Industry View: Materials Handling in the Chemical Supply Chain
11th December 2019
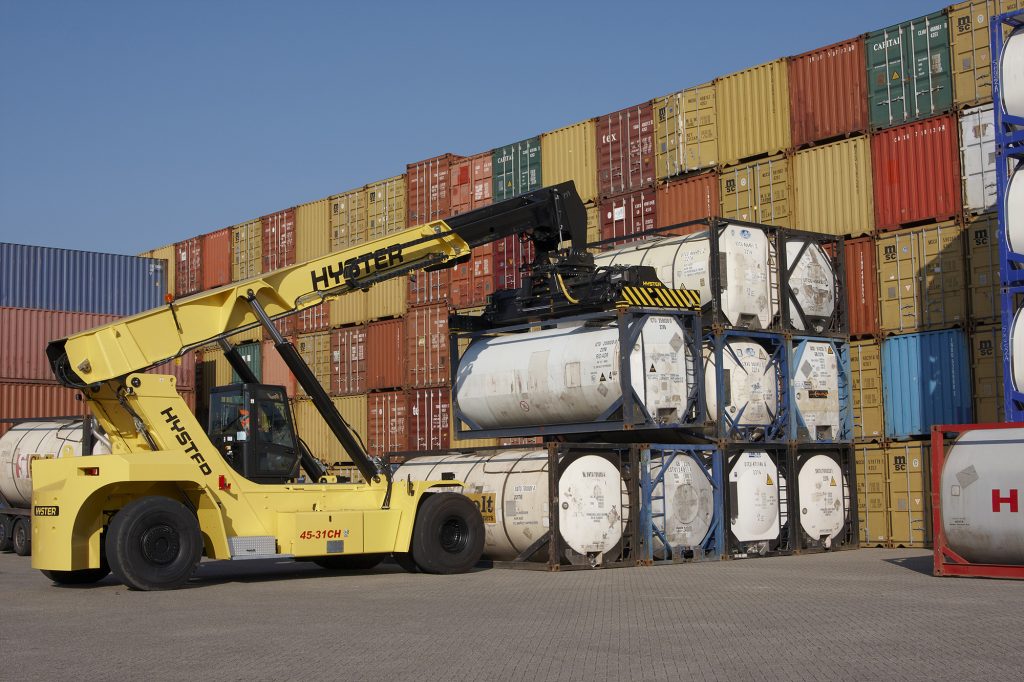
Many external factors affecting materials handling operations in the chemical supply chain are not immediately obvious. Mark Nailer, Industry Manager for Hyster Europe discusses some of the unexpected, but very important, industry trends that chemical handling applications should consider.
Businesses are utilising materials handling equipment at many different stages of the chemical supply chain, from raw materials transport, to dosing during manufacturing and the storage and distribution of finished goods, such as agrichemicals, paints and food additives. While these applications rely on Hyster® lift trucks for efficiency, accuracy and a low cost of ownership, they are also looking for support in overcoming other key challenges that affect the chemical industry.
1. The reduction of plastic
Increasingly, society, industry and government are looking to reduce plastic usage and production. At EU level, a Directive which comes into force in 2021* will ban certain single use plastics and the UK government plans to introduce taxes on plastic packaging, while also investing £40 million to support plastic reducing and increase recycling**. Since plastic production accounts for more than one-third of the chemical industry’s activity***, many applications therefore need to optimise their operations.
With our expert distribution partners, we work closely with customers to recommend the best solutions. For instance, our Hyster® warehouse simulator can help identify operational issues and test out potential solutions or different ways of working. This provides a detailed operational forecast to help businesses storing or transporting chemicals to make an informed decision – even if that means recommending they have fewer lift trucks!
2. The strive for cleaner and greener operations
Often, the public’s perception of businesses in the chemical supply chain is that they are ‘dirty’ and big contributors to pollution. However, many of our customers in this sector are very committed to reducing their environmental impact and this is driving demand for zero-emissions Hyster® electric lift trucks, particularly those powered by lithium-ion batteries.
Lithium-ion has no acid which could spill and no fumes – hydrogen and other gases can be produced by lead acid, which are unwelcome for operations looking to be ‘cleaner and greener’. Lithium-ion also offers other benefits in the right application, including reduced maintenance, lower total battery costs and simpler operations thanks to opportunity charging.
To further support those focused on reduced emissions, Hyster Europe also provides Stage V engines on several of its FT and XT ICE forklifts, making them cleaner than ever before.
While fossil fuels and batteries are still the choice of most, in certain applications with the right infrastructure, fuel cells may be a more suitable power option. Hyster Europe alongside fuel cell manufacturer Nuvera is currently developing solutions for customers in the chemical industry.
3. The thirst for ‘Big Data’
In the Logistics 4.0 landscape, businesses are increasingly focused on capturing and analysing ‘big data’ to inform operations. The chemical supply chain is no exception. In a competitive industry where organisations are always keen to be innovators, manufacturers are now commonly integrating their operating systems with blockchain technology for increased efficiency and security.
When it comes to materials handling, this means that there is a greater need for data to feed into these systems. Many customers in the pharmaceutical, petrochemical and agrichemical businesses utilise Hyster Tracker telematics to provide essential data on operator performance, specific truck usage, fuel emissions, fleet location and idle time.
Hyster Tracker also enables impacts to be sensed, report and logged as well as ways to track and respond efficiently to fault codes. Plus, the system’s online portal also provides a way to aggregate and analyse materials handling equipment fleet costs to see a real total cost of ownership.
4. The rise of the robots
The chemical supply chain is frequently handling high value raw materials and finished goods, making damage limitation a high priority. As a result, the adoption of automated solutions to remove the ‘human factors’ is increasing. In fact, research has shown that European manufacturing operations have the highest density of industrial robots worldwide.****
Applications can automate chemical supply chain handling tasks with affordable Hyster® robotic solutions. ‘Driven by Balyo’ technology combines reliable Hyster® lift trucks, such as tow tractors, pedestrian counterbalance trucks and low-level order pickers, with robotic control systems to help improve accuracy, boost efficiency and reduce damage, keeping busy production lines running smoothly, while driving down cost.
This also helps operations to realise the competitive advantage of running 24/7 manufacturing operations.
5. Ever-changing oil prices
Raw materials logistics is by its nature unpredictable, with oil prices a difficult variable to manage in a changing world. To counter this, certainty in materials handling is highly important for our customers in the chemical sector.
One thing industrial chemical applications can continue to rely on is their Hyster® lift trucks, which offer consistent cost and operational efficiencies. What’s more, as variables and operational needs change, the global network of local Hyster® dealers can provide short term rental agreements that can enable fleets to adapt as quickly as needed. Where budgets are always high on the agenda, this can also help organisations to more effectively manage their capital expenditure.
Whilst external factors will continue to provide challenges and uncertainty for operations handling chemicals, Hyster® delivers reliable solutions with safety at their centre to optimally meet the specific application needs at every stage of the supply chain.