BlueBotics Celebrates 10 Years of ANT Vehicle Ops
23rd October 2019
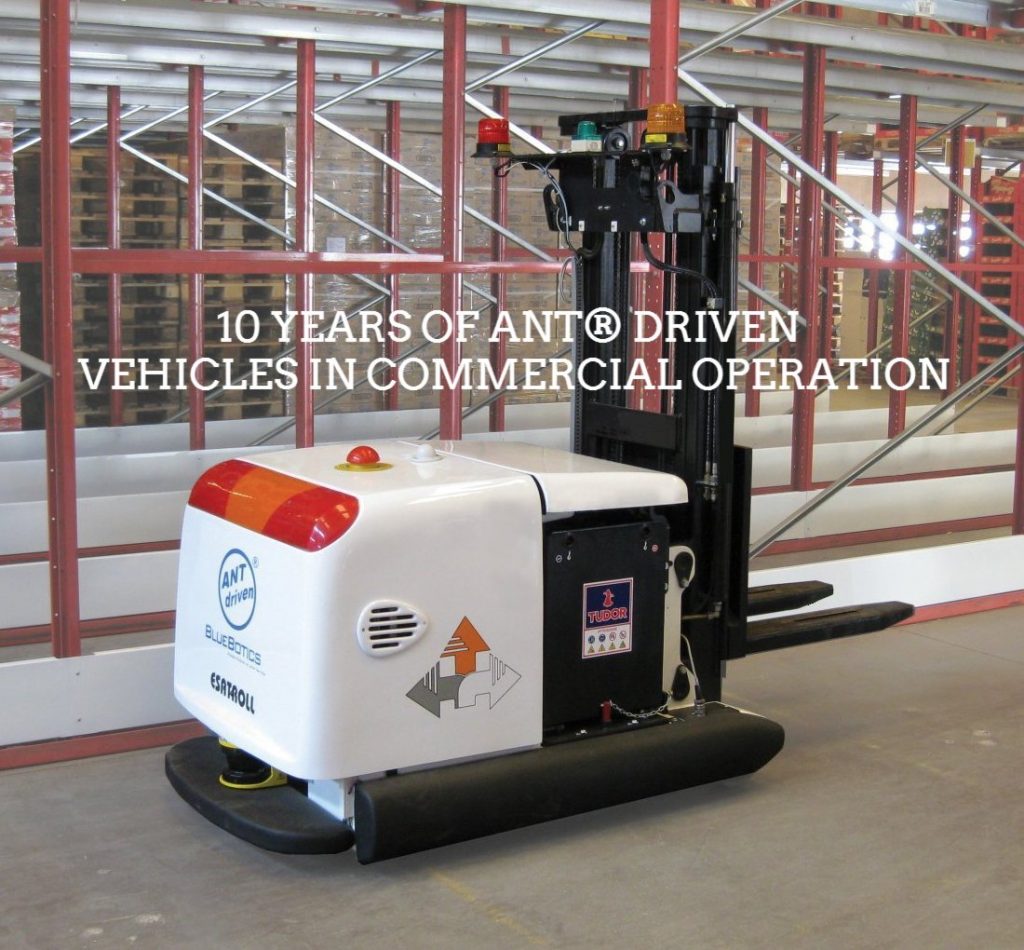
AGV and AMR specialist BlueBotics, is celebrating ten years since the first vehicle driven by its Autonomous Navigation Technology (ANT®) went into commercial operation. The company has also announced its ANT® lite+ and ANT® localisation+ products’ new support for omnidirectional vehicle movements.
The first ANT® driven vehicle to go into commercial operation was an Esatroll general-purpose Paquito AGV. This was installed at Dal Colle (Barilla Group) in Italy in 2009. Since then, as of October 2019, over 1,750 ANT® driven industrial vehicles have been commissioned at sites around the world. These installations span five continents and numerous commercial applications, ranging from shop floors and warehouses to cleanrooms, hospitals and data centers.
“A primary reason for our success is the robustness of our ANT® navigation solution. As customers often tell us when choosing to partner with BlueBotics, the platform just works,” said the CEO of BlueBotics, Nicola Tomatis. “AGV makers also appreciate the close, professional integration support we offer. This is crucial to the success of a project, whether a customer is developing a brand new AGV, upgrading an existing AGV’s navigation or automating a manual vehicle.”
Also driving the company’s continuing growth, Tomatis adds, is the fact that BlueBotics’ guidance technology suits virtually every type of AGV, environment and application: “We have modules such as ANT® lite+ integrated in 100 kilogram AMRs for cleanroom applications, while other customers are using ANT® to guide huge vehicles that regularly move loads of 25 tons or more.”
Omnidirectional movement
BlueBotics also announces today its ANT® platform’s newly-expanded support for omnidirectional vehicle movements. Previously available within the company’s ANT® localization solution, omnidirectional movement is now supported by BlueBotics’ entire range of navigation products, including ANT® lite+ and ANT® localization+.
“In most cases our customers develop vehicles based on tricycle or differential drive kinematics. For these models, ANT® lite+ is typically the optimal solution,” Tomatis explains. “However, there are exceptions—sites where omnidirectional movement makes all the difference—such as ultra-complex environments or older sites that cannot easily be optimized for AGV use. That’s why, as always, we’ve listened closely to our customers and expanded our platform’s omnidirectional support. With the latest version of our ANT software, manufacturers can reap all of the space-saving benefits that omnidirectional AGVs can bring, programming these movements simply and efficiently at the click of a button.”