ARIBIC digitalisation project saves AGV sensor data
1st September 2021
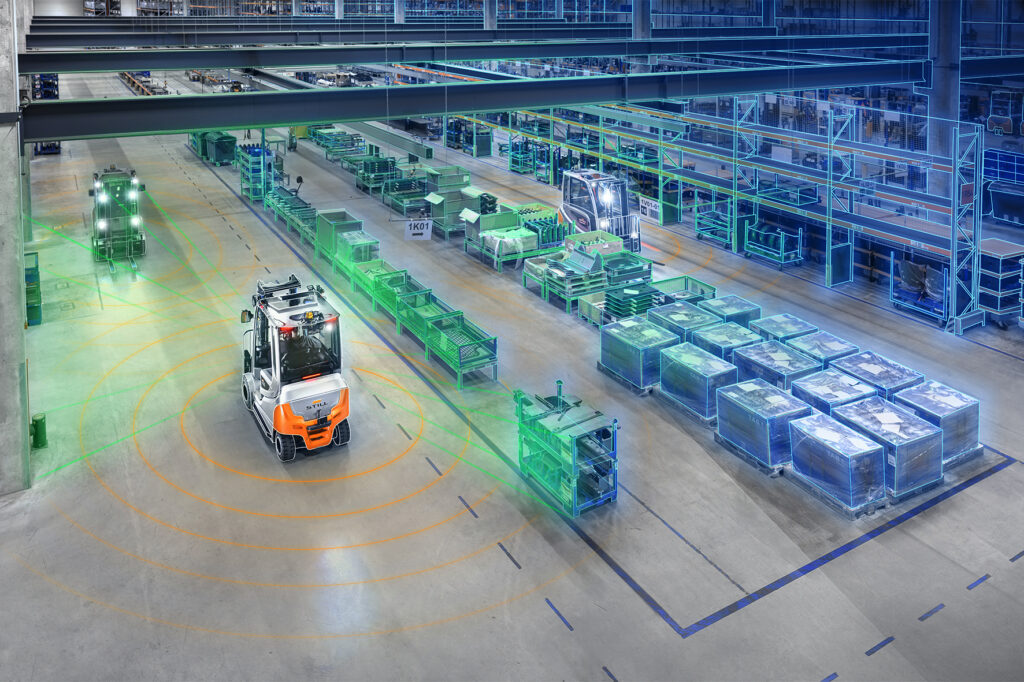
As automated guided vehicles (AGVs) navigate through warehouses or production halls, they become real data collectors. Data that is, however, immediately deleted again. “This is a huge waste,” says Bengt Abel, project manager at Hamburg-based intralogistics provider STILL. The international research project ARIBIC (Artificial Intelligence based Indoor Cartography) therefore aims to identify methods to make profitable use of this valuable information.
The data collected via sensors and cameras can be used in the ARIBIC cloud to create continuously updated 3D maps of warehouses or production facilities. “Via this real-time sensor data, we create a live digital twin of the environment and can thus display and share relevant information virtually in real time,” says Bengt Abel, describing the basic idea of the research project. In contrast to today’s method, where a rigid 3D image of the environment is created from a snapshot, the images generated by the ARIBIC platform (3D map creation engine) remain dynamic and always up-to-date.
“As the truck or AGV travels through their surroundings, their sensor technology detects even the smallest changes and forwards them to the ARIBIC platform. These changes, such as a moved rack or a newly placed pallet, are immediately taken into account in the artificial intelligence-based interior mapping and fed back into the system,” says the STILL expert.
Enormous benefits for users
High-resolution 3D maps with semantic information are primarily needed for the localisation and navigation of automated guided vehicles in their working environment. Operators of warehouses or production halls thus know where their vehicles are at all times. This information, in turn, can be used to optimise warehouse or factory planning. For example, it becomes clear in which areas of the warehouse traffic is high or low. It also shows which aisles are more frequently blocked. With these results, racks can (initially) be moved virtually or production areas rearranged.
Bengt Abel: ” With this new possibility to permanently record the working environment, operators will be able to optimally plan and utilise their warehouses and production halls in the future. For the first time, they would get a detailed insight into what is actually happening in their warehouses.”
According to the STILL expert, countless other fields of application are conceivable that build on the ARIBIC results: “We already have great ideas today. But I am quite sure that there will be a great many more in the future.”
The ARIBIC project
The ARIBIC project was launched in March this year. Completion is planned for the fourth quarter of 2023. In addition to the consortium leader STILL, the Karlsruhe Institute of Technology (KIT), the University of Toronto with its STARS laboratory and the Canadian sensor manufacturer LeddarTech are also involved in the international research project. The project is funded by the German Federal Ministry for Economic Affairs and Energy (BMWi) and the National Research Council of Canada Industrial Research Assistance Program (NRC IRAP).
STILL will also be contributing the OPX iGo neo, their successful autonomous order picker, which is already well equipped with sensors and camera technology. Yet that is not all, as Bengt Abel emphasises: “Our early commitment to the areas of automation technology, robotics and digitalisation is now paying off. For years we have already been working on a variety of sensor solutions for our industrial trucks, which are now gradually being implemented in series production. An important prerequisite for being able to participate in such a project in the first place.”