Driver-Friendly Design “Future Proofs Efficiency” Says Hyster
8th October 2018
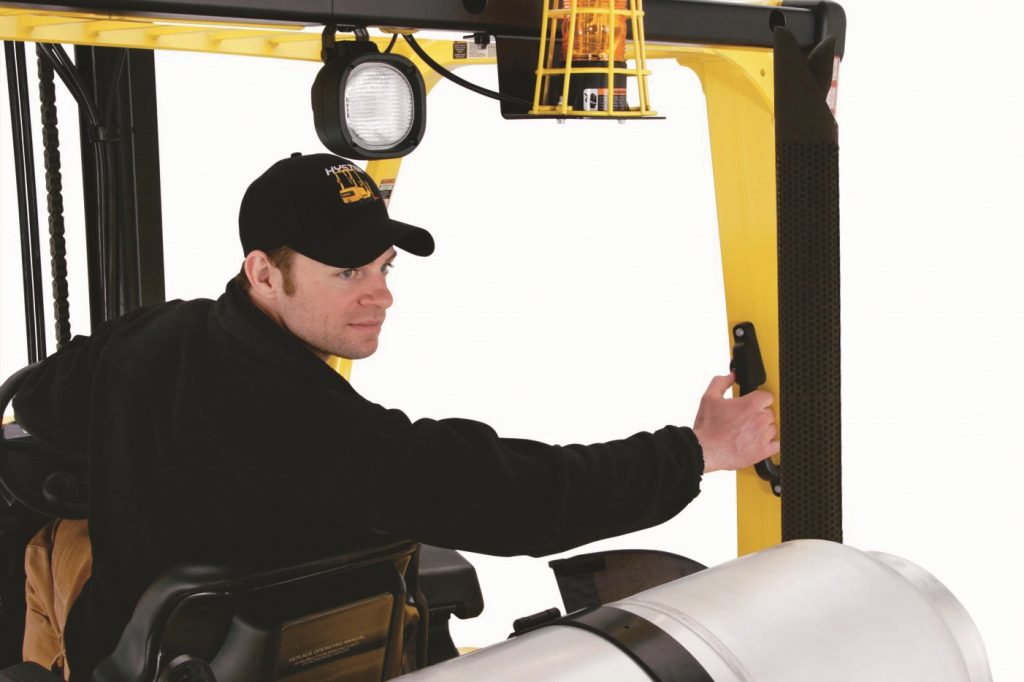
While reports of self-drive cars and lorries captivate mainstream media, automated lift trucks are already a reality in a growing number of operations. Hyster Europe believes new innovations to help human operators to be more productive remains essential for counterbalance lift truck manufacturers.
“Automation is perfect for many repetitive tasks, but it may never be the right option for everyone,” says Phil Mean, Product Strategy Manager for Hyster Europe, which already provides fully and partially automated lift truck solutions.
“However, enhancing the efficiency of a human lift truck operator with new features that support increased comfort, awareness or visibility remains essential,” he says. “Continued innovation enhances Hyster® counterbalance lift trucks to increase productivity in real life applications, and it is usually the small details that make a big difference.”
The IC powered Hyster® XT series, features new design elements that contribute to improved driver efficiency. The truck is designed for everyday operations, so the layout and design of the controls make it easy for operators to activate the hydraulics when they are getting on and off the truck regularly.
“We are constantly innovating to enhance the driver’s efficiency, but the choice of controls depends on the application requirements,” says Phil. “For instance, on the Hyster® FT series, we developed a new joystick option for sites using additional attachments.”
“We also developed the “TouchPoint™” mini-lever armrest as an option for Hyster® Fortens® lift trucks. This places the truck controls at the driver’s fingertips to help minimise driver movement, while allowing fast and accurate control,” says Phil.
The intelligent design of Hyster® electric counterbalance lift trucks provides a zero turning radius to help drivers turn more easily, giving them more space to be more efficient.
“Understanding how forklifts are used in different applications is key to developing a truck with the operator’s productivity in mind,” explains Phil. “An operator of a Hyster® FT counterbalance truck in a high intensity 24/7 logistics operation, for example, can benefit from features and options such as the Auto-deceleration System (ADS), Controlled Power Reversal, Autospeed Hydraulics and Anti-rollback on ramp.”
“All of these features can contribute to more efficient and accurate manoeuvring in real life operations,” he continues.
For applications where lift truck drivers spend a lot of time reversing, Hyster Europe has used intelligent design on its counterbalance forklift range to help reduce back and neck strain for the driver. Lift trucks combine slim overhead guard legs, low counterweight height and a well-positioned rear grab handle with integrated horn button to keep drivers comfortable, and efficient, even when moving in reverse.
An optional swivel or, in some cases, rotating seat on a counterbalance lift truck allows further improvements in both visibility and driver comfort which can lead to even greater efficiency.
“While repetitive tasks are suited to automation, many factors with operations are variable, such as the weight of a load,” says Phil. Hyster Europe has recently introduced a new range of mobile weighing solutions so operators can accurately weigh loads during transport, rather than transporting each load to a static scale, saving valuable time and increasing efficiency.
“On board weighing helps operators in so many ways,” says Phil. “They can fix issues with incoming goods there and then, record shipping weights, identify picking errors, check filling levels or even mix ingredients and dose more easily. They can of course also avoid overloading if the load is unknown.”
“There are so many new innovations that help operator efficiency and more are expected,” says Phil. “We continue to place the operator at the heart of our designs while embracing the benefits of automation, and other new technologies, where it best meets the needs of certain applications.”