Dutch Paper Mill Completes Partial Automation with Seven Counterbalanced AGVs
14th November 2017
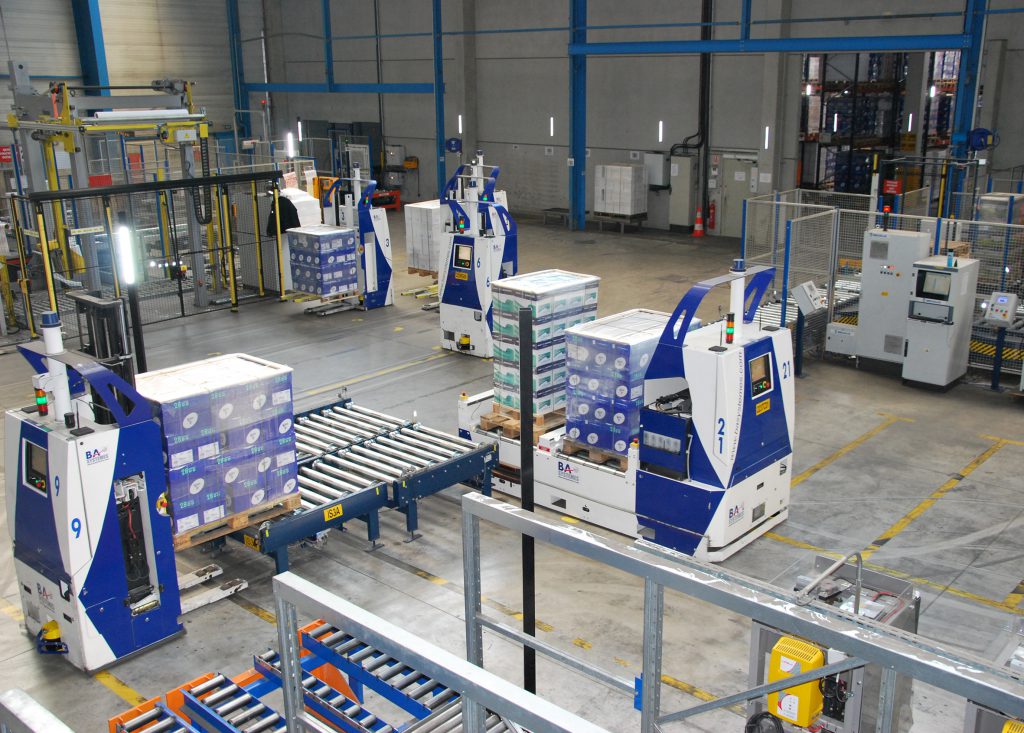
BA Systèmes, the French leader in AGV-based intralogistics systems has successfully completed the partial automation of Sappi’s Maastricht paper mill in the Netherlands. The fleet of 7 counterbalanced AGVs constitutes a highly efficient automated solution for integrated production and storage flows.
Sappi is a South African global player in the paper industry headquartered in Johannesburg, with nearly 12,000 employees in over 20 countries on three continents. Headquartered in Brussels, Sappi Europe is the leading European producer of coated fine paper used in premium magazines, books and high-end print advertising. Located on a 14-ha site, Sappi’s paper mill in Maastricht employs 480 people and produces 290,000 tons of coated wood-free paper per year. Thanks to its central location in Europe, the Sappi paper mill can deliver its products quickly and efficiently throughout Western Europe.
In order to increase the efficiency of the internal logistics in the cutting and packaging areas of the plant, Sappi decided to optimize internal transport by means of a fully automated AGV system.
Sappi has trusted BA Systèmes and its long experience in AGV automation as well as on its knowledge of the paper industry to provide its Maastricht paper mill with a safe, reliable and efficient AGV system that combines excellent functionality with a significant increase in productivity.
Completely integrated into the production process and operating 24 /7, the AGV solution offers:
– The transport of paper from the 3 cutting machines to the buffer storage
– The logistic management and handling in the buffer storage
– The transport of paper from the buffer storage to the ream wrappers.
BA Systèmes has integrated the system into the heart of Sappi’s production process, comprising 7 AGVs, an automatic battery changing system (Autoswap), and the AGVs’ traffic management through AGV Manager, BA Systèmes’ supervision system. The contract also included the supply of pallet racking systems and the connection to existing and new conveyor systems.
Sappi relied on BA Systèmes’ expertise to ensure the quality, overall efficiency and reliability of the system. One of the main concerns was to avoid any damage to the palletized paper sheets, a very delicate load. To ensure the integrity of the loads during transport, BA Systèmes has been working with Sappi from the start to adapt the AGVs to their specific needs and develop new tailor-made tools.
At Sappi, there are nearly thirty different pallet dimensions, and some of them are quite unstable due to the unwrapped stacks of paper. BA Systèmes’ AGVs developed for Sappi have undergone extensive tests to guarantee safe handling of these various formats. A set of specific tools has been added to the AGV equipment:
– A load backrest to maintain the integrity of the stacks during emergency braking
– A special pressing device to improve the stability of the paper stack during pick-up, transportation
and drop-off, avoiding paper stack deformation and loss of individual paper sheets
– A wide-range fork width control system to ensure safe handling from the smallest to the largest load
– A fork board sideshift to minimize the load spacing in the racks and optimize the storage capacity.
If needed, one or more AGVs can be transferred from one area to another by a simple keyboard order from an operator.
NB: The picture shows a similar BA Systemes installation.