Omni-channel integration during ongoing operations
21st February 2022
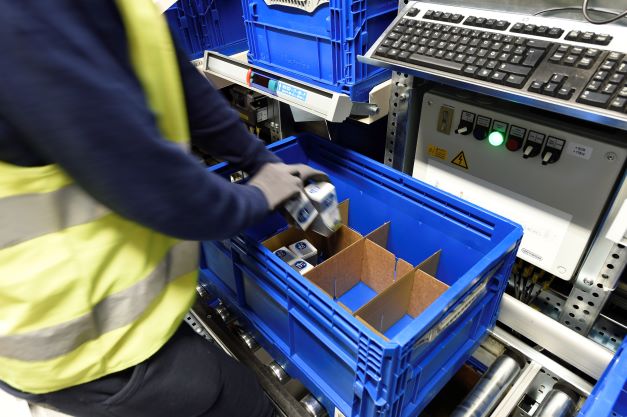
During ongoing operations, a high-performance logistics centre in Scandinavia is currently being expanded into an omni-channel logistics centre.
Since April 2012, the Finnish logistics service provider INEX Partners, a subsidiary of the retail company SOK, has been picking all general merchandise items at its Sipoo site using automated and semi-automated logistics systems from the general contractor Witron Logistik + Informatik GmbH. The 68,000 sq m facility near Helsinki used to exclusively supply the group’s 1,000 stores with more than 300,000 different items annually.
Now, the rapidly growing e-commerce business and the processing of click + collect orders will also be integrated. The goal of SOK/INEX is to process a wide variety of distribution channels centrally from a single logistics centre in a cost-efficient and flexible way. The operational start of the solution is scheduled for Q1/2022.
Flexible process structures
The INEX distribution centre in Sipoo is considered one of the most efficient logistics centres in Northern Europe, designed for a daily performance of processing more than one million units – clothing, cosmetics, sports items, electronic equipment, media, gardening equipment, and furniture.
Many of the non-food items are subject to fashion and music trends, or seasonal changes, which causes a constant change of products. Thus, highly dynamic and flexible logistics structures were required in the material flow processes right from the start. WITRON has already delivered a high degree of flexibility for the supply of approx 1,000 stores in the network.
This flexibility is now also a decisive factor in the development and logistical integration of further distribution channels such as click + collect and home shopping.
Decreasing logistics costs
The Covid-19 pandemic is not the only reason why the share of goods ordered online is also rising steadily in Finland. Whereas online orders could previously be manually picked by employees directly in the store and then shipped from there, a “critical mass” has now been reached at INEX, which means that this type of processing no longer appears economical. Also, given the increase in order volume, this process can no longer be covered by the employees in the store.
Faster, more flexible, but with significantly lower logistics costs – this is the process handling directly in the logistics centre. Here, employees pick small-volume items with the semi-automatic DPS (Dynamic Picking System) goods-to-person solution, pick-by-light guided from storage totes or storage pallets into the shipping tote.
With the semi-automatic pick-by-voice supported CPS (Car Picking System), large-volume or bulky items are stacked in the pick aisle from the storage pallet or layer trays into roll containers in a route-optimised manner. There is no physical separation between the e-commerce and the store logistics areas. Due to the generally low volume of e-commerce orders, totes used to pick orders for several online customers in parallel are created during the picking process.
In the following consolidation process, all small-volume and large-volume items are scanned and manually assigned to the respective customer order in a rack shelf, then packed and prepared for dispatch. Single-item orders will bypass the consolidation process. They will be scanned and packed directly from tote to carton. Shipping is also possible in form of click + collect orders to the stores.
High level of consistency
The processes integrated during ongoing operations are impressive in terms of their consistency. In principle, all items from the yearly 300,000 general merchandise product assortment are available to the SOK/INEX customers not only as a complete retail unit but also as “single items”. The formation of single items is generated dynamically as required in a separate process prior to picking. The logistics centre also handles all returns, which are returned to stock.
The merge of the e-commerce and click + collect distribution channels with the store business, storage, order picking, and shipping from one logistics centre is designed for future growth. Significant growth is expected in the coming years due to the successive change of the 1,000 SOK stores to the newly integrated omni-channel process and the increase of the overall e-commerce volume.
In addition to a further increase in premium customer service – both in the stores and in the online business – this means a variety of added benefits for INEX: cost-efficient and flexible processing for all distribution channels, processing with the same logistics personnel and the same technology, which includes a fast response to fluctuations and order peaks (e.g. Black Friday), no separate logistics areas and product storage for different distribution channels, a high level of sustainability in shipping, etc.