TPN equips forklifts with rugged tablets
25th November 2021
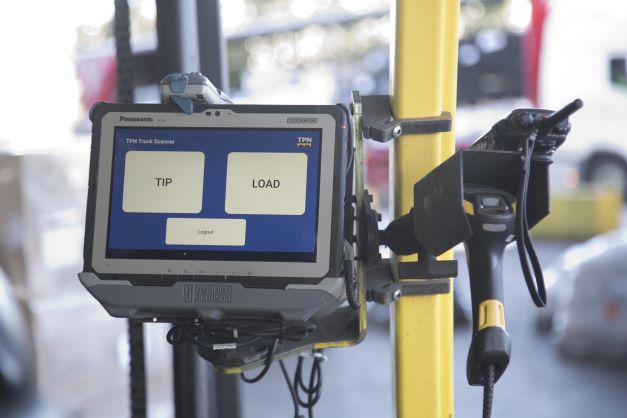
Technology has always played a huge part in staying competitive in the logistics industry, with mobile solutions forming a critical piece across depots, on-site and for managing vehicles. So, when The Pallet Network (TPN) was looking to replace the vehicle-mount mobile devices used by its forklift drivers at the company’s three UK depots it turned to IT services partner Jade Solutions to find the right replacement solution.
TPN is a leading UK pallet freight delivery network, last year shipping 4.6m pallets via its network of 119 regional transport partners and their 130+ depot locations. Their purpose-built main hub is in Sutton Coldfield and is Europe’s biggest cross dock, capable of unloading 57 trailers simultaneously and handling 20,000 pallets a night with workflows optimised using artificial intelligence. Its additional two regional hubs are in Preston and Northampton.
Continuous improvement
For Robert Haigh, IT Director at TPN, the problem was simple: “We had ageing Windows 7 devices mounted in our forklifts that were no longer supported and getting pretty tired. These devices are critical to our operations and used by the drivers constantly, so it was clear that they needed to be modernised. Our customers choose TPN because of our reliability, efficiency and transparency, which helps us deliver a successful logistics distribution service. Together with taking the opportunity to upgrade the old hardware, we also knew we could make further improvements by moving to the latest Android platform and deploying new software for our forklift operators to use.”
Working with trusted IT services partner Jade Solutions, the company set about evaluating options. It looked at all the leading industry providers alongside Panasonic TOUGHBOOK and its rugged Android A3 tablet. TPN required 150 new devices, with 130 deployed on forklifts at any one time.
“The Panasonic device immediately stood out as different,” said Haigh. “It was a much more polished and complete package in terms of design and robustness. In our environment, we knew we needed a tough device, but it’s a bit of minefield selecting a product that is rugged, carries the right features and is future proof enough to last us at least five years. Although we were actively involved in the hardware selection process, we really relied on Jade’s team to help us navigate and choose the right solution for our business.”
The critical factors in choosing the new devices were their ruggedness and reliability in the challenging working environment and the ability to run TPN’s in-house developed software application for managing and moving the pallets. In addition, ease of management and long-term support for the devices were other important considerations.
“We knew that Panasonic TOUGHBOOK devices had a reputation for being rugged to a military-grade but operating on our forklifts they needed to be TPN-grade rugged,” joked Haigh. In the past most damage to the old devices had been caused by the buckles on the seatbelts of the forklifts springing back when unclipped and smashing the device screen.
“We tested the Panasonic device by lassoing the device with the belt and there wasn’t a scratch,” explained Haigh. The TOUGHBOOK A3 is designed to help mobile workers combat the toughest tasks. It is water and dust resistant (IP65) and drop tested to 1.5 metres.
Another important factor in the choice of device was the large 10.5-inch screen and bright outdoor readable display, which enables the drivers to see quickly and easily which pallets must be moved next and where.
The third critical element of the offering was Panasonic’s long-term and regular updates and support for the Android operating system through its COMPASS offering and its ProTect Warranty.
Panasonic COMPASS offers everything TPN needs to configure, deploy and manage their new tablets securely. It’s designed to give organisations the confidence to take advantage of the flexibility offered by the Android operating system with the reassurance that Panasonic’s devices are always business-ready for applications, management and security.
TPN also took advantage of Panasonic’s 5-year ProTect Warranty to provide complete peace of mind throughout the lifecycle of the devices. “When you rely on technology as much as we do in our business, you need to know that your hardware is reliable and that when things go wrong it is going to be taken care of immediately,” said Haigh. “That allows us to concentrate on developing our software and continuing to improve the efficiency of service we offer our customers.”
Lastly, TPN chose SOTI to secure, manage and support their mobile operations after seeing the close working relationship between Panasonic and SOTI partners and how intuitively the SOTI ONE Platform worked with Panasonic devices. SOTI Assist makes it easy and efficient for technicians to analyse, troubleshoot and resolve mobile device and app issues from anywhere, at any time. Rolling out regular application updates to the new devices is also much more efficient using SOTI MobiControl.
“Reducing downtime is critical for us,” explained Haigh. “Using SOTI as the deployment tool, we have updated our software four or five times with tweaks and improvements and it’s very simple. As soon as we decide to deploy the update, it is on the devices in minutes.
“In addition, we have never had visibility of our mobile assets in the past. Now we can log on and see exactly what’s happening with each device. It’s easy remote management, visibility and control. For example, we can see if a device battery is running low, or if the device hasn’t been switched on properly.”
Positive feedback
The new forklift devices have been positively received by the drivers. “The feedback has been really positive,” said Haigh. “They immediately noticed how quickly the new devices work and that the connectivity is much better than with the old devices. There are practically no connectivity blackspots any longer, which has really saved us time and increased the productivity of our drivers.
“Importantly, we also didn’t need to spend any time or money to train the drivers to use the devices. It is all very intuitive. They just went to the forklifts and started using the new solution straight away.”
Having a true partnership approach to tackling the problem was equally as important to the TPN team, as Haigh confirmed: “Because the deployment of technology is so important to our business, we can be quite particular about what we want and sometimes even come across as a bit stubborn, but I was impressed with the pragmatism and support offered by Jade and Panasonic from day one. It really felt like a three-way partnership where we were all going to benefit from getting it right.
“We want to work with organisations that are creative with their solutions, deliver on their promises and that go above and beyond to meet our needs. I can say without doubt that Jade Solutions do that.”
Moving forward, TPN plans to extend the use of the devices for additional purposes at the hub, by undocking the devices from the forklifts and using them for supervisor checks, yard management and door control.
“Ultimately, we now have a solution that is ideal for our working environment and that we can rely upon to do the job, allowing us to concentrate on delivering and fast, transparent and competitive service to our customers,” concluded Haigh.