Greater Flexibility, Safety and Productivity: Fully-automatic
16th November 2020
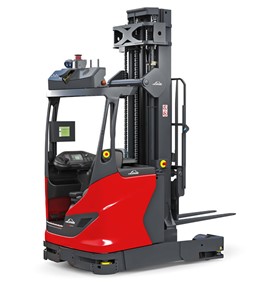
They never get sick, make no mistakes and work tirelessly around the clock: Automated industrial trucks offer a wide range of clear advantages.
Linde Material Handling has updated its comprehensive product range wih the second-generation Linde R-MATIC reach truck and an additional Linde L-MATIC HD model. The experience Linde has gained from past projects involving over 50 vehicles has gone into the further development of its reach trucks. The resulting performance characteristics ensure greater productivity, safety and flexibility.
Pallet warehouses play a central role as material buffers both in industrial manufacturing processes and in distribution centers. Storage and retrieval operations in high-bay racking systems are usually standardized processes entailing a high degree of repetition. As a rule, the narrower the distances between the rows of shelves and the more precise the positioning of the individual pallets, the more efficient the warehouse. This is exactly what makes pallet storage systems the ideal field of application for automated equipment such as the Linde R-MATIC reach truck and the Linde L-MATIC HD pallet stacker.
The new Linde trucks can work with maximum precision even in the tightest of spaces: With a length of 2,520 millimeters and a width of 1,565 millimeters, the Linde R-MATIC (1.6-ton load capacity) is the only automated hybrid reach truck on the EMEA-market that can maneuver in aisles as narrow as 2.90 meters. Software-controlled, the vehicle can store pallets with extremely high accuracy even at lifting heights of more than eleven meters. “The design, maneuverability, load handling and precision of these automated industrial trucks are decisive for the performance of the overall system,” says Alexandra Mertel, Product Manager Automation & Intralogistics Solutions at Linde Material Handling: “These criteria are crucial for enabling the pallets to be placed precisely at the intended storage locations and for pick-and-drop cycles to be improved.”
With the help of an infrastructure-free laser navigation system, the trucks dynamically steer their way through the warehouse, receiving transport orders directly from the warehouse management system via the central control unit.
The trucks receive a noticeable productivity boost from the auto-calibrating 3D camera that is equipped with a new software generation. Not only does this camera recognize the dimensions of the pallet markedly better, it can also see deeper into the pallet, which makes picking up the pallet and placing it down much more precise – whether on the ground, on roller conveyors or on the shelves. At the same time, the automated vehicles are able to transport a greater variety of pallets. This is ensured by relative image recognition algorithms developed exclusively for Linde Material Handling that have been validated in extensive tests.
As is standard practice at Linde Material Handling, the automated trucks meet the highest safety requirements. Four scanners are integrated into the vehicle at floor level, producing a 360-degree safety field around the vehicle and constantly screening for obstacles. The standard equipment also includes additional emergency stop switches, the well-known Linde Blue Spot and the Dynamic Mast Control system, which provides valuable assistance at great lifting heights. Optionally available equipment includes a sensor that detects overhanging loads and a second, higher-positioned 3D camera that can generate time savings in load handling.
The two Linde L-MATIC HD models with 1.6- and 2.0-ton load capacity feature all around safety equipment as well, including side bumpers, standard and optional scanners, emergency stop switches and optical and acoustic warning systems. Here too, load detection is via the innovative 3D camera.
Reach trucks and pallet stackers are designed as a hybrid solution, allowing the operator to take control of the truck at any time and switch to manual mode. Another new feature is the autonomous charging ability. Equipped with fast-charging batteries, the automated industrial trucks drive to the charging station independently for recharging.
“In addition to the appropriate technology, a provider’s consulting expertise also plays a decisive role in automation projects,” says Product Manager Alexandra Mertel from Linde Material Handling. In order to find a suitable solution for a particular customer, numerous parameters must be checked during the planning stage. “We first need to completely understand the customer’s expectations. Only then can the system be developed and the trucks configured in detail.” Here, specialists from Linde Material Handling work closely with different departments on the customer side (e.g. Purchasing, Logistics, Engineering). “For this purpose, we have set up our own implementation team to ensure the reliable commissioning of the vehicles. This enables us to provide comprehensive support to our customers,” emphasizes Mertel.