Case Study: Moving Perishable Goods in Food Applications
16th May 2019
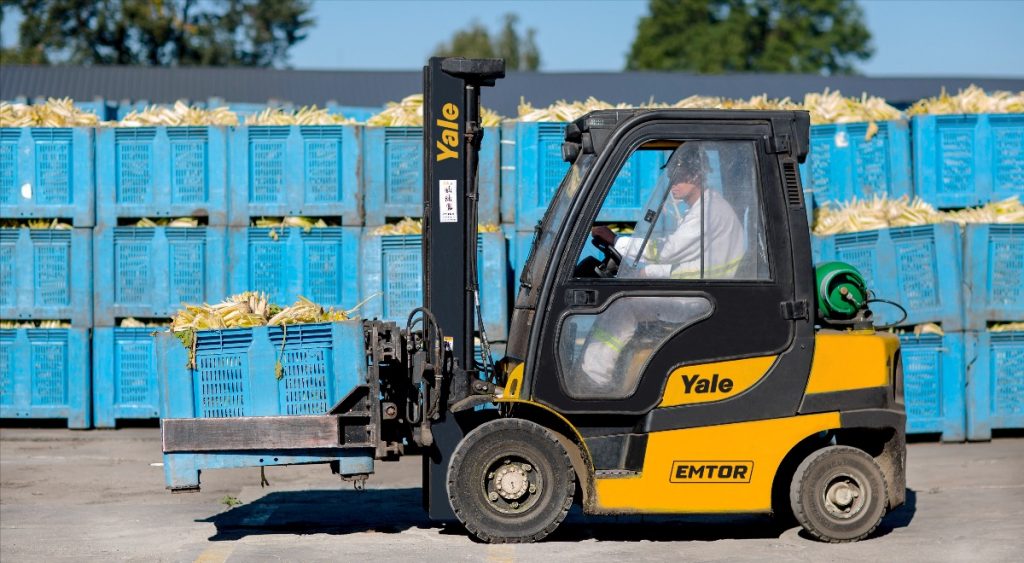
Yale industry experts understand the challenges associated with moving perishable goods in food applications and the demands that operating in cold environments place on materials handling equipment. This understanding has been a key part in the successful relationship between Yale dealer Emtor and the Bonduelle vegetable factory in Gniewkowo, Poland.
Processing around 30,000 tonnes of vegetables annually, the main output of the company’s Gniewkowo factory is frozen produce. Bonduelle vegetables undergo a long, complex process of washing, blanching, and tunnel freezing before they are ready to reach the consumer’s table and proven, efficient materials handling processes play a crucial role in ensuring the smooth running of the factory.
Bespoke solutions keep the cold out
The factory’s current fleet consists of 40 long-term rental Yale trucks, supplied by national dealer, Emtor, who have been providing Yale equipment to the factory for over 10 years.
Emtor carefully consider the needs of the application and continue to work closely with Bonduelle to ensure the rental trucks are ideally suited to the operating environment. The working conditions onsite vary from refrigeration environments (0-4°C) to dedicated cold stores where the temperatures can drop down to -18°C, therefore customised solutions are needed to prepare the equipment for temperature-controlled environments. The Yale trucks provided by Emtor feature enclosed cabins fitted with heated double glazing, double skin insulation and in cabin thermostatic heating, providing operators with a warm and comfortable workspace, whilst helping to reduce the risk of fogging when moving between cold and temperate environments. But the truck cabins are just one way in which Emtor has considered the needs of this customer.
“In our factory, semi-finished products are stored in a block system warehouse, and only finished products migrate to pallet racking. We discussed the need to ‘slim down’ the width of the reach trucks that will work in this area with Emtor because the aisles in our warehouse are extremely narrow. They took up the challenge and prepared narrower versions in line with the Polish Office of Technical Inspection’s requirements especially for us, which are doing well in our narrow aisles” said Paweł Łyczywek, Logistics and Supply Chain Director at Bonduelle.
Reach trucks make up the majority of the Yale fleet onsite with loads being stored at heights of up to 8.5 metres. The reach trucks are also fitted with special HD masts and have a low lifting capacity, enabling them to lift the same load capacity over the entire lifting height.
Electric trucks with a lifting capacity of 1.6 tonnes and higher capacity LPG trucks (1.8-2.5 tonnes) fitted with rotator attachments complement the reach trucks, undertaking tasks outside the warehouse. Most of the equipment in the factory operates seven days a week in a three-shift mode and is equipped with side battery extraction to save time and reduce the disruption caused by changing batteries.
“In the past, replacing the batteries from the top and manipulating them at height was a difficult operation that came with certain risks. The range of trucks we use is very broad, from reach trucks through to warehouse trucks, that’s why unifying the battery exchange system and adapting it to the various models we use is an important element of security for us,” said Paweł.
Dealer relationship the key to success
The majority of the trucks at the Bonduelle Gniewkowo factory operate on a long-term contract for a period of five years, after which they are exchanged for new ones. A shorter, three-year rental period covers the most intensively used trucks.
“The shorter rental period for some trucks is due to the extreme pressure they are subjected to. Some of the Yale forklifts we use transport loads of up to 15,000 tonnes a year,” said Wiktor Kwiatkowski, Transport Manager at Bonduelle.
Paweł added: “This rental agreement helps us maximise the efficiency of our fleet. We are confident that for five years of operation we can work relatively trouble-free, and if necessary, we can count on an immediate elimination of defects or replacement trucks from Emtor, which provides us with uninterrupted continuity of work.”
Emtor guarantees an on-site service in Gniewkowo by providing a dedicated mechanic. However, during the busiest period of the year when the most intense work is under way, the service team is increased with a further two technicians based at the factory.
In addition to the on-site service provided by Emtor, the Yale dealer also has a warehouse within close proximity to Bonduelle. “We have a very well-equipped spare parts warehouse, supported by an outstanding Yale spare part distribution centre, along with a host of replacement trucks, which is why we are able to efficiently repair or replace a forklift if necessary. Emtor is a family company in which the decision-making process is undoubtedly shorter than in a corporation, hence our ability to flexibly adapt to the needs of our clients,” says Dariusz Czaplicki, Technical and Sales Consultant for Emtor.
“I am glad that we have the opportunity to implement such a broad cross-section of solutions for Bonduelle. Thanks to this, we are able to work together to test different options, build expertise, and provide valuable feedback to their factories, allowing us to constantly improve our service,” concluded Dariusz.