The TPPL Battery Choice
27th October 2020
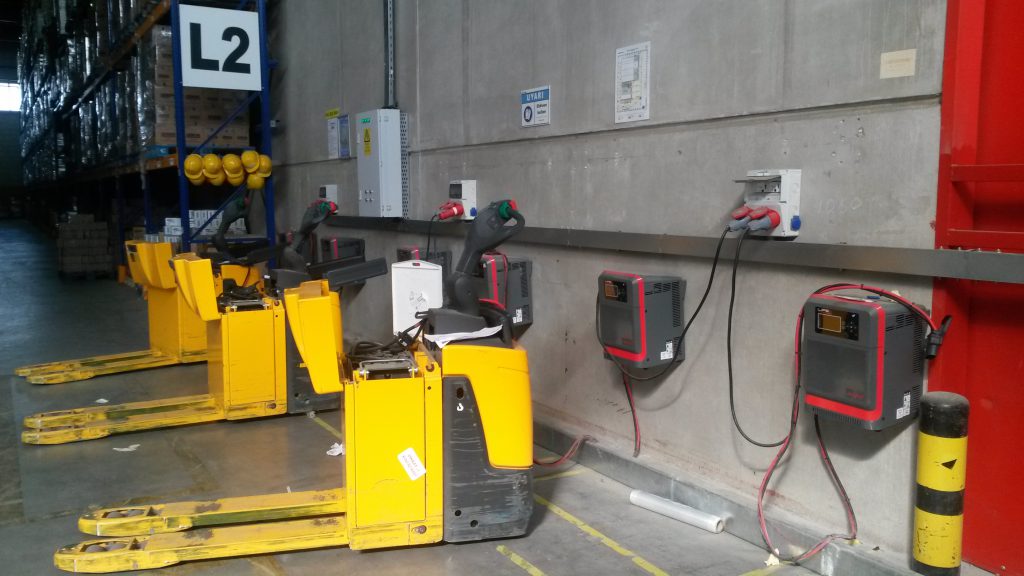
Matteo Todesco of EnerSys argues that TPPL battery technology has broadened battery choice for electric material handling vehicles.
Warehouses and production areas are under increasing pressure to maximise productivity and return on investment. This has led to more attention on the role of materials handling vehicles,
particularly the cost and performance of the batteries and technology that power them. As an example, users of material handling vehicles today will not accept a loss in productivity due to
battery-related downtime. It is simply no longer possible to remove a vehicle from service to charge or change out batteries and perform routine maintenance tasks. In addition, there is a trend to lease vehicles instead of making an outright purchase.
Changing a battery during a lease term is undesirable because the new battery will not be spent by the end of the contract, leading to waste.
Broad technology spectrum
Choosing a battery solution is affected by factors like initial cost, performance, maintenance, charging, stock management and recycling. High performing technologies, such as Thin Plate Pure Lead Batteries (TPPL), offer an attractive alternative to both the traditional solutions of lead-acid or new-comers such as lithium-ion (Li-ion). There are two main types of TPPL battery. The first is a ‘standard’ TPPL solution supplied as a direct alternative to lead-acid batteries. The second is a TPPL solution enhanced with carbon addition. This battery offers a high-performance and cost-effective alternative to Li-ion batteries, especially in heavy-duty applications, thanks to greatly extended cycle life.
Each battery type has different charging and safety requirements, which impact on truck productivity. Flooded lead-acid batteries typically need long charging cycles during or after a shift. This means taking a vehicle out of service or changing the battery. For safety reasons, lead-acid batteries require dedicated charging rooms with ventilation. Regular water top-ups are part of normal operation, but also create the risk of acid spills.
Also, overcharging batteries by 10–20% minimises stratification but adds to the energy demand. All these factors contribute to the total cost of ownership (TCO) for a lead-acid battery setup. Gel type valve-regulated lead-acid (VRLA) batteries have advantages over flooded lead-acid batteries. They do not require water top-up, and their overcharge factor is only 8–10%, thus reducing the energy demand for charging. However, they do not allow for opportunity charging or fast charging with high currents. Batteries must be taken out of service for charging, which takes from 8 to 10
hours.
Read the whole article from our last issue here: https://flickread.com/edition/html/index.php?pdf=5f3d1fcf3160d#38
similar news