Industry View: Getting Full Value from Very Narrow Aisle Layouts
9th March 2020
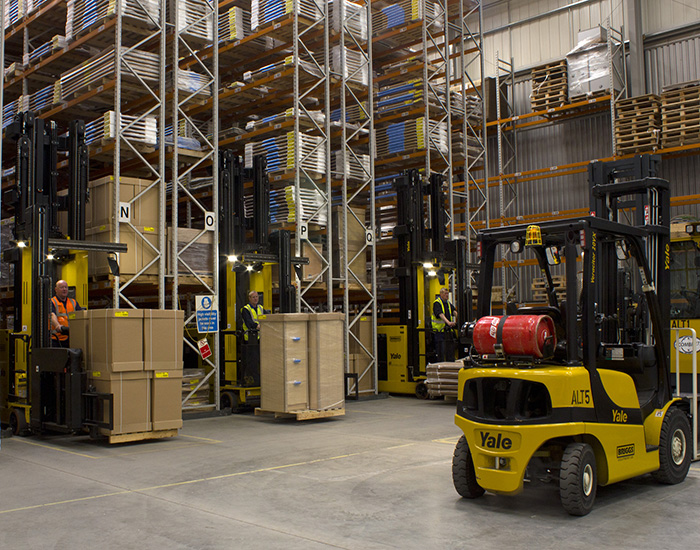
Modern businesses are constantly on the lookout for potential opportunities to maximise their operational efficiency, with the warehouse environment increasingly being targeted as a key area for improvement. These changes often come in the form of reconfiguring an existing warehouse or building a new facility to incorporate a Very Narrow Aisle (VNA) layout.
VNA structures ensure more of the available space in an area is being used, in turn improving productivity and increasing storage space.
Whilst VNA layouts within warehouses are not a new concept, the successful installation of materials handling equipment to operate in these environments requires careful planning and consultation. The time delays and financial implications that come with an unsuccessful VNA installation are significant, which is why it’s crucial for asset management specialists such as Briggs Equipment, to provide expertise in this area.
At Briggs, this activity is headed up by Andy Hancox, VNA Installation Manager who, with support from a nationwide network of technical engineers, manages all VNA installations from concept through to delivery and aftercare. He provided some insight into the complexities of VNA projects and why it’s crucial that Briggs has a dedicated team.
“By their very nature, VNA projects require careful attention to detail to ensure a successful installation and outcome. Typically, our team’s involvement with customers begins at the very beginning of a project where we’ll work alongside our sales team and undertake a specific site survey to help accurately determine the requirements.
“It’s at this point that we can identify any additional support that might be required during the installation and finalise the exact project brief. For example, we sometimes need specialist lifting or access equipment to complete a delivery of a VNA truck. In this instance, it’s crucial that the right machines are sourced well ahead of time to reduce the risk of complications on installation day. The projects we’re involved with are inevitably a real diverse mix, which is why we’re consistently innovating and improving as a team to ensure we’re ready to help no matter the situation.
“In addition to our pre and live installation work, we also collaborate with our customers post-delivery to ensure they are getting the most out of their VNA machine. The large network of mobile engineers that Briggs provides is incredibly important for customers, as they know that we’re able to respond quickly, and that we’ve got the expertise to accurately solve any issues.
“The skillset that we have within our team allows us to provide a complete solution to our customers. They are always very receptive to the fact that we can call upon this specialised resource and it undoubtedly gives them confidence in our capability to deliver complex VNA projects. The successful installations carried by our team have helped cement a number of long-term commercial relationships.”
VNA projects represent a growing area of business for Briggs and the number of installations increases year on year, with 2020 already projecting to be a record period. To adequately adapt to this demand, Briggs provides a truly world-class selection of VNA products and equipment from a range of market-leading manufacturers.
The ongoing feedback that Andy and the team receive from customers is fantastic and further highlights the importance of having dedicated expertise.