Bridging the gap between Indoor and Outdoor Logistics
20th June 2024
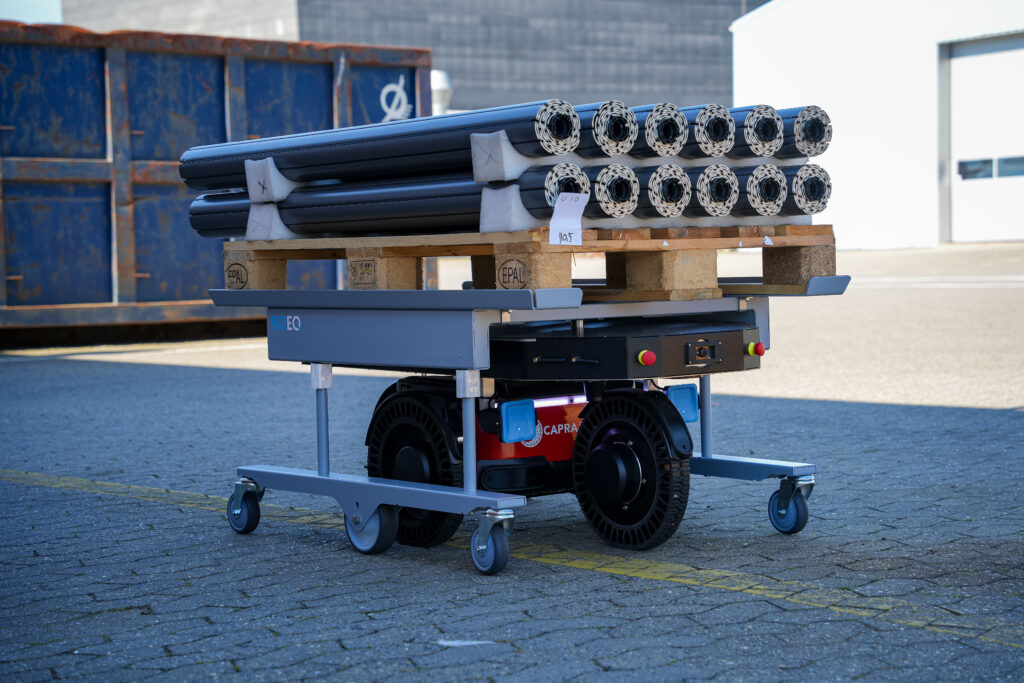
Award winning company Capra Robotics have invented a new solution for achieving smooth and uninterrupted logistics flows facility wide, indoor and outdoor.
For decades, manufacturing companies have invested heavily in optimizing their intralogistics to ensure the smooth flow of materials within their facilities. However, a critical bottleneck arises when moving goods out of one production building and into the next. The transition from indoor to outdoor logistics presents a unique set of challenges for AMRs and AGVs such as crossing the gate, shifting weather conditions, and uneven terrain which results in additional and undesired manual handling. Unfortunately, manual processes place companies at increased risk of errors, increased operational costs, and worst: interrupted value chains.
The heavy reliance on labour puts companies at risk due to historically low unemployment rates and increased labour costs. To stay competitive, scale their business, and maintain conformity to existing process standards, companies need new automated and digitized solutions for a wide range of tasks – and in new domains. To this end, CAPRA ROBOTICS® has emerged as a transformative force in logistics and recently won an RBR50 Innovation Award for its logistics solution.
Bottleneck of Logistics
Whereas intralogistics refers to optimizing and managing the logistical flow of data on and physical material within a facility, CAPRA ROBOTICS® proposes a new concept to describe the process of moving goods across entire facilities in uninterrupted logistics flows: Interlogistics. Interlogistics involves the transfer of goods from the well-controlled indoor environment of a facility to the more unpredictable outside environment with various challenges such as weather conditions, heavy traffic, and challenging terrain when moving goods between buildings.
