Egemin To Build Third High-Bay Warehouse For DeepFreeze Specialist
21st November 2016
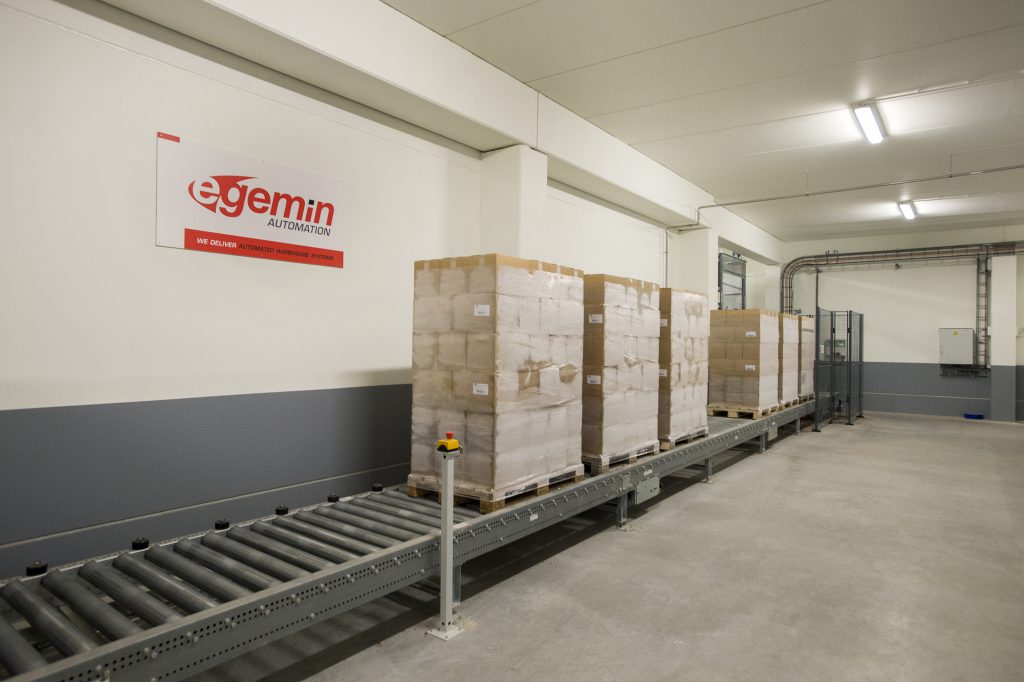
Belgian pre-fried and frozen potato products manufacturer Agristo is teaming up with Egemin Automation for the third time in a row for the construction of a new, fully automated high-bay deepfreeze warehouse. The new warehouse will be built in Wielsbeke (90km west of Brussels) on a 25-hectare lot. Alongside the storage facilities, Agristo is also erecting new production buildings and green zones. The investment needs to support extra production capacity, further improve Agristo’s quality insurance and expand the company’s storage capacity.
Work started on the new site at the beginning of September. The warehouse will be nearly 45 metres high, and with 15 storage levels it will accommodate 50,000 pallets, or 35,000 tons of frozen fries. The warehouse is due to go into operation in autumn 2017. Agristo already has two Egemin high-bay warehouses in use, in Tilburg (2012) and Nazareth (2015).
Egemin is handling the complete intralogistics infrastructure and the automation of the warehouse operations. It is providing the warehouse racks for the clad rack structure, as well as the pallet stacker cranes, the conveyor system and pallet lifts that connect production and shipping with the high-bay warehouse. Agristo will use Egemin’s E’wms software for automatic control and management of its new warehouse and all transport systems.
“Automation means that it is easier for Agristo to guarantee the quality of its products,” says Marcel Spruijt, Sales Manager at Egemin. “The cold chain is never interrupted even for a moment. The pallet conveyor system automatically conveys the frozen fries from production to the high-bay warehouse. In addition, fewer actions are needed to move products to the warehouse, which reduces the risk of damage to the pallets and packaging.” The high-performance warehouse concept has a double outfeed conveyor system on two levels. This means that Agristo can handle large buffers very quickly making it possible to load trucks from the warehouse in barely 15-20 minutes.
The clad rack structure of the deepfreeze warehouse is designed to use energy sustainably. “The production and storage of frozen fries takes a lot of energy,” says Carmen Wallays, Procurement & Logistics Director at Agristo. “When designing this new project with Egemin, we therefore paid a lot of attention to efficiency, sustainability and the environment.”
As a result, the roof and wall insulation is thicker than the standard for deepfreeze warehouses. The pallet stacker cranes have an internal energy recovery system. The system collects the energy released during lowering and braking operations of the cranes and feeds the energy back into the power grid. In this way, the cranes save up to 20% energy, less heat is released into the warehouse and less cooling is required.