New Palletising System offers Speed and Simplicity
5th October 2020
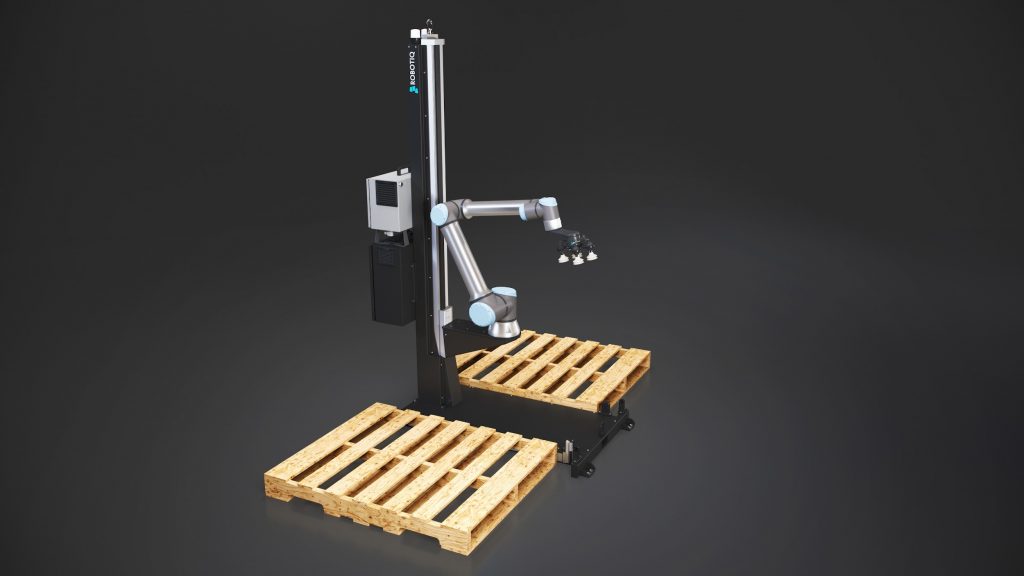
A new robotic palletising solution which combines flexibility and ease of set-up with greater throughput for rapid return on investment, has been introduced by collaborative robot (cobot) application specialist Robotiq.
The Robotiq Palletising Solution has been specifically developed to meet the needs of companies providing essential goods in lower throughput applications with frequent changes of task and box or pallet size.
Around 30% faster than other cobot palletisers currently on the market, the new system is designed for applications of up to 13 boxes/ minute. Installable in less than a day thanks to its single, integrated application software, this solution can be set-up for a new SKU in as little as five minutes.
In addition, this application-focused technology comprises fully connected, plug and play hardware and software with pre-selected functions for rapid and simple deployment with UR10.
“We were very impressed when testing this Application Kit. The synchronised motion makes it a very unique product in the cobot space,” said Early Ewing, Head of UR+ Ecosystem at Universal Robots.
The palletising application can be set up in just three simple steps on the visual robot control device, with automatic trajectory planning and collision detection, and no need for a PC or external programming. Once programmed, simple one-click activation gets operations under way immediately.
The system delivers optimised, synchronised motion control of both the cobot and 7th axis, with seamless movements ensuring a maximised cobot life cycle. Its compact footprint means it fits easily within any existing floor layout, with no need to reconfigure production.
Each system consists of a vertical axis, a robot base, an application software and a vacuum gripper. In details: vertical 7th axis and control box containing PLC, drive, motor and safety relay; Robotiq’s vacuum gripper AirPick, bracket and suction cups; pallet and box sensors; cable management system; URCaps nodes for palletiser and axis control; and two status lights.
The technology has undergone extensive and robust field testing, receiving strong endorsements from leading robotics experts. Among them is Bryant Henderson, senior robotics engineer at Advanced Control Solutions, who commented: “Overall I was extremely impressed with the system. The hardware seems tested and robust, and the user interface is extremely easy to use.”
Nicolas Lauzier, senior product owner at Robotiq, explained: “The need to automate the palletising process – already a key consideration in many facilities due to the health & safety implications of repetitive and physically demanding manual palletising on human operatives – has only been intensified by the recent Covid-19 pandemic.
“However, many other cobot palletising solutions on the market have a large footprint, are comparatively high in cost and require substantial expertise in automation, while the time needed for programming can be significant. There are also challenges around the flexibility of these systems for different applications – for example, handling smaller boxes or using pallets of different sizes – and their speed, which rarely exceeds 10 boxes/ minute. The issue is often further complicated by the use of components from multiple providers, leading to compatibility issues.
“The new Palletising Solution by Robotiq is addressing all of these issues at once, providing a flexible and rapid solution particularly suited to the food & beverage, consumer product and pharmaceutical sectors – or any other sector requiring rapid throughput and SKU changeover.”
Additional customer value is provided through risk assessment recommendations comprising an e-learning module on safety and a dedicated section on safety in the instruction manual. It is also compatible with third party safety systems such as safety interlocks, light curtains and area scanners.