Staying safe in the warehouse with STILL
21st May 2021
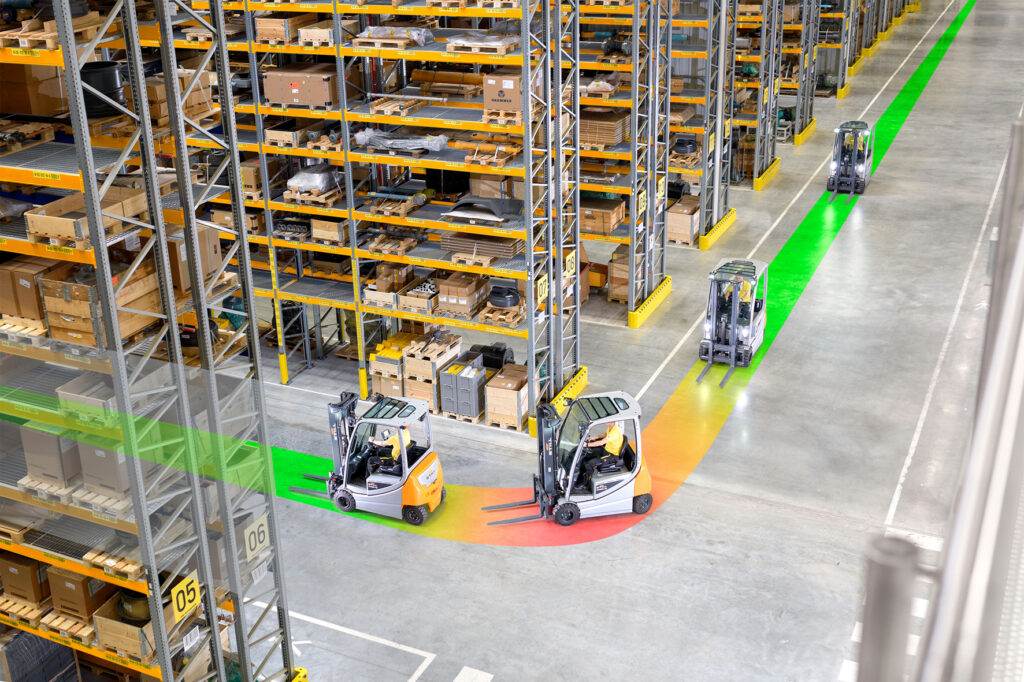
Hamburg-based intralogistics supplier STILL recently presented a webinar highlighting ways in which it has harnessed technology to help make the warehouse workplace safer.
In Germany alone, more than 20,000 reportable occupational accidents involving forklift trucks and warehouse equipment occurred last year. So much for the bad news. The good news: there are effective assistance systems that help prevent such accidents. STILL presented some of these innovative safety solutions in a webinar entitled Safe around the warehouse with industrial trucks.
To demonstrate where hazards lurk in the warehouse, Jürgen Wrusch and Janos Poppe took the webinar participants on a virtual warehouse tour. On the way, the two STILL experts explained that each warehouse has specific features and, as a result, an individual risk ranking.
Access and usage control
As early as at the beginning of the shift, hazards may arise from willful or negligent misconduct. For example, when vehicles are used without permission. This could be people who either do not have a driving license or whose driving ability is impaired. Or those who – without thinking of the consequences of their behaviour – want to use damaged vehicles or vehicles unsuitable for the task.
“Each of these reasons conjures up incalculable dangers,” emphasised Poppe. This can be remedied by systems that ensure that only competent operators use a suitable vehicle in proper technical condition. One of these systems is the pre-shift check feature of the STILL Easy Control on-board computer: before the start of each shift, or at user-defined intervals, drivers must confirm the vehicle’s operability via the on-board computer before they can operate the vehicle with all its functions.
STILL’s FleetManager access control system also offers a comprehensive suite of reports and telematics applications that can be used to monitor the use of trucks and drivers on the site. Acceleration sensors can also be used to monitor the driving style of the operators and – if necessary – intervene in the vehicle control.
“The sensor detects mechanical shocks and immediately generates a speed reduction. Road hogs whose wanton misbehaviour poses a danger to people and equipment are thus quickly unmasked and slowed down,” says Poppe.
Collision accidents
After successful access control, movement through the warehouse begins. From this moment on, there is a risk of collisions with other people or vehicles. “One way to prevent this is to use visual warning signals. These significantly increase the perceptibility of the vehicles,” explained Wrusch to the webinar participants.
A proven solution for this is the STILL warning zone light. The optional lighting equipment acts as a visual warning for pedestrians and other drivers in the immediate vicinity by projecting luminous strips onto the side of the hall floor next to the vehicle. This makes the STILL warning zone light a good complement to the STILL Safety Light. This projects blue light dots onto the ground at a distance of approx. 5m in front of and behind the vehicle, which warn of the approaching vehicle and can thus prevent an imminent collision.
A big step towards completely avoiding collision damage to people and vehicles are radio-based safety systems. “The basic principle of these systems is to establish bidirectional communication via radio waves between vehicles, pedestrians and stationary equipment even without visual contact. For this purpose, this equipment as well as all pedestrians and vehicles are equipped with radio modules,” explained Wrusch. With their help, vehicle control can take place automatically in danger zones, for example by reducing the speed or braking the vehicle if there is a risk of collision.
Tipping accidents
Whenever the forklift truck is in a hurry on its way to the next task, the top risk looms: a tipping accident. “These occur with heavy counterbalance trucks as well as with pallet trucks. The frequent cause is excessive cornering speed,” recounted Poppe.
However, STILL has a suitable remedy for this risk, too, in the form of Curve Speed Control. The steering angle-dependent speed limitation reduces a possible tipping accident by ensuring an appropriate cornering speed. This assistance function is available for various forklift trucks and warehouse equipment and automatically regulates the travel speed depending on the steering angle. This means that the driver does not have to worry about speed when cornering. The vehicle automatically brakes exactly to the point where the operator is safe and at the same time as fast as possible when cornering.
Tipping accidents also occur when drivers overestimate the load capacity of their equipment. If there is too much load on the front of the forks, the truck tips over into the racking. To prevent this from happening, STILL has developed the Dynamic Load Control assistance system. This system limits the lifting height in relation to the load weight and thus prevents the truck from being overloaded.
Wrusch: “The result can be described like this for counterbalance trucks: The higher and heavier the load, the slower the lift. A very effective assistance system that not only makes storage at great heights much easier, but also considerably safer.”
Another innovative system for accident prevention is the Active Load Stabilisation (ALS). An automatic compensation pulse quickly and effectively stops the mast vibrations that occur at great heights, which – in addition to the safety benefit – also reduces the waiting time at the racking up to 80%.
Conclusion
The vision of accident-free intralogistics seems within reach, as the results of the STILL webinar showed. In order to make this a reality, however, not only innovative technical solutions for trucks are needed, but also effective training concepts for warehouse employees to enable them to handle these trucks safely and responsibly.
This is also the purpose of the website specially created by STILL on the subject of safety: www.still.de/safety. Even if the ever more reliable technology can take many decisions away from the operating personnel: industrial trucks are – and will remain in the future – complex tools which safe operation must be properly learned.