Cost-Efficient Logistics Drives in Three Preferred Configurations
15th November 2017
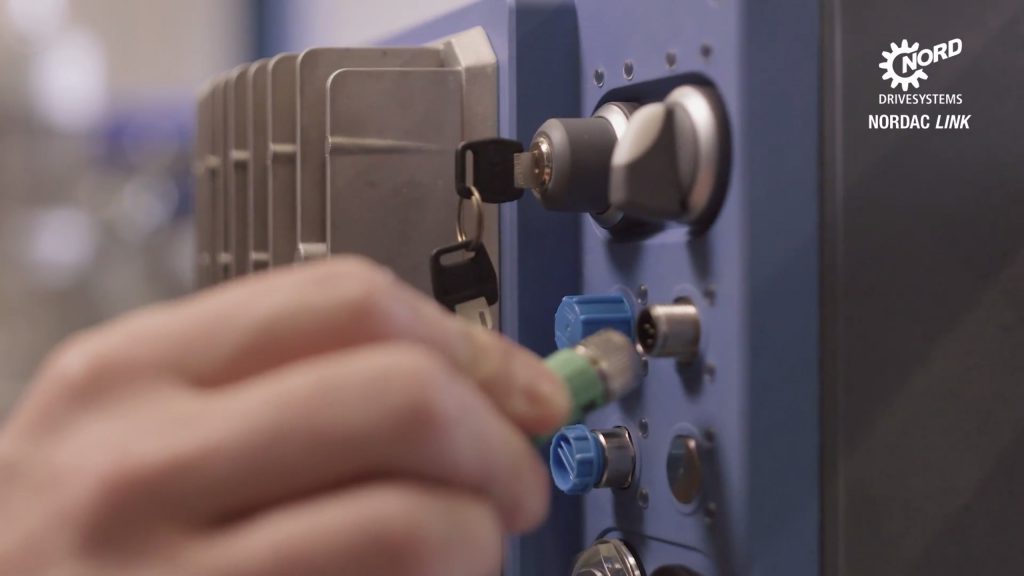
In plants with many drive units, the total cost of ownership can be reduced by up to 70% through intelligent management of variants. Therefore, NORD DRIVESYSTEMS has established three preferred sizes for efficient variable-frequency drives in materials handling and conveyor applications. These cover the typical functional and performance requirements in postal hubs, intralogistics applications, and baggage handling systems. The standardized drive systems greatly simplify purchasing, engineering, commissioning, and spare parts stocking. Moreover, they are particularly easy to install, operate, and maintain.
Limiting the number of variants can yield greater total cost of ownership (TCO) savings than any other measure except for lowering energy consumption. Therefore, drive manufacturers should be able to provide viable drive system standardizations for specific industrial segments. Preferred variants will also benefit customers by simplifying the procurement process, from the first drive purchase to any orders that may follow. Fewer variants also make inventory management much easier. Furthermore, they make planning and engineering processes less complex for everyone – the drive supplier, the OEM, and the end user. The challenge is to select as few drive configurations as possible in such a way that they adequately fulfill the varied tasks without being oversized. Drive engineers therefore need to thoroughly analyze sector-specific patterns of drive operation and application-specific needs. NORD DRIVESYSTEMS has been designing efficient drive technology for intralogistics and airports for many years. Based on this wealth of experience, the German manufacturer has developed the LogiDrive line of three preferred drive variants optimized for these applications. LogiDrive systems ensure leaner purchasing, engineering, system maintenance, and staff training processes. Only very few spare parts must be kept in stock. As a result, the TCO in postal hubs, warehouses, and baggage handling systems can be reduced by up to 70%.
Three variants, much flexibility
The LogiDrive line is the solution for conveyor systems spanning many hundred meters. The variable-frequency drives (VFDs) allow for simple daisy-chaining; short power lines can be connected from one drive to the next. NORD has tailored this line to intralogistics and airport technology. Three geared motor variants meet all typical performance requirements. IE4 permanent-magnet synchronous motors with power ratings of 1.1 kW, 1.5 kW, or 2.2 kW are combined with efficient two-stage helical-bevel gearboxes in two sizes for torques up to 260 Nm. Robust frequency inverters from the NORDAC LINK series enable a wide range of speeds. The systems feature a high overload capacity and offer a uniquely versatile range of functions. Interfaces for all commercially available communication protocols are available, including PROFINET, Ethernet POWERLINK, EtherCAT, and EtherNet/IP.
Extremely user-friendly and efficient
LogiDrive systems are easy, quick, and safe to install thanks to coded plug-in connectors. Maintenance switches, key switches, and direction switches on the devices allow for flexible direct access to individual drive axes for setup or service. Sensors and actuators can be connected via M12 plugs. Sensor data collected by the inverters can be passed on to higher-level systems, which reduces otherwise necessary wiring. Plug & play, pre-parameterized inverters also simplify maintenance. Drive components can be easily replaced. Instead of swapping out entire drive units, for instance, only the geared motor can be exchanged. Thanks to their light-alloy housings, the compact drives are easy to handle as well: on average, they are about 25% lighter than steel-alloy drives. The LogiDrive systems’ IE4 or Super Premium Efficiency synchronous motors take their energy-saving potential to its full extent in conveying systems with frequent partial-load operation. By consuming significantly less energy, they pay for themselves in a very short time.
Integrated safety
LogiDrive systems efficiently and safely power horizontal, inclined, and vertical conveyors. A load monitor protects the driven equipment by stopping the motor in case of blocked applications. NORD can even implement the STO and SS1 safety functions according to EN 61800-5-2 for every single drive axis by means of TÜV-certified electronic modules. Employing field-oriented vector control, the inverters achieve high-precision control. In hoist applications, for example, they provide full torque from zero speed and reliably deliver set speeds even under load fluctuations. Standard inverter features furthermore include connection options for incremental and absolute encoders. The drives manage absolute and relative positioning as well as smart braking. Positions and distances can be programmed via the bus or directly on the device. Multiple drives in master/slave operation can synchronize speeds or positions. Featuring integrated PLC as well as PI controller functions and a wide range of sensor interfaces, these systems can even be used to drive fully autonomous modular equipment in a larger installation.
NORD DRIVESYSTEMS has extensive practical experience in the field of conveyor technology. The drive manufacturer has designed efficient drive systems for hundreds of intralogistics plants and airports worldwide. The company draws on a large modular program of drive components that are manufactured in-house. The energy-saving motors are suitable for worldwide use and available in all common efficiency classes. The NORD gear portfolio comprises numerous gear types and covers an extremely wide range of torques and gear ratios. The VFDs provide enhanced intelligence in plant segments and ensure high efficiency especially in partial-load operation. Furthermore, electronic inverters enable highly flexible speed adjustment. This allows for limiting the drive variants in a larger installation to only a few sizes and gear ratios. The new LogiDrive systems for airport and other logistics applications demonstrate the benefits of greatly simplified variant management and the major cost savings associated with it.