Optimise Existing Capacity to Save Costs
4th September 2023
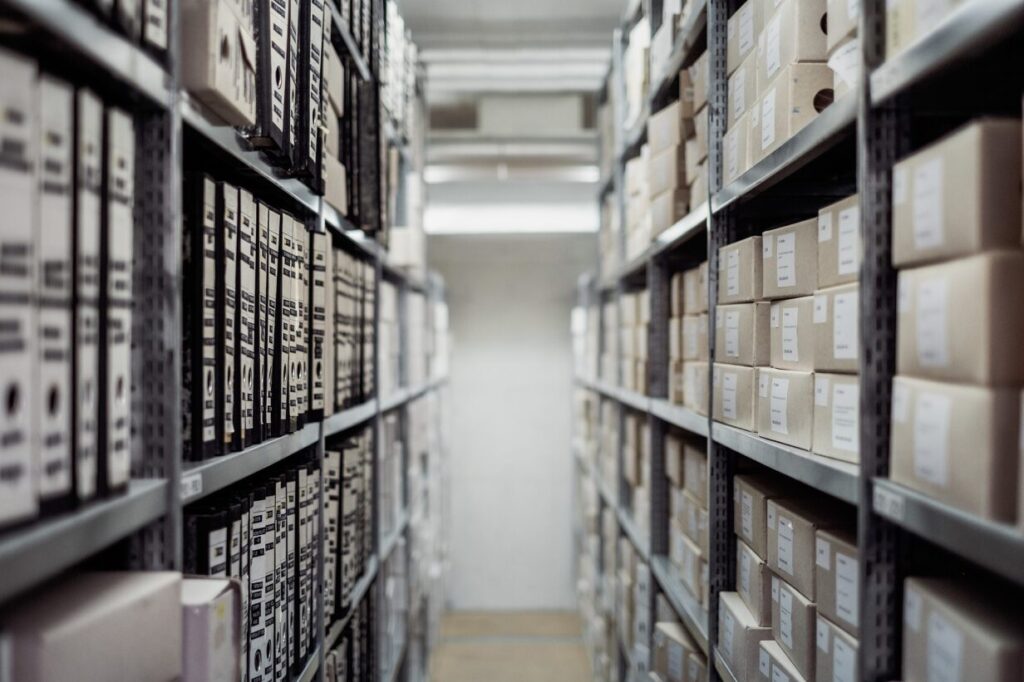
Growing businesses will sooner or later need more capacity in their supply chain to fulfil larger sales volumes. Adding capacity to an existing facility by introducing automation, reconfiguring current handling and storage equipment, or building an extension all offer a potential solution but can be expensive and disruptive to ongoing operations.
Another possibility is to relocate to a new and larger warehouse but leaving aside the costs and complexity involved the current lack of available new-build sites can make any such move impractical. Before making any decisions, growing businesses would do well to consider how to make the most of their existing facilities by utilising the power of warehouse management software (WMS) to maximise the efficiency of their current operations.
Using WMS to increase factors such as occupancy, throughput, and data and task accuracy can all help to increase the capacity of an existing warehouse. In doing so these businesses will avoid disruption and eliminate – or at least delay – the need for additional capital investment.
Any growing business involved with the supply of products will need to store and deliver more and more items. Building a bigger warehouse is one answer but can take time and generally requires a large investment. Industry data suggests there is over 51 million sq m of warehouse space available. Most of this is in-use and leading commercial agency Savills reported earlier this year that vacancy rates are below four per cent – a historic low. Another recent report suggested that the number of new build warehouses in the USA and Europe has decreased by a quarter over the past two years.
That means less available space is being chased by more potential occupiers, and no doubt the growth in e-commerce and home delivery is one of the causes. Another report from warehouse developer ProLogis estimates every extra £1bn spent online will require another 72,000 sq m of warehouse space. The rate of building barely keeps up with demand. Space is not cheap but there is hardly a motorway or major truck road intersection without a warehouse already there or awaiting planning approval.
Some businesses find that creating a new warehouse is the best option. For example, Ireland’s leading furniture importer and wholesaler reduced complexity and increased its stock volumes in 40% less overall space by investing in a new facility and implementing a state-of-the art WMS. While this approach suits some, many businesses have found they can use their existing storage facilities more efficiently. One way is to invest in new technologies and equipment that allows denser storage and/or faster throughput which can both increase overall capacity.
This might be as simple as replacing block stacking with pallet racking or wide aisle with narrow aisle configurations. Big changes often represent significant investment which, leaving aside the potential disruptions to ongoing business, may be beyond many businesses. For these a better approach is to use what they have more efficiently and this is the role of the WMS and related technologies.
