WMS Brings 40% Efficiency Boost to UK 3PL Hallmark
27th February 2020
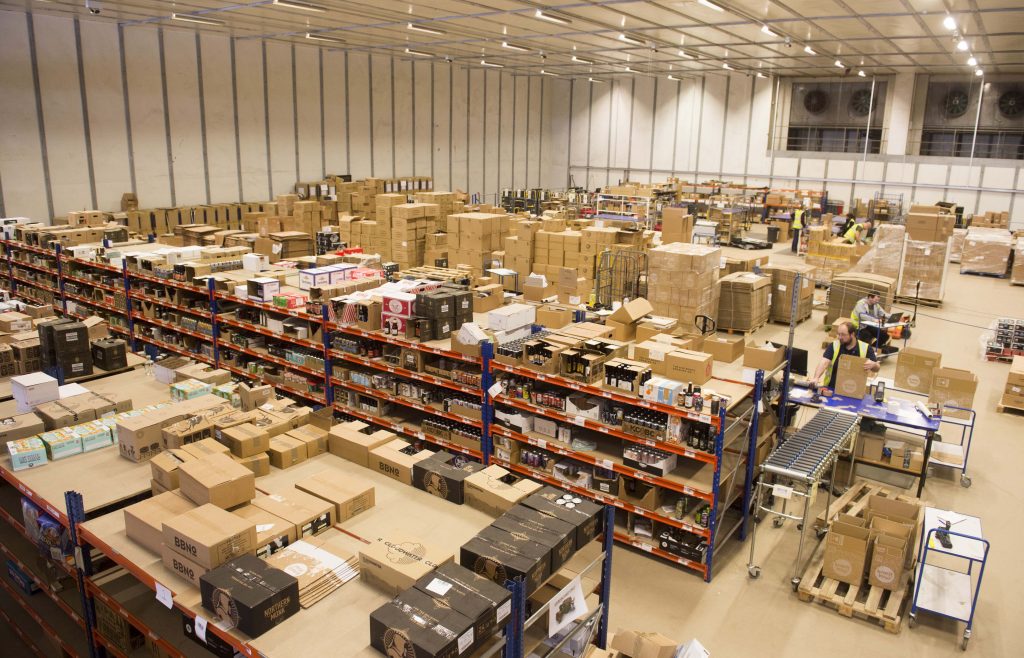
UK 3PL specialist Hallmark Consumer Services says it is enjoying 40% efficiency increases on some of its fulfilment lines after implementing a best-of-breed warehouse management system (WMS).
SnapFulfil WMS is being used across the three levels of Hallmark’s 40,000 sq.ft in Melton Mowbray, Leicestershire, but with 80+ clients and space at a premium needed it to be up and running within a month and working in tandem with the existing OrderActive system.
New and extra functionality software was also required immediately to get products sorted and away a lot quicker and onto different types of pallets in all the correct areas of the warehouse.
Hallmark Consumer Services now benefit from bespoke location formats and walk routes, incorporating their new mezzanine level, while SnapFulfil Pack Station functionality caters for all labelling and streamlines the whole process and makes it more efficient and cost effective.
Coupled with Metapack capabilities, it provides carrier rate shipping to ensure the best value carrier is always used, plus with the many different sized products handled, Snapfulfil volumetric functionality drives pallets to the correct locations to maximise loading occupancy – a process which is continually being honed to optimise slot usage.
Hallmark Consumer Services managing director, Phil Hall, explains: ”We have an entry point system in place, but in taking the business to the next level recently – and coinciding with the new mezzanine floor – realised a much more advanced WMS was required with cloud benefits and architecturally robust, so that the hosted solution performs consistently and reliably in real time.
“We required a lot more set up and configurability options as well – but without being cost prohibitive – and apart from the software being forward thinking and progressive, were looking for a support team we could work in tandem with and on a much more proactive and flexible basis.
“SnapFulfil has delivered in every aspect and aside from these much welcome operational improvements, the transition has been fairly seamless and the support service excellent. We had a dedicated in-house team testing the operating procedures with their project management team, through peak demand periods, and they all remarked how easy the new system was to pick up.
“Minimal training was required on the hand held devices and the shift from onerous manual and paper based procedures to digital automation has been a god send – particularly for goods in – where we’ve been able to tangibly improve labour efficiencies straight away.”
Looking to the future, Hallmark Consumer Services is busy working with the SnapFulfil continuous improvement team on advanced inventory management auditing and making their stock integrity even better.
Multi-tier functionality is also improving the staging areas for pallet drop off across a host of different operators.
With SnapFulfil now starting to be firmly embedded with their clients, the old system is beginning to be phased out and the aim is to use its multi-site capabilities to facilitate additional warehouses.