Sortation Case Study: Prepared for Peak Times
11th July 2018
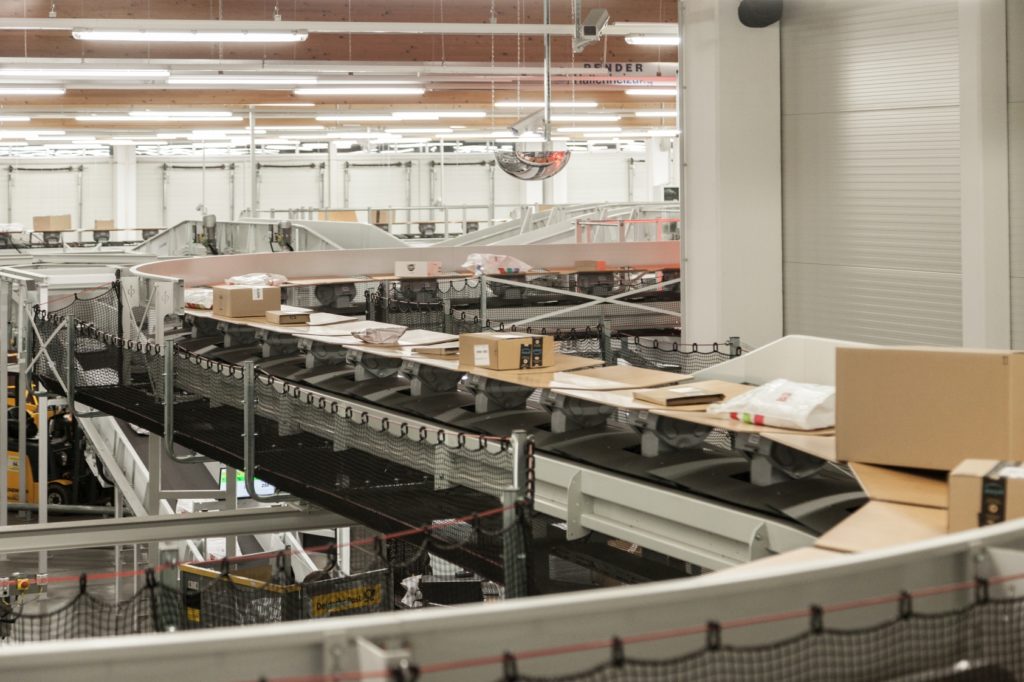
Austrian postal service Österreichische Post AG has built its new distribution centre in Wernberg, in the southernmost Austrian state of Carinthia. Up to 30,000 packages are handled on a daily basis. The sortation system is at the heart of the logistics centre: it handles the sortation demands reliably and responds quickly during peak times. The BG Sorter is Beumer Group’s latest system development. It is powerful and energy-efficient yet runs so quietly that the working environment remains pleasant. The managers were also impressed by the trouble-free handling of the project.
Parcel shipping is growing worldwide, and Austria is no exception of course. One of the reasons for this growth is the enormous increase in online orders. Customers want their orders to arrive ideally on the same day, delivered right to their doorstep. Logistics and parcel services must be able to react accordingly to those demands, because the competition is fierce. The Austrian postal service has responded to this tough task and opened a new distribution centre in Wernberg, in the state of Carinthia. Put into operation in the summer of 2017, it distributes and delivers packages in Austria’s southernmost state and East Tyrol. “The move to Wernberg was necessary, because the site in St. Magdalen no longer met our requirements,” explains the new branch manager Kathrin Fischer. “The old distribution technology was no longer capable of handling the increasing volume and the hall was too small to install a new system.” While the St. Magdalen site will remain operational for the distribution of letters, the most modern sortation and distribution system for packages, with a footprint of 5,000 square metres, is now operating for the Austrian postal service in a facility with 12,000 square metres of total space.
