Case Study: EnerSys and Unicarriers Make Dutch Fleet More Sustainable
23rd October 2019
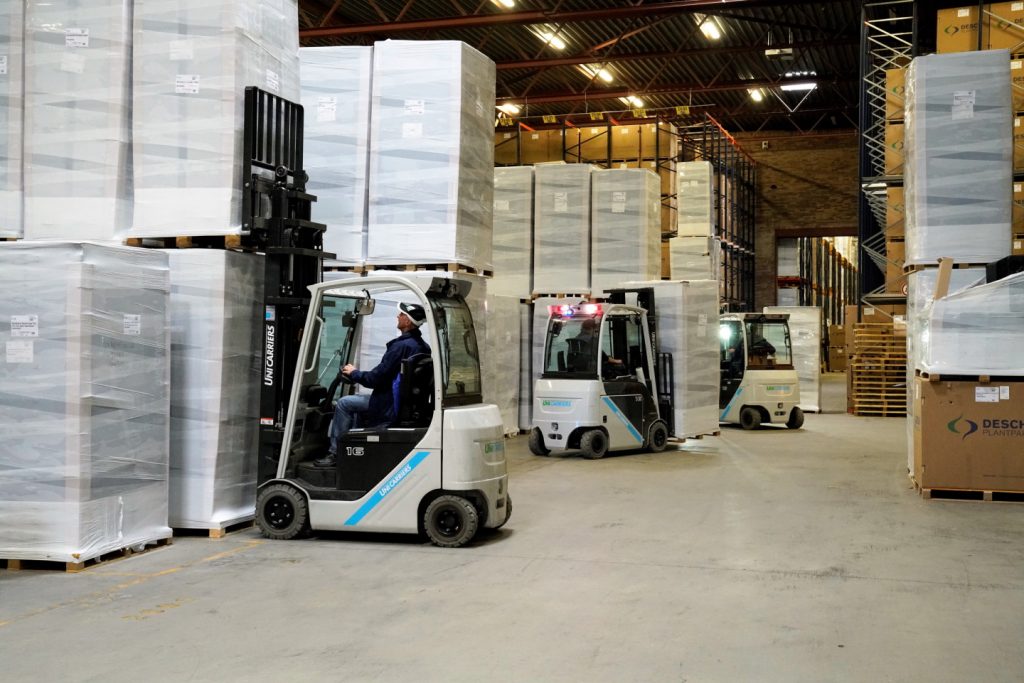
Netherlands-based Desch Plantpak has modernised its internal transport fleet by selecting UniCarriers to supply ten electric forklift trucks from its new TX series. The electric forklift trucks are equipped with NexSys Thin Plate Pure Lead (TPPL) batteries from EnerSys, which make unimpeded interim recharging possible.
Desch Plantpak devises and produces all kinds of innovative solutions for the professional horticultural sector. Pellets are supplied for the production of rolls of film, which are transported to an intermediate storage facility. The rolls are transported from the intermediate storage facility on a call-off basis to the various production units, which transform the film into flowerpots, plant trays and plant packs. Once the finished products have been palletised and wrapped in film, the goods are shuttled to the warehouse, just a stone’s throw away. From here the goods are transported to customers across the globe.
“Good internal transport is essential for us,” says Cecile van Daalen, responsible for Desch Plantpak’s logistics, among other things. The trucks are responsible for supplying the machines on the factory floor. “And we can’t do without forklift trucks for loading and unloading raw materials and loading the shuttles for our warehouse,” adds Bas Langenberg, planner in the Technical Services department. The trucks unload the shuttles in the warehouse once they have supplied the finished products from the production facility. They are also responsible for product entry and exit and order collection.
The lease contracts of the trucks in the production department and the warehouse were coming to an end, prompting Desch to investigate suitable providers of renewed internal transport solutions. This was found in UniCarriers, which supplied a total of twelve new trucks: three TX3 electrically powered trucks, with load capacities of 1.6 tonnes and two DX combustion engines (1.8 tonnes and 3.2 tonnes) supplied for the production department, and seven electric TX4 1.6 tonne trucks for the warehouse.
The specific wishes and requirements of deployment differ considerably for the two departments. Availability is essential on the factory floor. To guarantee short delivery times for its clients, Desch always strives to deliver from stock. The bar is certainly high during high season and much is demanded of the forklift trucks. “It’s full steam ahead from January through to May, and we even work on Sundays during that time. There are sometimes as many as 25 full trucks in the yard at once during that peak period,” Bas Langenberg continues.
The average operating time of a forklift truck in Desch’s production department is some 2,000 hours/year. It was precisely the high level of availability that led the company to rely entirely on LPG trucks until recently. The combustion engines have been available almost continuously. After all, if an LPG tank is empty, it is exchanged for a full one in no time at all and the truck can continue operating again.
However, Desch was eager to switch to quiet, zero-emission electric trucks for its new fleet of vehicles. “Not just because of the emissions,” Bas Langenberg explains. “The operating costs of electric vehicles are lower than those of combustion engines. Moreover, the trucks are less prone to failure.” What is more, the 1.6 tonne electric powered three-wheelers are more compact and agile than the 1.8 tonne vehicles in use until then. “That makes the trucks lighter and more energy efficient,” Bas Langenberg says.
Of course, availability remained crucial. And there is simply no room in the production facility for a special, expensive charging station. For this reason, as well as from a safety perspective, the use of exchangeable batteries was not an option. “We also looked at lithium-ion batteries, but that technology is still rather young for us. There are not enough references right now, so we weren’t confident enough in choosing that solution,” Mr Langenberg relates.
On the recommendation of UniCarriers and in collaboration with battery supplier EnerSys, Desch ultimately opted for NexSys batteries. Like lithium-ion batteries, the 48 V/625 Ah batteries allow for interim recharging, but the NexSys technology has been available for some time and has more than proven its worth. “Our drivers can now connect their trucks to the charging station during their coffee break, for example, so that we can continue operating throughout the hours needed,” Mr Langenberg says. To make (interim) recharging of the batteries as quick and simple as possible, UniCarriers moved the battery connector to the entry and exit side of the trucks.
Anouk Mantoua – Sales and Service manager Motive Power Netherlands at EnerSys summarised that it was a great experience to work with UniCarriers in the project, which has seen Desch Plantpak gain from choosing UniCarriers trucks powered by NexSys TPPL batteries.
Both Ms Van Daalen and Mr Langenberg are very satisfied with the collaboration with UniCarriers and EnerSys. “This is the first time we have worked with them. We were particularly impressed with how they thought along with us during the tender process and how quickly they responded,” Ms Van Daalen adds. “The future will tell whether the promises made regarding service are actually upheld. We have no experience with this. But I am convinced that it will be fine too.” All the trucks have been leased for a 72-month period, including a maintenance contract.