BS Handling Systems Takes On Big Retail Project For Clipper Logistics
9th November 2016
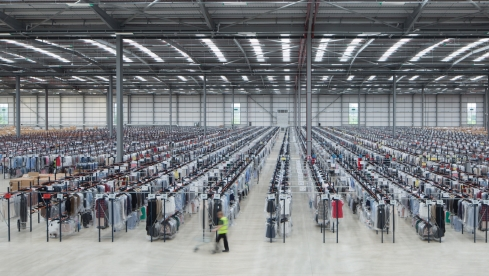
When Clipper Logistics plc was awarded a new e-fulfilment contract with a major international retailer, it turned to BS Handling Systems to fit out its new 300,000 sq ft distribution centre in Northampton.
The storage and materials handling project awarded to BS Handling Systems has involved the company installing pallet racking, a hanging garment solution (GOH system) for 750,000 units, 5 packing spur belt conveyors and 125 packing benches into the new facility.
Designed to boost productivity
Our client is an international retailer with a business strategy to increase their online sales of clothing, footwear and accessories this distribution centre in Northampton is part of that plan, explains Tim Owrid, development director for Clipper Logistics. He continues, We have a stockholding here of two million items, which rises up to four million at peak so on a busy day we are processing up to 100,000 items.
BS Handling Systems was involved with the fit out process right from the start. I had complete confidence in their commitment to the programme, which was a difficult one due to the strict deadlines and the fact that we werent working to a fixed design. They coped very well with all the changes that were made, pointing out any issues and just getting on with it. It was an evolving design process and they played a significant role in helping with that design.
During the installation we often had trades working simultaneously in the same area, sometimes in a live operational environment in a carefully sequenced overlap. BS Handling performed well, they understand that the way they work with other suppliers as part of a team is more important than the way any individual company works as a component part.
A critical aspect of my job is managing the relationship with my client. In order to do that I have to rely on contractors who are flexible and able to deliver and BS Handling was absolutely central to that.
Profit hinges on an efficient layout
At present the distribution centre operates at ground level a large mezzanine is planned for the second phase of the fit out. Bulk storage is held in pallet racking which has been erected along one side of the DC. This racking acts as a marshalling area between palletised goods arriving, being broken down and placed into stock.
The GOH system, designed and installed by BS Handling Systems to store 750,000 garments, dominates the floor area. The garment racking is arranged into blocks, with each storage block containing five runs of nine bays and each bay having two storage rails per side. This gives a total hanging capacity of 9,450 garments for each block.
To process and pack the orders BS Handling Systems has designed and installed a conveying solution to provide the efficient handling of up to 100,000 items per day. Once the orders have been picked out of storage they are processed at one of the 100 packing stations which are positioned beside the packing spur conveyors.
There are 5 conveyors, each equipped with 10 benches on either side. Once each order has been completed it is placed onto the belt conveyor running alongside the operative. Orders then accumulate at the end of each conveyor where they are put into the correct cage for onward despatch.
A further 25 packing benches have also been supplied by BS Handling; these are used by the goods in operational team.