning each barcode, colour to colour or row to row in and every pallet position over storage racks of several tiers, with at least two scans per position. It’s faster than pen and paper, sure, but it has obvious drawbacks.
That could all be about to change. Drone technology is often excitably discussed in the world of logistics, with the highest-profile ideas (if not necessarily the reality) concerning last-mile deliveries, but inventory management by flexible drone is starting to gather serious weight as a workable concept.
Mike Becker, founder and CEO of German-based doks.innovation, is marketing inventairyXL, a drone- based inventory system that he says brings both full transparency and autonomy to the process, with the bonus of manual labour more profitably employed elsewhere in the facility and a much safer environment into the bargain. The premise is simple enough to understand – a ground-based Autonomous Mobile Robot (AMR) is the base from which a cable-attached drone has the flexibility to fly up to 14 metres, gathering and reporting intelligence back to the Rover as it goes (21m is in development).
“In fact, the drone is only the carrier for our sensors,” Mike Becker tells me. “In itself, it has no intelligence. We don’t need a drone per se, what we need is a practical system to move our sensors from the bottom to the highest points of the warehouse and the drone is the best current way of doing that. All of the intelligence is in our Rover, and everything is processed and controlled from within it. All the drone has to do is stay above the centre of the rover and fly up or down to the height needed.”
The drone collects barcode data, distance data and also captures multiple images of each pallet position, passing that information back to the Rover. Becker says that pallet damage detection is coming, as well as counting the items on a pallet. “There is also the facility to match the barcode reading from the image with that of the barcode scanner to ensure accuracy of information.”
Why drones? doks looked at using both telescopic arms and mini airships, but found the safest, cheapest and most beneficial carrier for the sensors to be the drone. Operational time is up to five hours, after which the Rover returns to its recharging station, a process that takes 3.5 hours.
How efficient is the image collection if the barcodes are awkwardly positioned on the pallet? “The barcodes must be outward-facing and visible from the front,” he points out. “When the system sees that something is not visible, it will flag the pallet position and the images can then be checked to see what the pallet contains, enabling a double check with the WMS.”
Then there is the cable attachment. With the drone able to travel up to 14m from the Rover, is there the possibility of entanglement with other objects or protruding objects from the shelves? Mike Becker is confident: “The drone will detect any obstacles first,” he claims. “Meanwhile, the length of the cable is constantly adjusted to the drone height, so it is used optimally.”
He founded doks in 2017, describing it as “a software company which uses hardware because we have to”. He started the firm with some colleagues after working on a logistics research project at a drone manufacturer in his native Germany, which was exploring inventory management using RFID. Fearing that such technology would prove too costly, he developed the ideas using drone technology and says he now has 20 pilot projects and sold systems working in several countries.
Becker is aware that logistics is a low-margins business but advises clients that serious transparency requires proper investment. Backed by angel investors in Germany and now with around 30 staff at his disposal, he plans to have 90 systems on the market by the end of this year. Germany, Austria, Switzerland, France, Benelux and the UK are principal target territories.
Installation is pain-free, he says. “We can perform a full demonstration in two to three hours on customer premises. No change in warehouse infrastructure is needed and the system can be set up in a matter of days. Autonomy and safety in the warehouse are big USPs,” he concludes.