Case Study: Smart Production Solution from KNAPP
26th November 2018
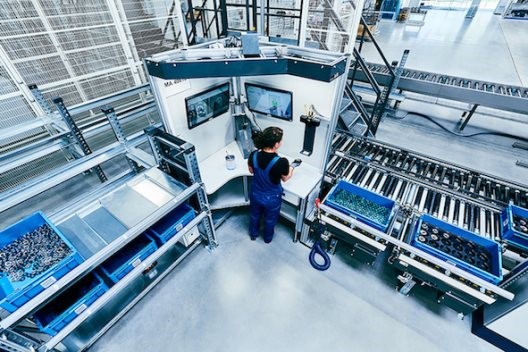
At its new factory in Kapfenberg, Austria, Pankl High Performance Systems will produce 160,000 drivetrains a year for leading motorcycle and sports car manufacturer, KTM. Pankl is using automation from KNAPP for just-in-time supply of components to its assembly workstations, where KNAPP software ensures real-time quality control.
Production and assembly of high-grade motorcycle drivetrains began at the 9,000m² Kapfenberg site in the autumn of 2017, creating 110 new jobs. Seeking a balance of automated and manual processes, Pankl High Performance Systems – a new division of Pankl Racing AG – chose an intelligent material handling solution from KNAPP that epitomizes the logistics provider’s zero-defect philosophy.
A drivetrain every three minutes
With a production volume of 160,000 drivetrains per year, automation was key to Pankl’s success but the solution also needed to offer sufficient flexibility to respond quickly to various changes in production. At the Kapfenberg site, Pankl manufactures a total of nine different drivetrains for KTM for offroad use and will produce at least 3 models for road vehicles in the future. In the world of performance motor sport, the quality of components such as drivetrains is paramount, requiring seamless traceability for every step of the production process.
Shuttle store supplies components just-in-time
KNAPP supplied an automated shuttle store to link the production and assembly processes. Following manufacture, the components are washed and then stored by the shuttles, which subsequently retrieve all the required components and supply them automatically and just-in-time directly to the assembly workstations. At each assembly station, support for operators in assembling the drivetrains is provided by the intelligent feedback system, ivii.smartdesk. Developed by ivii gmbh, the image recognition and processing specialist within the KNAPP group, the ivii.smartdesk captures information regarding every component and checks every work step. In this way, each drivetrain is inspected in real time to confirm the correct assembly, with personnel receiving immediate and motivational feedback on their work. KNAPP’s scope of supply was completed with its integrated software solution, KiSoft One. A video of the solution supplied to Pankl is available here.
Commented Michael Mayer, Plant Manager for Pankl High Performance Systems, “The process is set up so that our fitters are optimally supported and the right component is always available at the right time at the workstation. The entire process is supported by software to the greatest possible extent,” he continued, “where each step of work is displayed on the monitors and checked in the background. We therefore create an ideal working environment in which our employees can concentrate entirely on the assembly of the drivetrains.”