Robotics Help Philips Factory Logistics
14th March 2025
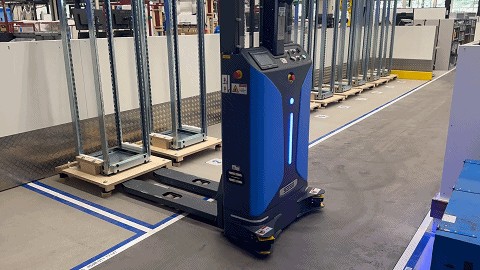
Recently, in order to accelerate the automation and digitization of warehouse racking transfer, and to reduce the manual handling workload, Philips Netherlands factory has introduced the CE-certified forklift SFL-CDD14-CE , which not only reduces the intensity of manual work but also eliminates the safety hazards in the operation area, and significantly improves the overall transfer efficiency of the warehouse.
Philips site needs and challenges
In Philips factory operations, the transfer of racks between the warehouse and the production area faces a number of challenges and needs:
– Automate and digitize the transfer: Traditional methods of transferring racks in the warehouse rely on manual handling, which is inefficient and error – prone. Philips wanted to introduce an automated solution to enhance logistics efficiency and management.
– Reduce manual handling workload: The shelves are high and heavy, making manual handling very intense. This can easily lead to employee fatigue and workplace accidents. Therefore, there was a need for equipment to replace manual handling.
– Ensure the safety of shelf transfer process: There are potential safety hazards during shelf transfer, such as tipping and collision. Effective safety measures are needed to ensure the safety of personnel and equipment.
– Flexible adaptation to production needs: Production plans may change at any time. The shelf transfer program needs to be able to quickly respond to production changes to achieve flexible scheduling and efficient operations.
Highlights of the Solution
– CE-Certified, Ideal for Overseas Markets
SEER ROBOTICS offers various types of CE-certified autonomous forklifts. The products are internally equipped with SEER ROBOTICS’ Safety Controller for Autonomous Forklift SRC-3000FS. The SFL-CDD14-CE product selected by Philips has CE and UL certifications and has passed the ISO3691-4 certification, enabling worry-free export to the European market.
– Rotational Charging, More Flexible and Efficient
According to the area division at the Philips site, the charging area for autonomous forklifts is relatively narrow. To solve this problem, SEER ROBOTICS has set up a ‘rotational charging’ mode. The forklifts operating on site are charged in sequence, achieving an even distribution of power and avoiding power depletion situations. Based on this, it not only improves the charging efficiency and extends the service life of forklifts but also reduces energy waste.
– Multiple Measures, Ensured Safety
The SFL-CDD14-CE has extremely high safety attributes. The fuselage is equipped with 3D obstacle-avoidance cameras, distance sensors, etc., achieving 360-degree three-dimensional safety protection. According to the on-site environment, SEER ROBOTICS has set the optimal forklift operation routes, working hours, and pallet placement positions, and has finely adjusted the forklift identification parameters and safety parameters to achieve both safety and efficiency. In addition, a specific safety area is set up. In case of an unexpected situation, it supports a one-click arrangement for forklifts to go to the designated area.
similar news