Because the two environments are worlds apart when it comes to classic automation, this transition is often accompanied by manual processes, which introduce various complications. Manually moving material between production buildings with forklifts increases the risks of errors, damage, and increased operational costs. A lack of real-time tracking contributes to extended lead times while additional labour, storage, and the need for error rectification all contribute to higher costs. Now, however, there is an alternative.
To bridge the gap between indoor and outdoor logistics effectively, businesses must take a holistic approach. The goal is to bring the same level of automation, efficiency, and accuracy that characterizes intralogistics into the realm of interlogistics. While a strategic shift in mindset is a necessity, it requires the appropriate technology. CAPRA ROBOTICS® has created an AMR solution that unifies indoor and outdoor logistics operations by being able to move goods between production units in separate buildings. The unique-looking mobile robot, CAPRA CARRIER, utilizes the latest advances in vision- and AI-based mapping as well as satellite-based positioning to enable both indoor and outdoor navigation.
The solution integrates sophisticated indoor and outdoor navigation systems seamlessly. Indoors, it utilizes an AI-powered VSLAM system alongside PLd-rated industrial radars, facilitating rapid mapping and updating for operation in confined environments. Outdoors, a proprietary Kalman Filter processes data from GNSS signals, Odometry, and IMUs, enabling automatic navigation system switching as the environment changes. This dual navigation system ensures uninterrupted logistics flows across entire facilities.
Uninterrupted Logistics Flows
Automated pick-up and drop-off paired with wireless opportunity charging reduce the need for human intervention, allowing clients to utilize their personnel for tasks that truly require human capabilities and add value. Courtesy of the novel VSLAM system and high-precision docking, the robot supports automated loading and unloading of SLCs, racks, pallets, and customer-specific packaging. The solution has a documented uptime of more than 10 hours and features automated charging, contributing to minimal downtime in operations.
Flexible Payloads
The AMR is designed with advanced material handling capabilities, allowing it to handle a wide range of goods and materials with ease. The system is designed with the flexibility to handle standard load carriers as well as customer- and industry-specific packaging. In effect, the solution supports top deck loads of up to 100 kg., in addition to carts and trailers with a payload of up to 500 kg. Due to its modularity and versatility, a single AMR can reduce the need for manual labour and forklift operations leading to significant increases in productivity and substantial reductions in production costs leading to a payback period as low as 12 months. In addition to being a good financial investment, implementing automation will help companies achieve their long-term business targets as they try to accommodate for growing labor shortage issues.
Interoperability
The solution is accompanied by a universal fleet management system, designed for interoperability and combined indoor-outdoor operations. Tasks generated in a central management system (WMS/MES/ERP) are communicated to the robot via the VDA5050-compliant CAPRA FLEET MANAGER interface. The Fleet controls the overall operation and performance of the robots, monitors the progress and status of its subsystems, and communicates with external systems such as gate controls, light controls, and crossing signals.
The robot and its navigation system have an IP65 rating and are designed to operate in varying climate conditions and effortlessly navigate in strong sunlight, precipitation, low light, and uneven terrain. This allows it to move goods safely and efficiently through even the most challenging and dynamic environments. The combined system is extensively tested and safe for use in busy industrial environments, with multiple safety protocols and features built into the design. The robot features state-of-the-art PLd-certified radar sensors, the most dependable safety sensor for combined indoor and outdoor driving. The radars work in any weather and lighting conditions, can measure several objects simultaneously, and have a response time of less than 100ms for optimal safety.
The transition from intralogistics to interlogistics is a pivotal point in the supply chain that can no longer be ignored. Manually handling goods in and out of production buildings compromises cost-effectiveness and hinders uninterrupted logistics flows. Businesses must adopt a holistic approach to bridge the gap between indoor and outdoor logistics. This approach, which focuses on digital data management, real-time tracking, automated workflow, and data integration, paves the way for a new era of efficiency in logistics, facility-wide.
The future of logistics lies in the seamless flow of goods, information, and automation from before they enter the facility to after they leave. As businesses embrace this holistic approach, they will find themselves better equipped to navigate the challenges of production logistics, leaving behind the errors, inefficiencies, and operational costs that have plagued the past.
read more