Bathroom Supplier Turns on the Taps to Next-Level Digital Tech
2nd September 2019
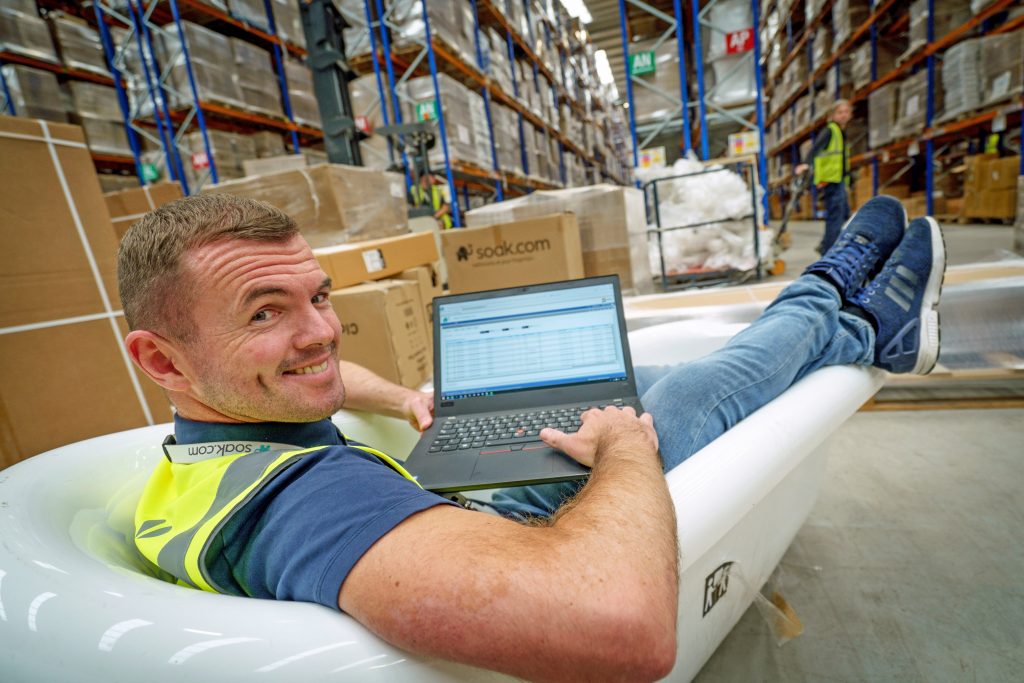
A leading luxury bathroom products e-commerce business has successfully made the transition from pen-and-paper driven warehousing to next-level digital technology.
soak.com distributes through a number of B2C channels to the UK and Ireland (and are now expanding into Europe) but in acquiring a new, customised distribution centre in Liverpool to be nearer the Irish sea ports, they needed a digital solution which could easily be interfaced with its ERP system, implemented quickly, without a large capital investment and able to drive productivity improvements immediately.
SnapFulfil WMS gave the company the competitive pricing and configuring flexibility required to facilitate growth and reduce operating costs, plus the logistical benefits of using a proven solutions provider also helped in what was a massive ‘change management’ undertaking for soak.com.
Return on investment has already seen a 30% reduction in operating costs from digital over paper management, with the cost per item now under 50p, a significant saving.
Additionally, soak.com was able to fit out the purpose-built warehouse and secure all the necessary IT infrastructure and workforce to launch the SnapFulfil WMS solution across all its trading channels in just over three months – which is very quick.
soak.com Programme Manager, Mike Wood, says: “We spent a lot of time upfront defining our requirements and how SnapFulfil would integrate with our ERP order management system, so implementation has gone well – with the majority of our key milestones achieved and with no unexpected time or cost overruns. The SnapFulfil team were great on initial delivery and have maintained that level of quality service with their after sales support.
“We’ve quickly gained more insights into the efficiencies of our business management processes and have been able to react and improve accordingly because SnapFulfil records everything. Stock checks are 99.99% accurate, which has been verified by external practitioners, and the precision of our reporting has been equally impressive.
“We’ve also been able to do enhancement and optimisation work as additional delivery carriers come on board and working closely with the SnapFulfil Continuous Improvement Team means more management data, better understanding and a WMS that keeps giving valuable insight.
“We use temporary order pickers to support peak trading and the system is simple and easy to use as well – in just a couple of hours they can be up-and-running on SnapFulfil – which really helps with our demand peaks.”
Closing the original Nuneaton warehouse – where the company has its HQ – has been a major digital transformation, but soak.com now exceeds 14,000 pallets (previously 12,000) and a catalogue of up to 8,000 SKUs as part of a flourishing business.
Further optimisation of picking procedures and inventory management are the latest ongoing efficiency drivers at Liverpool, which by the end of summer 2019 will have taken up all of Nuneaton’s previous operational capacity.
SnapFulfil Project Manager, Victor Chidlaw, adds: “Soak.com’s product range required various picking methodologies to be deployed to cater for the different storage methods, stillages, extra-large pallets and carton roller options; all of this is managed simply and efficiently within SnapFulfil.”
“Using SnapFulfil has shown the business valuable metrics to make strategic decisions, strengthening the link between the Distribution Centre and the Head Office. Visibility across all channels has enabled resource forecasting for both labour and stock, thus enabling the operation to consistently hit the dispatch deadlines.”
Pic: ‘Soaking’ up all the benefits of best-of-breed SnapFulfil WMS is
Stephen Lea, Senior Systems Support Analyst.