Another change over the past decade is the type of warehouse operator. Ten years ago, most large facilities were operated by, or at least on behalf of, retailers. Today the largest proportion is operated by 3PLs, some as dedicated facilities but many others holding stock for multiple clients. Everyone is cost-conscious but 3PLs sell their services and base their costs on factors which include the number and size of pallet locations, overall storage capacity, picking capabilities and so on. For these businesses in particular, maximising efficiency and profitability with support from a WMS is vital.
There are only two realistic ways to increase capacity without a total reconfiguration. The first is to ensure maximum utilisation of every available space. The second is to increase throughput to get stock in and out more quickly. Efficiency gains like these are often possible because existing operators might not have noticed that their warehouse has changed in front of them while they have been busy focusing on their day-to-day operations.
Consider a hypothetical, but not implausible, business that setup or renovated its warehouse operation 10 years ago. At the time the operation required space for 2,500 pallets of various heights to meet customer needs, perhaps 1,000 at 1.6m high, 1,000 at 1.8m and the rest at 2.1m. That was the right configuration at the start and allowed a degree of flexibility to support the business requirement. The WMS was configured accordingly and operations have run smoothly since, or so it seems.
But over time it is not unusual for customers and their requirements to evolve. In fact, a small change here and there often means a business does not know immediately how many pallet locations, and of what type, they have. This might be because of changing the actual racking but adding equipment such as coolers or pallet wrappers might inadvertently block or restrict access to otherwise usable locations. Unless these businesses remember to keep their WMS up-to-date, and experience says that many do not, they will not be able to say how many spaces they have.
Nor for similar reasons can many businesses immediately identify the number of available free locations or their overall occupancy rates. Some free locations help with stock handling flexibility but too many can be a waste of resources and, ultimately, very costly for a business that is selling space.
Another possibility is that the profile of the stock is different, for example more larger pallets or fewer small ones, and so on. While it is of course possible to store a smaller pallet in any size location the reverse is certainly not true and that immediately leads to potential allocation issues that will restrict the performance of the overall operation. But even if it makes sense to store those smaller pallets in larger locations this is not an ideal use of the available volume in the warehouse – there could be up to 500mm of free but unusable space above a small pallet stored in the largest location. Again, unless the WMS is updated, it will be impossible to utilise all spaces with maximum efficiency.
Even in the best run warehouses there will be occasions when some pallet locations are out of commission. This might be as a result of accidental damage or to allow maintenance on the building infrastructure. This reduction in capacity will cost in terms of lost revenues but how many businesses will have a real-time view of their income generating capabilities or be able to see how much they are losing as a result of these outages. Certainly, with a properly configured WMS they would be able to tell. Another potential scenario, perhaps in extra-busy warehouses or where the stock profile has changed, is that demand for some locations exceeds capacity. This can restrict efficiency, for example preventing efficient putaway or requiring the excess stock to be stored elsewhere temporarily and potentially being unavailable for picking.
Experience suggests that almost any warehouse team experiencing problems like this will be unable to identify all of the problems, and their causes, immediately. But there is some good news and it does not necessarily require significant investment. Any decent WMS will help maximise stock management efficiencies but the best will incorporate business intelligence and analytics functionality. One example is ProWMS Advanced Warehouse Management’s business intelligence module that allows operators or managers to instantly identify where change is necessary and will have the maximum impact. This is done via easy-to-read, live, visual dashboards displaying, for example, products in each location with a detailed breakdown of relevant stock information.
Experienced application vendors will challenge warehouse teams about these and similar issues when they start to discuss the business and operational requirements for new implementations. They will have various tools to help them ensure the configuration is correct and always up-to-date to reflect structural changes, evolving stock profiles, and new business demands to help maximise operational efficiency and profits.
For over 30 years, Principal Logistics Technologies has been a leader in the design and delivery of innovative warehouse management software (WMS) and enterprise resource planning (ERP) software. Its technology and services, which include the design of new revenue-generating services for 3PLs, optimise operational performance, reduce OpEx and increase revenue for 3PL, distribution, wholesale, manufacturing, and retail warehouse businesses.
The company supports enterprise-level and multinational businesses with complex single and multisite operations spanning 3PL, chemicals & hazardous goods, hard & soft commodities, chill picking, cold storage, cross-docking, eCommerce & eFulfilment , FMCG, pharmaceuticals & healthcare and more. It operates from offices in Dublin in Ireland and Manchester and Birmingham in the UK.