High technology, small footprint
The site is conveniently located between two big cities, Villach and Klagenfurt, easily accessible from the autobahn. On average, approximately 30,000 packages are handled per day, increasing to up to 50,000 during peak times such as leading up to Christmas. That means up to 6,000 packages per hour. “The various parcels must be handled with care and distributed quickly and accurately,” said Fischer. The sortation system must meet these high demands. Beumer Group provided the necessary technology, with its new high-capacity BG Sorter at its core, designed as a tilt tray sorter. “Our components have been installed, from goods receipt to goods issue,” reports Frank Niemietz, Sales Manager Logistic Systems at Beumer Group. Wernberg is a comparatively small site of the Austrian postal service. Beumer Group had to install the entire system in the already existing hall with very little space.
BG Sorter: adjustable, quiet, reliable
When a truck docks at the hall for unloading, an employee places the packages on a horizontally and vertically adjustable telescopic belt conveyor. It transports the packages, which vary in shape and weight onto a Beumer Parcel Belt Conveyor. The weight of each package is precisely calculated. The shipments are then dispatched onto the BG Sorter. The system can assign the parcels to the right destination because it is equipped with barcode recognition and with a laser system that continuously detects the parcel’s volume and reports the result to the superordinate data processing system. If the packages cannot be read then they are sent to a special destination. An employee inspects and processes the parcels, then returns them to the BG Sorter.
“Our BG Sorter is based on tried-and-tested technologies,” explains Frank Niemietz. “This includes the sorter frame made out of steel and the contactless energy supply instead of the typical contact lines, which are commonly used by the competition.” The tilt tray sorter design is capable of conveying items of up to 60 kilograms. Wireless communication enables real-time data transmission, unlike infrared communication where data are transmitted only when an infrared sensor is passed. This reduces the communication time to milliseconds. “Different operating modes are also easily implemented. This allows us to respond better to sensitive products,” explains Niemietz. “The items are discharged at different speeds and with high precision.” Users can handle items of different sizes with more flexibility. “This machine allows us to handle a large mix of product with precision while being cost effective; and distribute to other logistics centres in Austria and our distribution units in Carinthia and East Tyrol,” says Fischer.
Energy-efficient drive
The new Beumer system is equipped with energy-efficient drives. The servo drive-based OptiDrive reduces power consumption and CO2 emissions. The contact pressure of the drive wheel is automatically set depending on the required driving power – even for braking, which makes this solution highly efficient and force-fitting. This boosts efficiency to up to 90 percent and enhances the service life of the drive wheels. The BG Sorter is equipped with carrying wheels that are larger than those used in comparable systems. They reduce the rotation frequency by 25 percent. This has a positive effect on the wear and tear and the noise. “One very important aspect for our 40 employees,” says Fischer. “It stays very quiet in this hall, you can easily talk to each other, the operating volume remains very pleasant, which means it causes no additional stress for the employees.”
The packages are transferred via chutes onto telescoping belt conveyors. The items are taken off the conveyors and transferred into swap bodies. They are then transferred onto trucks that carry them to one of the other six distribution centres in Austria.
Smooth project handling and reliable service
After the successful completion of the project, Beumer Group continues servicing the customer. Österreichische Post has signed a hotline contract with Beumer customer support. This allows the customer to contact a service engineer whenever necessary. If the machines come to a standstill, Beumer Group can dial in directly to the machine via a VPN connection, examine the situation and solve the problem directly or come up with a solution together with the customer.
“This project was carried out extremely professionally and our communication with Beumer was honest and direct the entire time,” says Gert Haas, Technical Director at Österreichische Post AG, Region West. “We were able to stay on schedule and the entire system was commissioned on time. Quite extraordinary for a project of that size.” Branch manager Kathrin Fischer is very satisfied. “The BG sorter operates very quietly, is highly reliable, and extremely precise and fast when it comes to sorting the products.” And speed is a valuable asset in this industry, on top of the list for the customers. “We are the only parcel service in Austria that delivers six days a week, from Monday to Saturday,” says Fischer.