Forvia Automates Storage and Supply of Parts
1st April 2025
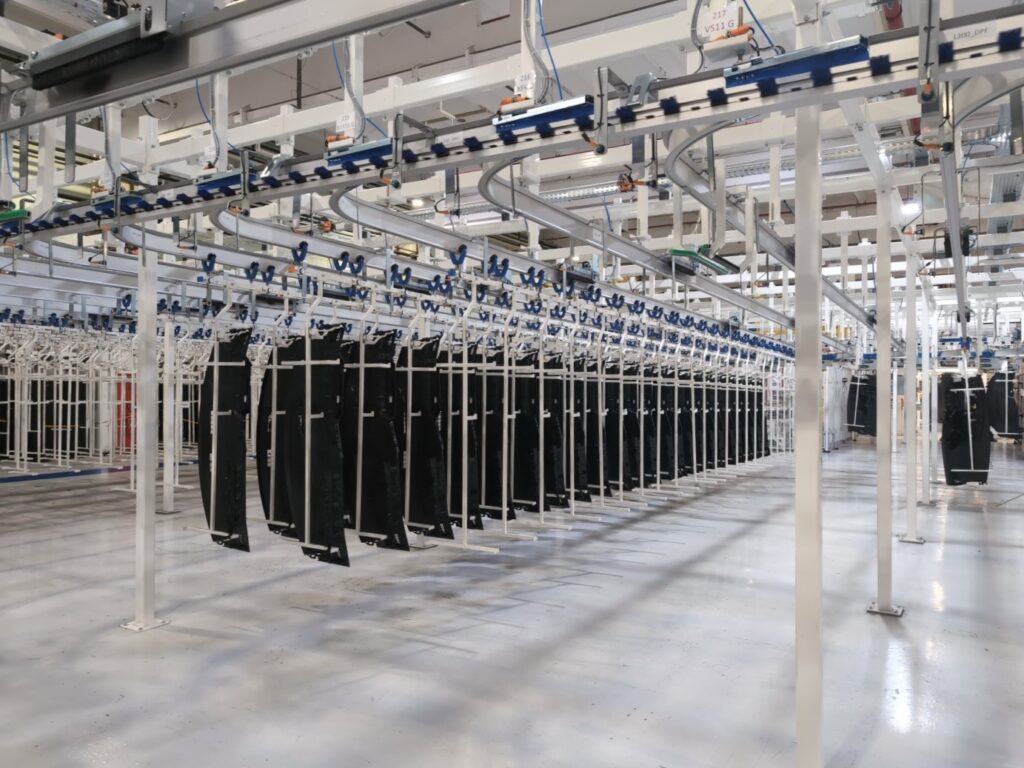
Faced with an increase in its activity and the number of references to be processed, automotive parts supplier FORVIA chose Transitic to optimise its logistics flows at its Hénin Beaumont site in France. Thanks to two networks of automated overhead conveyors, the plant now ensures precise sequencing of parts and continuous supply of workstations, thereby optimising productivity.
FORVIA, the result of the merger between Faurecia and Hella, has established itself as a major global player in the design and production of automotive components and systems. Its expertise covers a wide range of solutions, from interior fittings to sustainable technologies. In France, FORVIA employs more than 10,000 people at 52 industrial sites,including Hénin-Beaumont in the north of the country.
FORVIA Hénin-Beaumont was faced with an increase in the number of parts to be managed, resulting in a more substantial daily flow. In this context, the teams wanted to increase their storage capacity while automating the supply and sorting of parts for greater precision throughout the production chain.
Unique Solution
Two independent networks of overhead conveyors, combining motorised and gravity sections, act as buffer-sequencers. They ensure the storage, transport and scheduling of parts, guaranteeing a continuous, organised flow to the workstations.
The first part of the installation comprisesthree workstations, each fed by emptytrolleys custom-designed to transportFORVIA parts. Once they have been loaded,the operators identify each trolley using an RFID tag, thus associating the parts with their support.
The trolleys are then directed to a first overhead storage network, made up of 18 lines and able to accommodate up to 450 trolleys. Depending on the type of part, they are directed to two separate machining centres, then emptied and finally evacuated to an automatic recirculation loop.
Once the parts have been machined,they are reloaded onto new trolleys, identified and then integrated into a second storage network. The latter was retrofitted from an old overhead system installed by Transitic in 2021. It has been recovered, extended and optimised to meet FORVIA’s new requirements. Equipped with 23 storage lines and a total capacity of 500 trolleys, this buffer ensures the sequencing of parts and routes them in a precise order to the different workstations according to their assembly line.
“Sequencing errors have been completely eliminated,” says Marc Lefebvre, Methods Manager at FORVIA. “The working comfort of our operators has also been improved by drastically reducing manual tasks and travel,” he adds.The entire installation currently operates at the rate of one trolley per minute, and can achieve a maximum production rate of 800 parts per day.
similar news